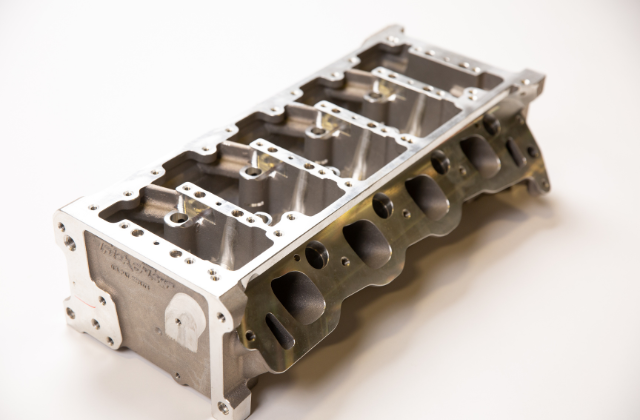
Vacuum impregnation was first developed to seal die casting porosity. The process is used to seal die casting porosity in order to prevent fluids or gases from leaking under pressure.
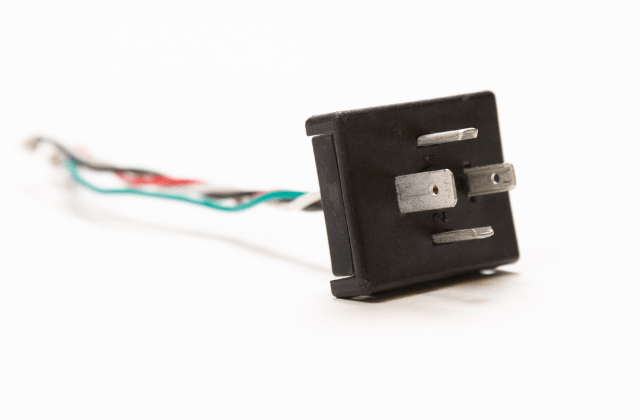
The surge in electronic components has made vacuum impregnation the best process to seal leak paths and prevent corrosion.
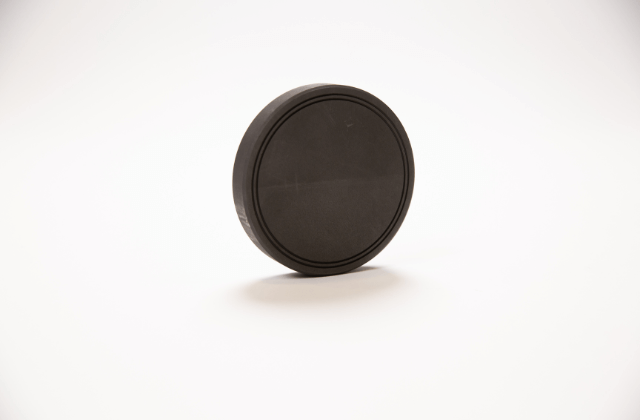
Graphite demand is skyrocketing to meet hybrid and electric vehicle use. Porosity is inherent in graphite, and vacuum impregnation is used to the porosity to ensure the parts are pressure tight.
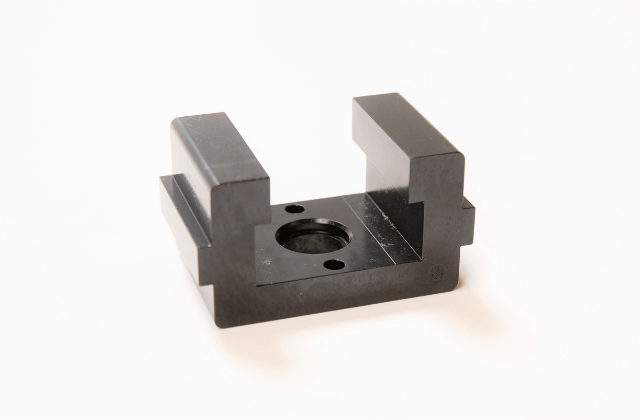
The use of vacuum impregnation in powder metal expands beyond sealing porosity. The process also reduces corrosion, improves machinability, and enhances surface finishing.
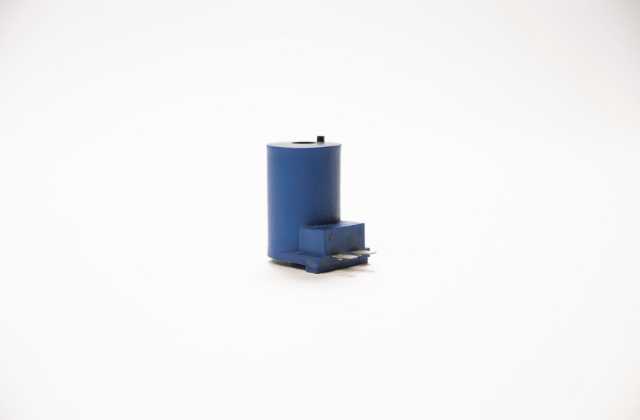
In these parts, metal pins and wires are embedded in the plastic housing. When the parts experience heat during manufacturing or normal use, the plastic and metal expand at different rates, creating microscopic voids between the materials. Vacuum impregnation seals the leak paths by filling the void between the two dissimilar materials.
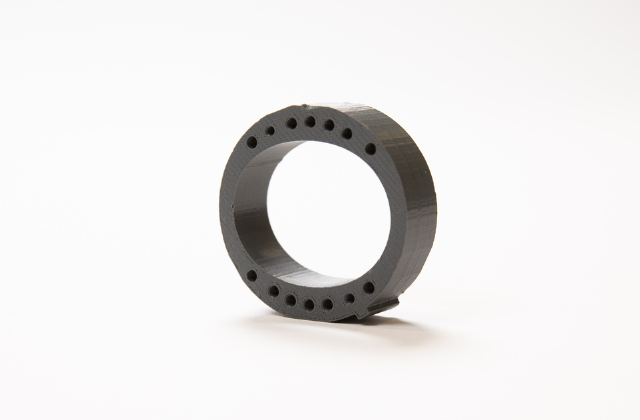
3D printing has streamlined the product development cycle. However, parts created through the process are susceptible to the same porosity that plagues those created through more traditional processes. Vacuum impregnation is used on 3D printed parts to seal leak paths and improve part integrity.