Category Archive: カテゴリーなし
新車には平均して、約40個の電子制御機器、5マイルの配線、1000万行以上のソフトウェア・コードが搭載されています。自動車に搭載される電子機器/コイル/ワイヤーは、燃料効率や顧客のニーズに応えるべく、今後も増え続けると予測されます。
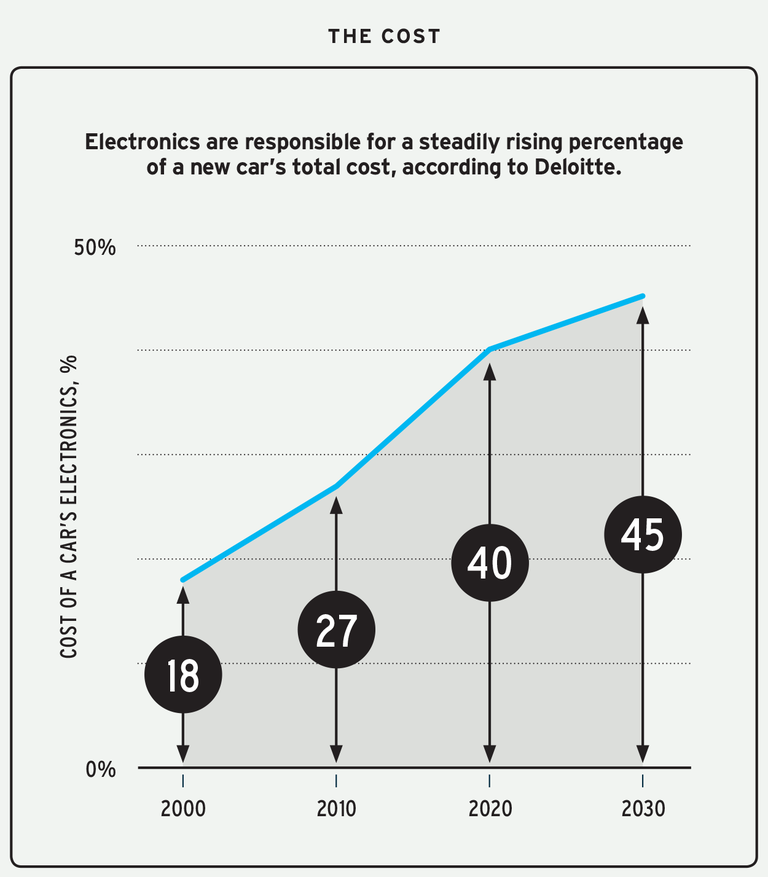
Source: Car and Driver
これらの部品では、金属製のピンやワイヤーがプラスチック製ハウジングに埋め込まれています。製造時や使用時にこの部品に熱が加えられると、プラスチックと金属はそれぞれ異なる速度で膨張してしまいます。この膨張により、材質と材質の間に微小な空洞が発生するのです。これらの漏れ経路の発生は回避できないものですが、シールを行わないと現場で不具合を生じさせるおそれがあります。自動車用電子部品のプロセスにおいて、これらの部品には著しい膨張が発生してしまうため、漏れ経路のシールが非常に重要となってくるのです。
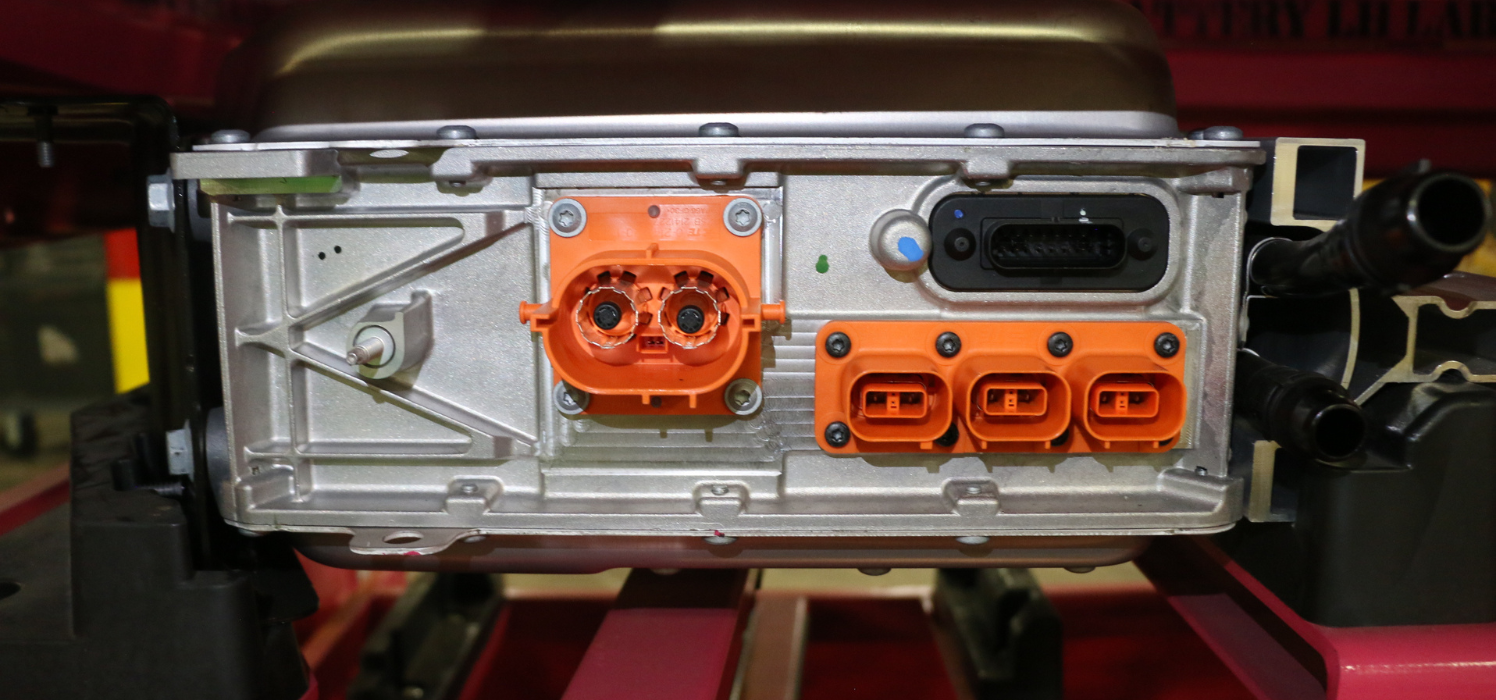
これらの空洞をシールする方法として一般的な方法が2つーポッティング法と真空含浸法ーが挙げられます。ポッティング法は一般的な方法ですが、真空含浸法に比べて不利益となる点もあるのが現実です。ここで、電子機器のシールを行う際はなぜ真空含浸法が推奨されるのか、3つの例を挙げて説明します。
真空含浸法
真空含浸法 は、2つの異なる材質間の空洞を埋めることで、漏れの経路をシールする表面化のプロセスです。シールを行わなければ、流体がコネクターに侵入するおそれがあります。真空含浸は、漏れ経路をシールすることで流体の漏れを防止します。
耐腐食性
酸化あるいは亜鉛メッキによる腐食は、通電能力の低下や部品の不具合につながります。真空含浸法を行うことで、酸素や湿気が侵入する漏れ経路をシールして腐食を防止することができます。
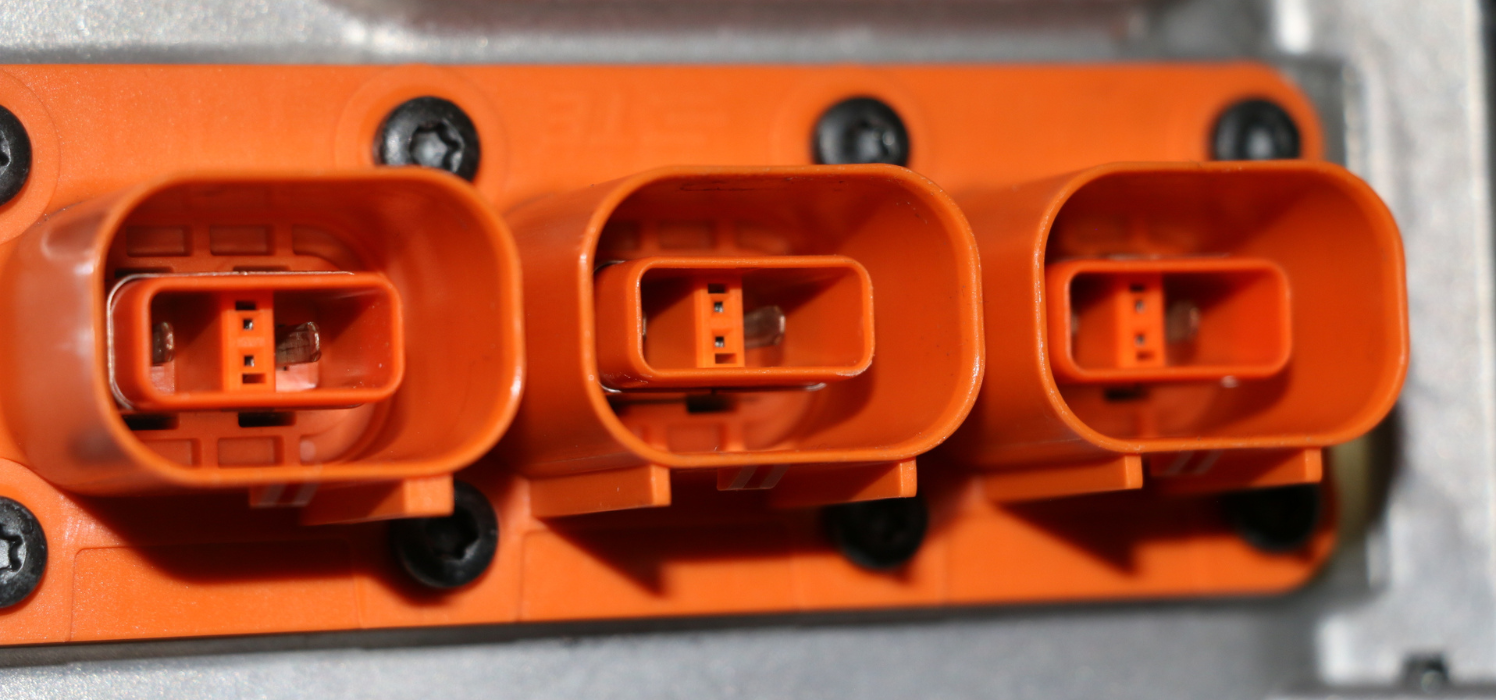
自由設計
真空含浸を行っても、部品の寸法は変わりません。したがって、オリジナルの形状に合わせた設計が可能になります。プロセス実施後も部品表面にシール剤を残さないので、寸法公差を考慮する必要がありません。
まとめ
自動車エレクトロニクスの急速な発展により、ポロシティ(穴孔)のシールが重要視されています。ポロシティ(穴孔)の適切なシールを行うことで、部品の品質が性能要件を満たします。真空含浸法は、漏れ経路のシール、耐腐食性に最も効果的なソリューションで、かつ自由設計も可能にします。
消費者ニーズの変化に伴い、環境への配慮は企業にとって必要不可欠なものとなりました。その結果、アルミニウム製ダイ・キャスト(圧力鋳造)を使用しているOEMやメーカーは迅速な対応を行い、持続可能な製造プロセスがますます一般的になってきました。
持続可能な製造プロセスは、製造廃棄物や環境への影響を最小限にすることを目的としています。より環境に配慮した製品設計や製造プロセスを採用することでこれを実現しています。持続可能な製造プロセスは、OEMからサプライヤーまで、プロセスと材料の両方で展開しています。例えば、真空含浸といったプロセスや、そのプロセスで使用されるシール剤などの材料などが挙げられます(画像1)。
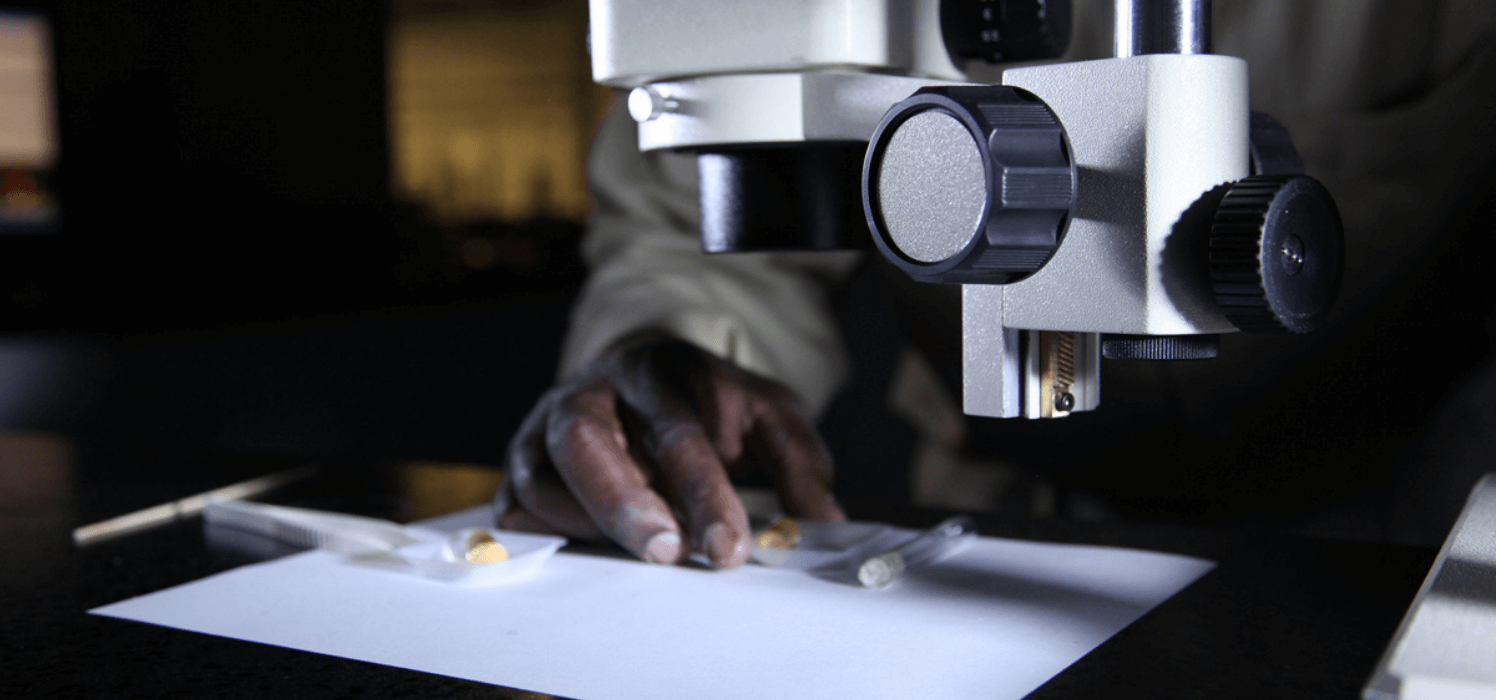
画像1:環境に配慮した製品設計や製造プロセスの採用により、持続可能な製造プロセスが実現
真空含浸とは
真空含浸とは、鋳造プロセスで発生した漏れの経路をシールする、影響の少ない方法です。具体的には、鋳物の壁を破り、製品の不具合につながるおそれのある、内部で相互につながったポロシティ(穴孔)の経路を、真空含浸法でシールします。この方法では、寸法や機能特性を変えることなく、ポロシティ(穴孔)をシール剤でシールすることができます。
真空含浸とは、 鋳物のポロシティ(穴孔)をシールすることによって、従来なら廃棄されていた鋳物を利用可能にするものです。その結果、ほぼ全ての部品を製造ラインに戻すことができ、廃棄量の大幅な削減およびリソース管理を実現します(画像2)。

画像2:ダイ・キャスト(圧力鋳造)のポロシティ(穴孔)をシールすることで、従来なら廃棄されていた鋳物を利用可能に
回収可能なシール剤の利点
環境の持続可能性に貢献するのは、真空含浸プロセスだけではありません。真空含浸プロセスに使用できる材料ー特に回収可能なシール剤ーも環境保全に貢献しています。最も一般的に使用されている回収可能なシール剤の主な利点を3つご紹介します。
- 回収(Recover) – 回収可能なシール剤は洗浄前に自動的に回収され、すぐ再利用できるよう含浸モジュールに戻されます。回収後の純粋なシール剤は、シール剤のコンタミネーションのリスクを排除することができます。
- 再利用(Reuse) – 回収可能なシール剤は、含浸プロセスの間、オリジナルの配合を維持します。他のシール剤とは異なり、再構成するための大きな資本を必要とするプロセスを経る必要がありません。したがって、洗浄水やその他のコンタミネーションを取り除くといった余分なプロセスなく、何度も再利用することができるのです。
- 削減(Reduce) – 部品の効果的な取り扱いおよびシール剤の純度維持によって、シール剤の消費量を削減します。これによって、サイクルが1回目でも50回目でも同様に、部品がベタベタしたり剥がれてコンタミネーションの原因になることなく、部品の適切なシールを確実に行います。シール剤は洗浄ステーションの前で取り除かれるため、洗浄水と乳化することがありません。部品は清浄な水でクリーニングが行われ、シール剤が残留することはありません(画像3)。
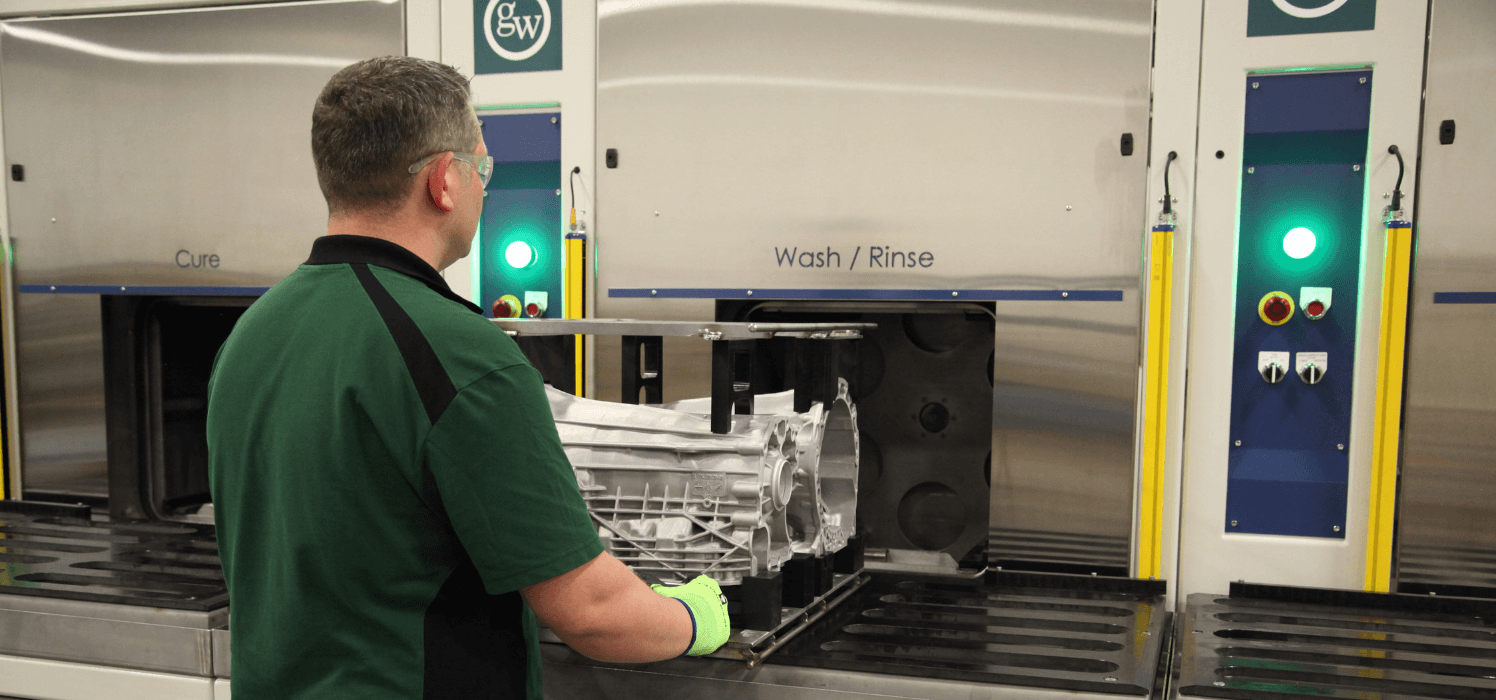
画像3: シール剤は洗浄ステーションの前で取り除かれるため、洗浄水と乳化することがありません。
まとめ
アルミニウム製ダイ・キャスト(圧力鋳造)のシールを行う際、回収可能なシール剤を使用することは大きな利点となり得ます。このシール材は非常に環境に配慮した製品です。安全性と環境に対するリスクを軽減しながら、鋳造の回収率を最大化することができるのです。
自社で装置を保有/運用する場合と、外注する場合のメリットの違いは、流通/品質/部品にかかるコスト削減が挙げられます。これらのコスト削減は、企業の収益向上に直結します。これは、真空含浸装置についても当てはまります。しかし、限られた設備投資予算の中で、多くのプロジェクトやプログラムに関しても考慮しなければならず、真空含浸装置への投資は難しいことのように思われます。それ故、多くの企業が真空含浸プロセスを外注するという選択を当たり前に行っているのが現状です。
真空含浸装置の調達方法に関わらず、最も高額なコストは装置自体ではなく、ポロシティ(穴孔)のために廃棄される部品と付加価値のない外注費用なのです。適切な真空含浸プロセスおよびその装置を選定することは、生産性の最大化、品質の改善、コスト削減につながります。
ここでは、財務目標と経営目標を整合させつつ、真空含浸装置を導入するための方法を4つご紹介します。
即金での導入
購入時に即金で支払い(買い切り)、装置を所有する方法です。この方法は、先行資本が確保できている長期的プロジェクトに採用されます。資本、装置、光熱費の額によって異なりますが、総費用を一番低く抑えられる選択肢です。多くのOEMやティア・ワン・サプライヤーではこの方法を好んで採用しています。
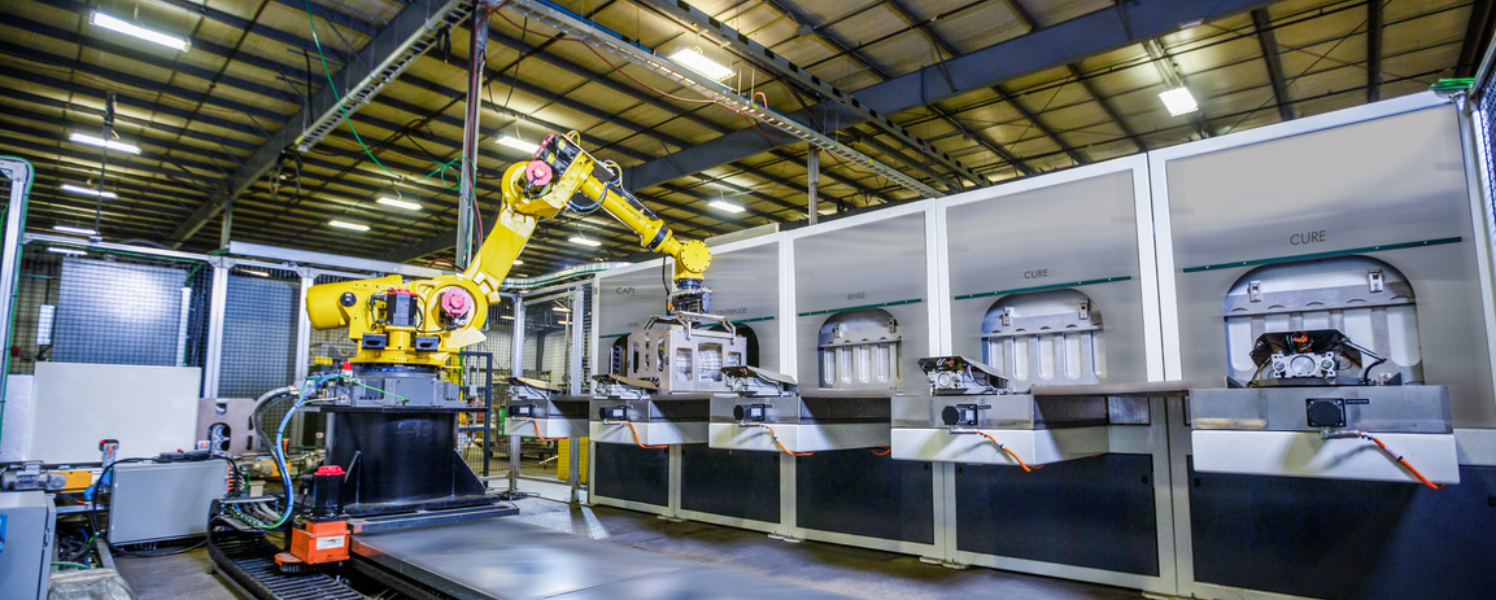
キャピタル・リース
企業が装置をリースして運用し、リース期間終了後に購入できる方法です。この方法は、プロジェクト開始時に利用できる予算が限られている長期プロジェクトに採用されます。企業は毎月のリース金額および利息を支払います。
この装置は賃借人の所有物とみなされるため、固定資産として計上し、減価償却処理を行います。リース債務は、貸借対照表に負債として記載され、支払いに応じた利息が認められます。減価償却費および利息は税額控除の対象となり、減価償却費はボーナス減価償却として計上されます。
オペレーティング・リース
装置の使用は許可されますが、所有権は発生しない方法です。リース期間終了後は、賃貸人はその装置を保持する、あるいは適切な市場価格で賃借人に売却する方法です。この方法は、短期プロジェクトによく採用されています。キャピタル・リースと同様、企業は毎月の金額および利息を支払います。
装置の所有権は賃貸人にあるとみなされるため、企業はこの契約を賃貸として計上します。支払いは、賃借料として損益計算書に記載され、税額控除の対象となります。
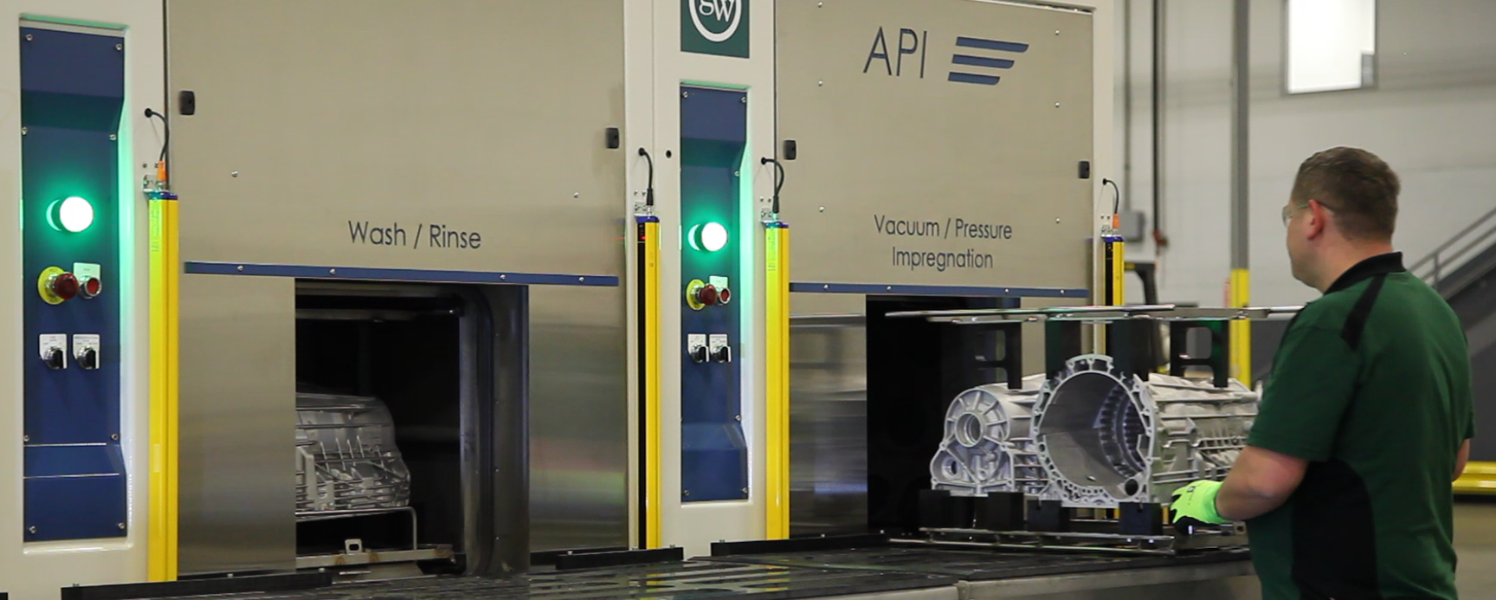
Equipment as a Service (EaS)
装置の所有権はメーカーにありつつ、企業が装置の運用を行う方法です。メーカーは「使用料」として費用の請求を行うため、企業は運用費として計上することができます。メーカーは装置/トレーニング/メンテナンス/修繕をすべて提供します。企業は、運用/消耗品/光熱費を負担します。契約期間終了後、企業はこの装置を返却します。この場合も、使用毎に発生する料金は、営業費用として控除の対象となります。
EaSの利点は、生産と費用の整合が可能であることです。費用は処理能力に直結しており、この費用は減価償却費の対象とはなりません。
まとめ
真空含浸装置の購入/リースに関するさまざまなオプションをご用意しています。お客さまの財政状況に合わせた適切な購入オプションを選定することが重要です。適切な選定によって、部品の回収率を最大限にし、コスト削減、収益性の向上が実現するのです。
2008年、北米のバイク・メーカーのOEMが製造コストの削減に向けて、真空含浸技術をアウトソーシングからインソーシングへ、つまり自社内で実施することを決断しました。OEMは、複数のシール剤や装置についての調査を行い、廃水排出の削減、高い鋳造シール率、最小限の調整/メンテナンス/修理などが謳われていた装置の購入を決定しました。選定した装置は、リサイクルしたシール剤を使用するものでした。
課題
使用してしばらく経った頃、同社は購入した製品が実際とは異なることに気が付きました。リサイクル可能であるはずのシール剤の化学性質は時間とともに変化し、回収結果も変わってきたのです。リサイクル可能なシール剤は、その性質上、含浸処理の際に水と混合する必要がありました。最初、シール剤は純粋でしたが、一度水に触れるとその特性が損失し、オリジナルの配合に戻ることはなかったのです。
また、シール剤の効果を維持するためには、洗浄水の調整剤が必要でした。しかし、このシール剤の効果を得るためには、毎日正確な比率で調整剤を加えなければならなかったのです。比率が不正確だった場合、シール剤の安定性が失われるのです。同社は、洗浄/硬化モジュールに化学物質が過剰に投下された場合、部品のコンタミネーションが進行し、システム損傷を引き起こすことを突き止めました(図1)。
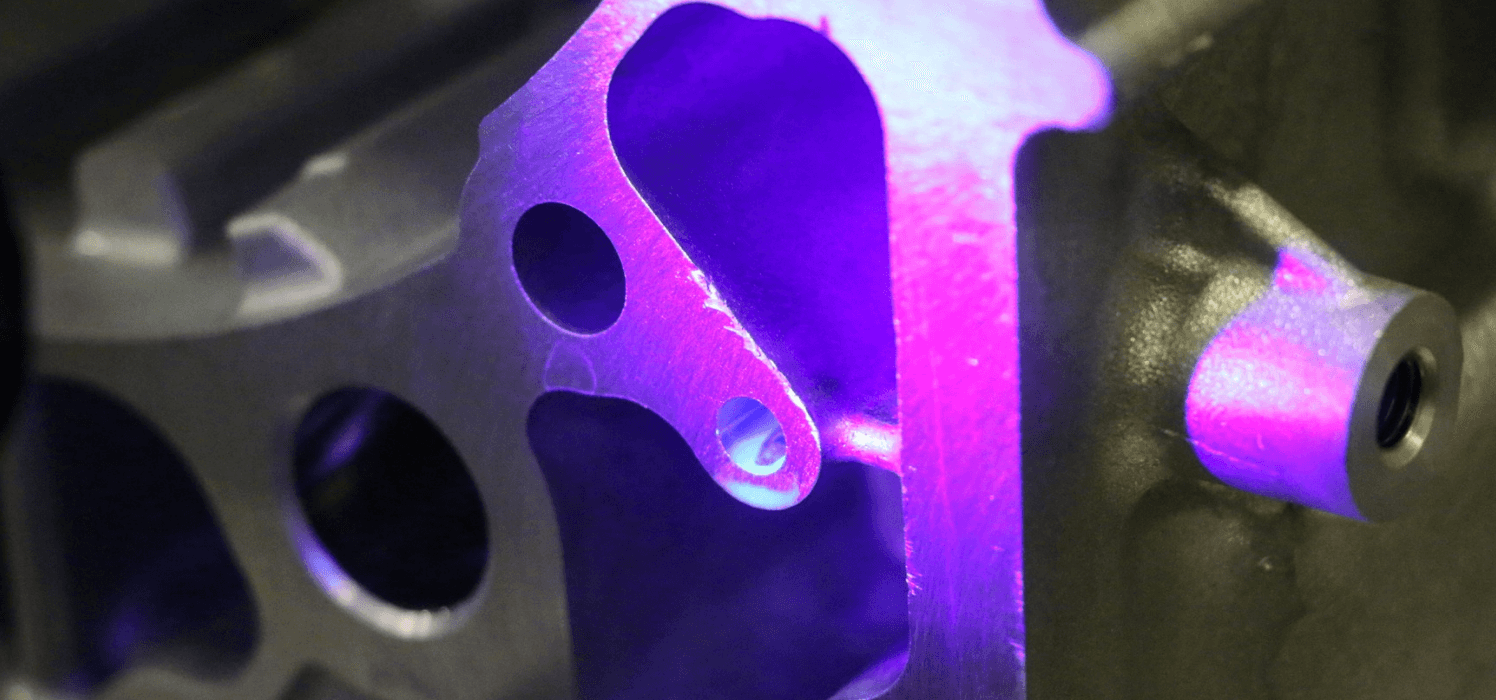
図1: 洗浄/硬化モジュール内の過剰なシール剤による、部品のコンタミネーションの進行
このシステムは非常に高価なものです。同社では、廃棄部品、修理、メンテナンス、人件費、シール剤用消耗品、シール剤サポート用化学物質など、100万米ドル以上の予算を組んでいました。このシステム管理を行う費用は、含浸プロセスをアウトソーシングする費用を上回るものでした。
同社は真空含浸の方法を抜本的に変えなければならないと判断し、軽量のクランクケースを新しく開発しました。それは、すべての部品をシールする必要があるものでした。これまでの経験やデータから、新しい含浸システムを選定する際には、3つの大きな課題を解決する必要がありました。
- メンテナンス費用 : 従来のシステムでは、コンポーネントの消費が非常に多い状態だったため、より簡単に、メンテナンス頻度が少ないシステムが必要でした。
- シール剤の管理 : リサイクル可能なシール剤は、過剰なテストとメンテナンスが必要だったため、複数の部署にまたがる毎日のメンテナンスの必要がなく、元の化学成分を維持するシール剤が必要でした。
- 回収不良 : 従来のシステムでは鋳造品の約14%が不良品で、回収できなかった部品はすべて廃棄していました。廃棄鋳造の費用は、約96.7万米ドルにも上っていたため、回収可能な鋳造品をさらに増やす必要がありました。
ソリューション
GW社は、CFi(連続フロー式含浸)システムの、DVP(ドライ真空/圧力)プロセスおよび回収可能なシール剤(95-1000AA)の提案を行いました。
CFiでは、GW社のDVP(ドライ真空/圧力)含浸プロセスを採用しており、高速で高い真空度を取り入れて、穴孔から空気を排出します。シール剤をチャンバー内に移動した後、高圧でシール剤を鋳造内に深く押し込みます(図2)。
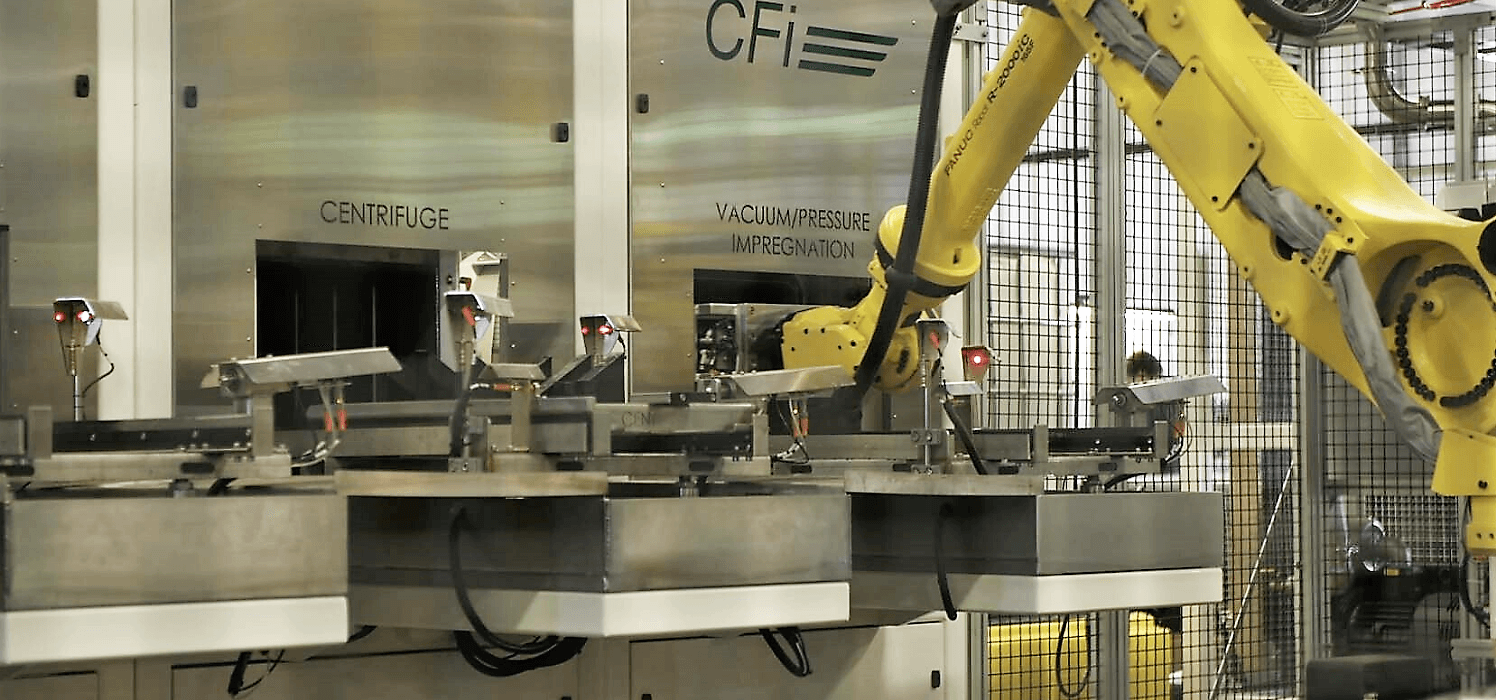
図2: GW社は、メーカーの課題を解決すべく、CFi(連続フロー式含浸)システムを提案
回収可能なシール剤(95-1000AA)は、処理が終了するまで純粋な状態を維持しています。CFi含浸モジュールは、シール剤をオリジナルの配合で回収できるよう設計しています。部品の含浸処理が終わると、部品は遠心分離機にかけられ、未使用のシール剤が回収されます。未使用のシール剤はシール剤用容器に戻され、次回のサイクルに使用されます。純粋なシール剤を保持できるため、添加物や過剰なメンテナンスを必要とせずとも、回収率を最大限にすることができるのです。
含浸プロセスの後、部品はCFiの洗浄/硬化ステーションに送られます。余分なシール剤がないため、洗浄水はクリーンな状態を保つことができます。これにより、部品の適切な洗浄が行われ、コンタミネーションの防止にも繋がるのです(図3)。
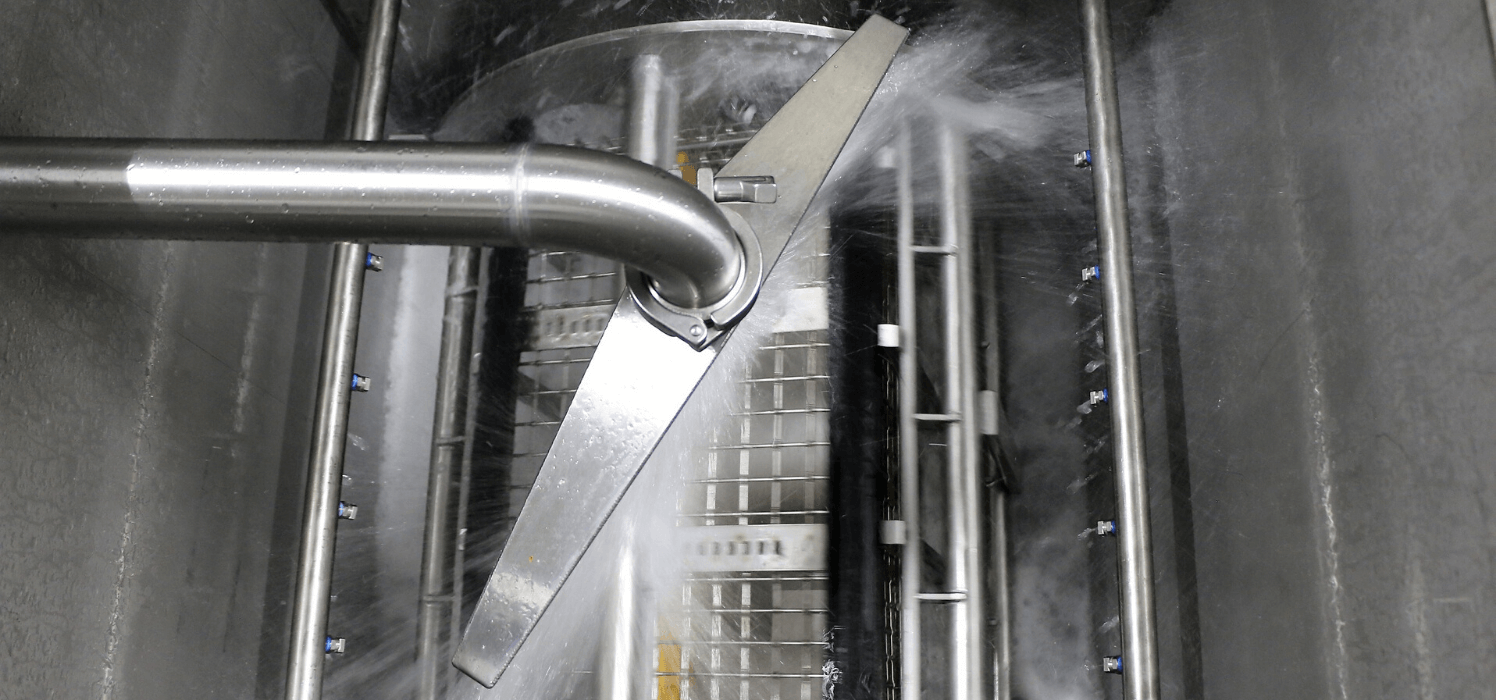
図3: クリーンな洗浄水が部品を適切に洗浄し、シール剤のコンタミネーションも発生しない
CFiというシステムは、メンテナンスおよび稼働を最優先に考えた設計を行っています。内部コンポーネントは、製造工程を中断することなく、簡単にメンテナンスが実施できるよう配置されており、後方のアクセス・パネルから主要コンポーネントのメンテナンスを行います。クイック・コネクツ継手を採用しているため、特殊工具を使用することなく取り外しが可能で、手でメンテナンスを行うことができます(図4)。各モジュールには定格ラインのディスコネクトが装備されており、メンテナンスの際にシステム全体を停止する必要がありません。
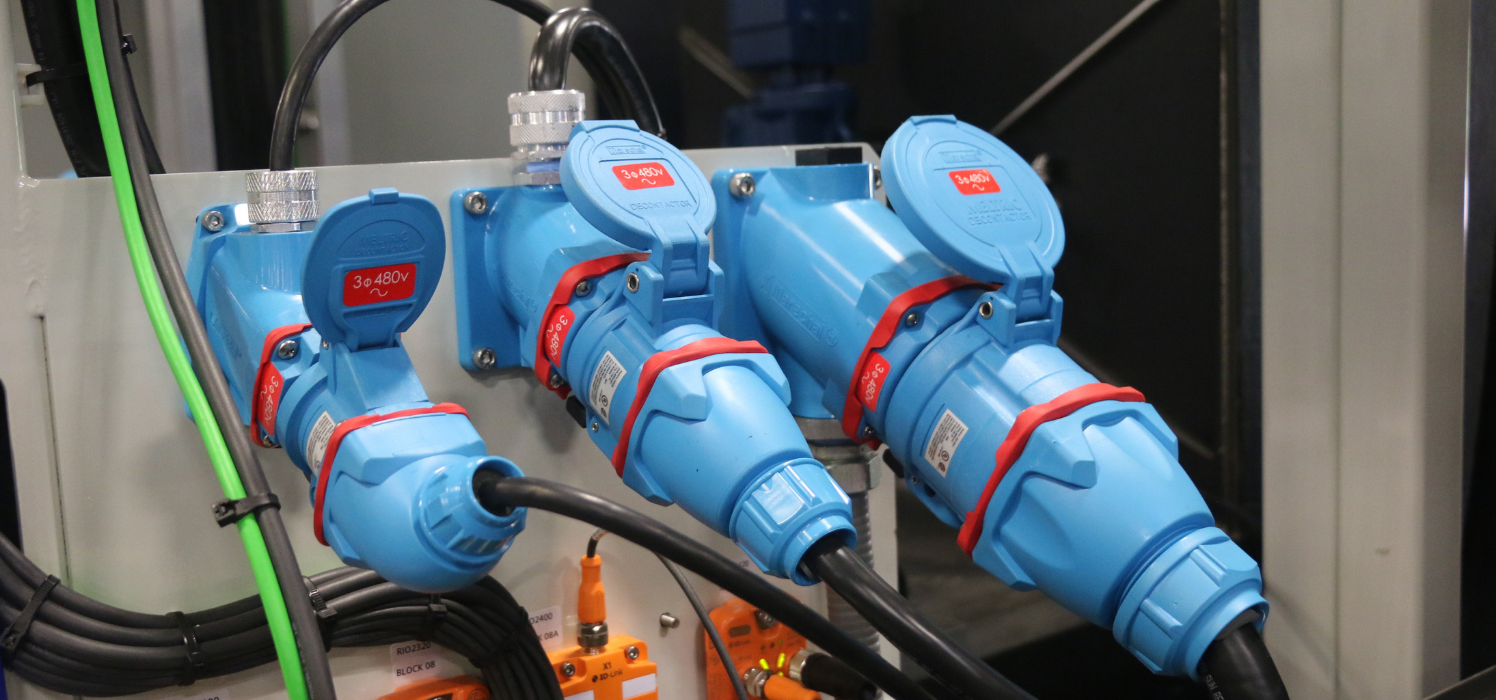
図4: 特殊工具を使用することなく、容易にCFiのメンテナンスを行うことが可能
このシステムとシール剤の選定は最適なソリューションでした。しかし、メーカーはこの技術とシール剤についてさらなる詳細な説明を希望したため、GW社は、CFi と回収可能なシール剤を取り扱うサービス・センターを紹介しました。
メーカーは、サービス・センターを見学し、その技術についての説明を受けました。そこで、このプロセスおよび回収可能なシール剤は純粋な状態が維持されていること、メンテナンスや作業者が関わる頻度が低いことを実際に確認することができました。メーカーは、CFi の処理能力、効率、シンプルさに非常に感銘を受け、また提示されたデータも詳細に検討した結果、CFiの購入を決断したのです。
結果
CFiの導入後、オペレーションとメンテナンスのトレーニングが実施され、システムはすぐに稼働を開始しました。それ以来、メーカーがこれまで抱えてきた課題は全く発生していません。
- メンテナンス費用の削減 : メンテナンスおよび予備部品にかかる費用が、年間約5万米ドル削減できる見込みです。
- 効率的で簡単なシール剤の管理 : 洗浄水用の調整剤を購入する必要はなく、シール剤のメンテナンスや監視が大幅に削減されます。年間約2万 米ドル削減できる見込みです。
- 鋳造品の回収率向上 : CFiのFTT(First Time Through)率は、99%でした。以前の回収率より14%もアップしたことになります。これにより、年間約63万米ドルのマイナス幅を補うことになります。
トータルで、コスト削減と回収率アップにより、年間約68.5万米ドル節約できる見込みで、投資費用は24カ月以内に回収可能です。このCFiの生産性およびメンテナンス性の高さは、メーカーが当初抱いていた真空含浸のイメージを一変させるものでした。
まとめ
最適の含浸プロセスおよびシール剤の選定は、自社で真空含浸装置を購入する際に非常に重要です。購入後は、取り返しがつきません。このメーカーは、デュー・デリジェンスの観点からデータを精査し、ニーズに合致した適切な装置とシール剤の選定を行いました。回収可能なシール剤を使用するCFiは、コスト削減、品質向上、効率改善を生み出し、同社の含浸プロセスを一変させたのです。
効率的な製造フローを確立するには、部品や材料がスムーズに流れ、遅れが最小限になるよう、作業ステーションや装置を順番に配置することが非常に重要です。効率的な生産フローを導入することで、生産性や柔軟性が向上し、必要な資本の削減にもつながります。
表面工学の業界屈指の企業である Anoplate 社は、生産フローに関する問題を抱えていました。同社は、多孔質材料におけるガス放出、耐薬品性、前処理のブリード・アウトから発生する破損の可能性を排除し、かつ漏れ経路のシールを行う真空含浸サービスを提供しています。Anoplate社は、航空宇宙、防衛、情報技術、レクリエーションなどの分野で活躍する世界的に有名な大手企業向けの、高価値で複雑なダイ・キャストの加工を行っています。鋳造は通常、小さなブラインド(ドリル加工なし)・タップ付きの薄肉のものです。
課題
Anoplate社のオペレーションは、2棟の建物で展開しています。本社ビルにはオフィスがあり、また真空含浸処理も行っています。通りを挟んだ2つ目のビルでは、蒸気脱脂とメッキ処理のプロセスを行っています。ダイ・キャストの工程には、自社製のバッチ式含浸装置を使用しています。バッチ式とは、様々な部品を集めて大量に処理するシステムです。 含浸処理の前には、まず脱脂処理を行います。
同社は真空含浸法に精通してはいましたが、バッチ・システム特有の以下の3つの制限により、複雑な鋳物を効率的に処理することができませんでした。
- コンタミネーション : クリーンなシール部分を完成させるには、余計な手順が必要でした。貫通したテープ穴やブラインド・テープ穴に、硬化したシール剤やオイルが残留し、工程終了後には作業者が機械やテープ穴を手洗いしなければなりませんでした。また、多くの部品では含浸が2回必要でした。
- シール剤の使用 : システム処理用バスケットは、シール剤の「引きずり出し」の原因となることが多くありました。この引きずり出しにより、シール剤の使用量が増え、引いては材料費の増加につながっていたのです。
- 非効率的な生産フロー : 非効率的な生産フロー:プロセス経路(脱脂、含浸、メッキ処理、仕上げ)では、建物の間を部品が何度も行き来するため、常に輸送用ダンネージ材への出し入れをする必要がありました。処理数が増加するにつれ、部品損傷のリスクも増え、在庫管理が不十分となり、プロセスにかかる費用も増大していました。
ソリューション
同社の課題に対応するため、GW社はカスタマイズされた、無駄のないフロント・ローデイング方式のHVLV真空含浸システムを提案しました。
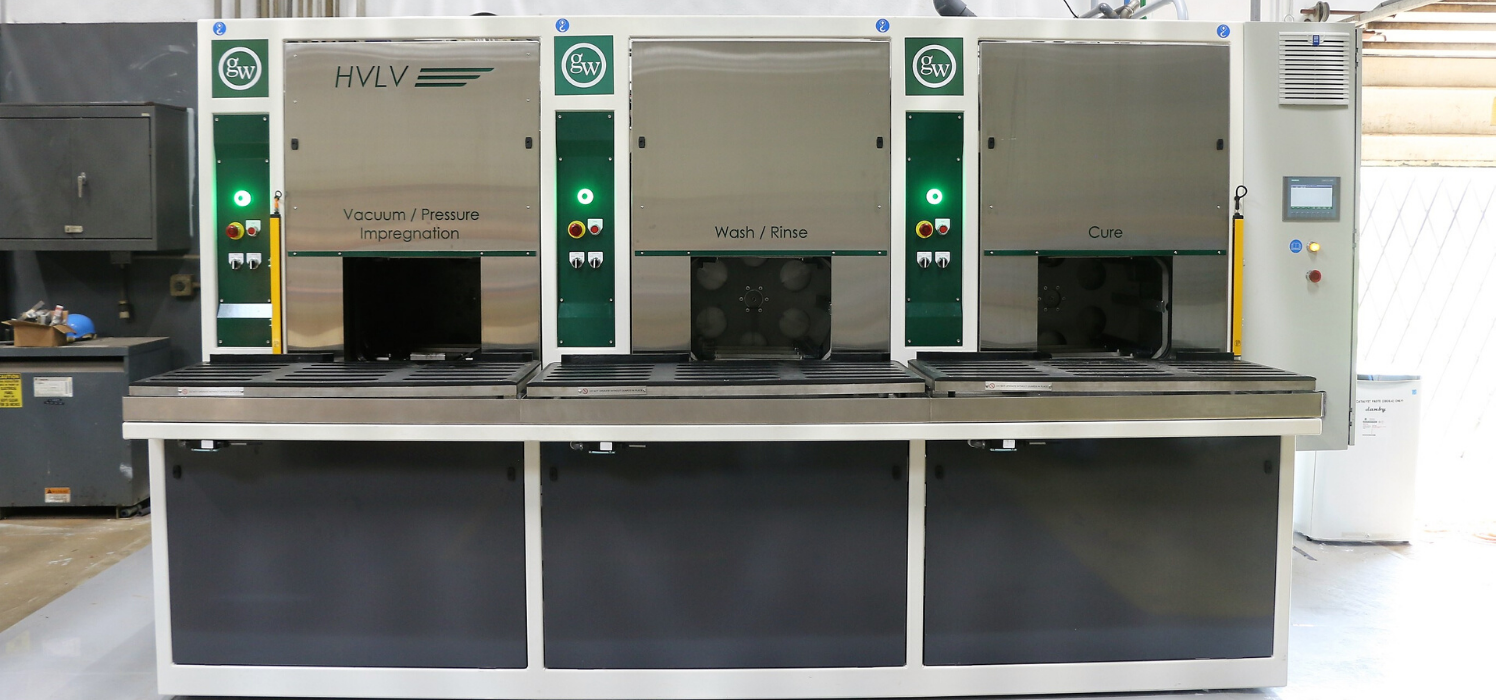
コンタミネーションの除去に向け、GW社は、1サイクルあたりの鋳造数を最大化し、重要な機械機構を保護するような、カスタム化したフィクスチャーの設計を行いました。HVLVの高度な洗浄サイクルは、ブラインド穴や機械機構からシール剤を洗い流すため強力洗浄を行うようにプログラムされました。
含浸処理を行った後は、部品を遠心分離し、未使用のシール剤を回収します。回収されたシール剤はシール剤用容器に戻され、次のサイクルで使用します。HVLVでは洗浄を行う前に未使用のシール剤を回収するので、シール剤の引きずりやコンタミネーションの恐れがありません。
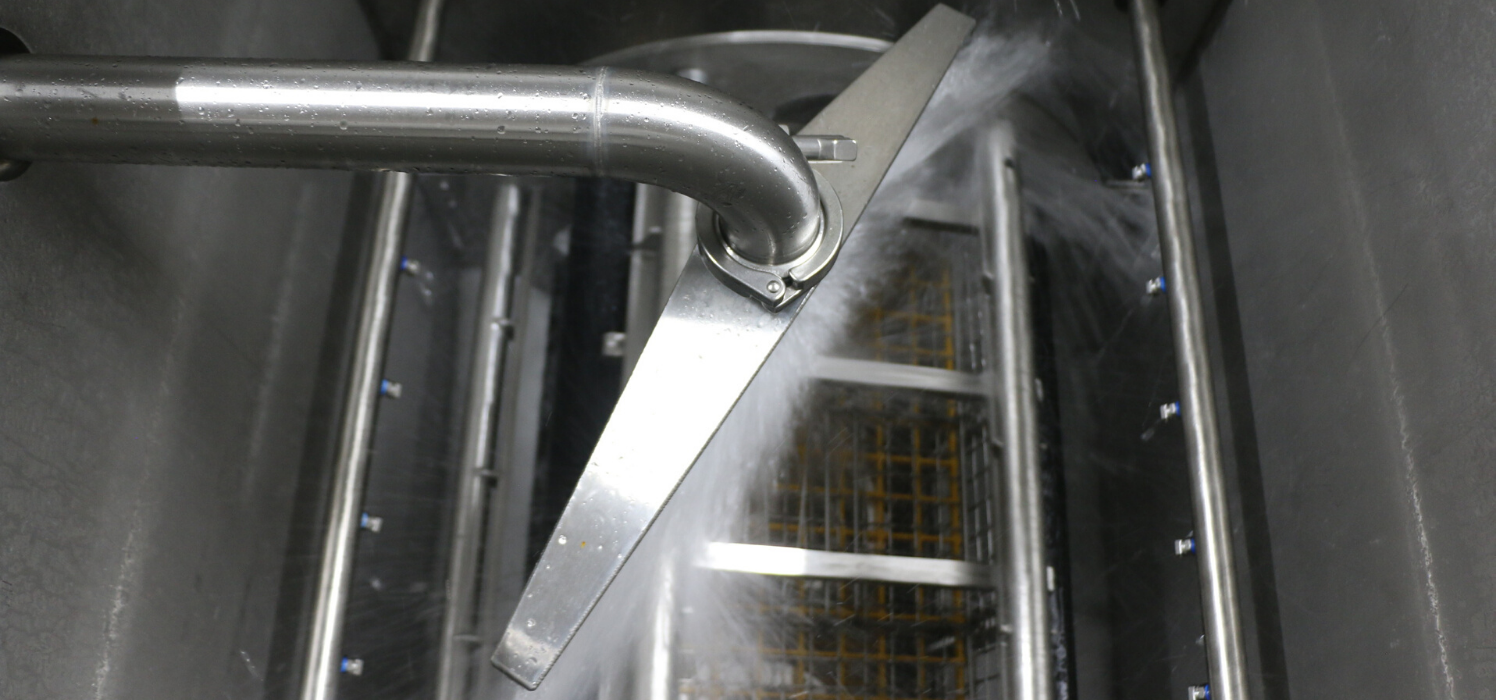
Anoplate社は、同システムをメッキ処理作業と同じ建物内に導入することを希望していました。そこでGW社は、製造ラインに合わせたHVLVの設計を行いました。HVLVモジュラーのフットプリント(設置面積)は96 平方フィートで、フロアの改修は必要ありません。さらにGW社は、HVLVがAnoplate社のオペレーションの順番とどのように統合できるかを調査した結果、HVLVを導入することで従来の脱脂プロセスを削除できることが判明しました。
この完璧なシステムに対して、Anoplate社は実際の投資前に非常に厳しいサンプル試験を実施しました。サンプルは、Anoplate社に提案したものと同じ機械を使用して、GW社の本社にてHVLVの処理を行いました。その結果、HVLVはリーク経路をシールするだけでなく、コンタミネーションを削除し、シール剤の使用量も削減したことが判明したのです。さらに、HVLVモジュラーのフットプリント(設置面積)が、既存の生産ラインに対して簡単にフィットすることが実際に確認できたのです。これらの試験の結果により、Anoplate社はHVLVの採用を決断したのです。
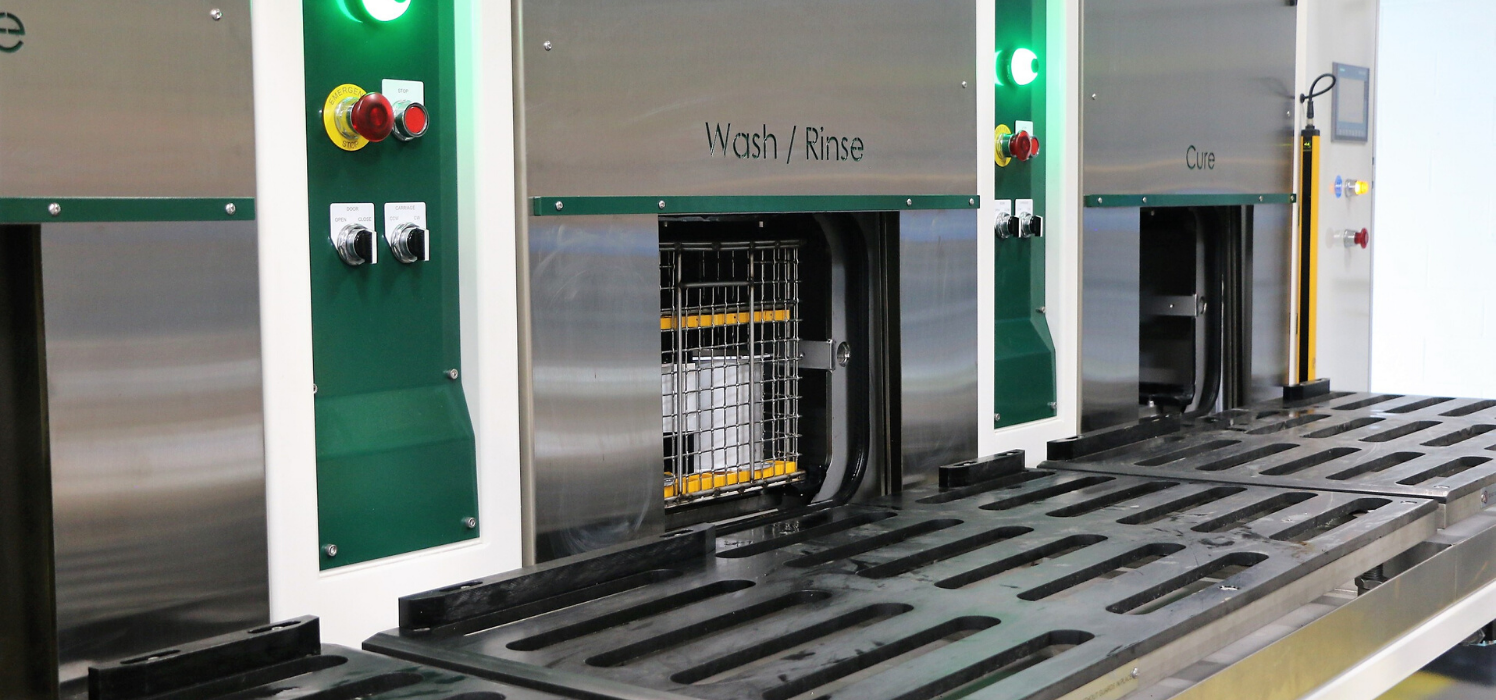
結果
HVLV導入後、オペレーションおよびメンテナンスのトレーニングが実施され、たった2週間以内にシステムが再稼働したのです。それ以来、Anoplate社の課題はHVLVが解決し続けています。
- コンタミネーションの除去 : システム内のカスタム化したフィクスチャーおよび徹底した洗浄により、すべての部品が不具合なく処理され、シール剤の残留コンタミネーションの後は確認されませんでした。
- シール剤の使用を最小限に抑制 : シール剤の「引きずり出し」が大幅に減少し、シール剤にかかる費用50%も削減されました。
- 生産フローの改善 : HVLVはメッキ施工の工程と共に稼働しています。含浸処理を行う装置に直接部品を輸送することで、人件費を50%も削減し、また生産性も30%向上することができました。
「我が社が抱えていた課題に対して、HVLVは非常に効果的なソリューションでした。私たちが保有していた高度な製造環境を活かした、比類なき品質の製品の製造が可能になりました」Anoplate社のエンジニアリング担当副社長Jesse Campbell氏はこのように述べています。「またこのシステムは、従来の含浸装置のイメージを一新してくれました。シンプルな操作性、洗練されたモダンな外観をも我々は手に入れたのです」
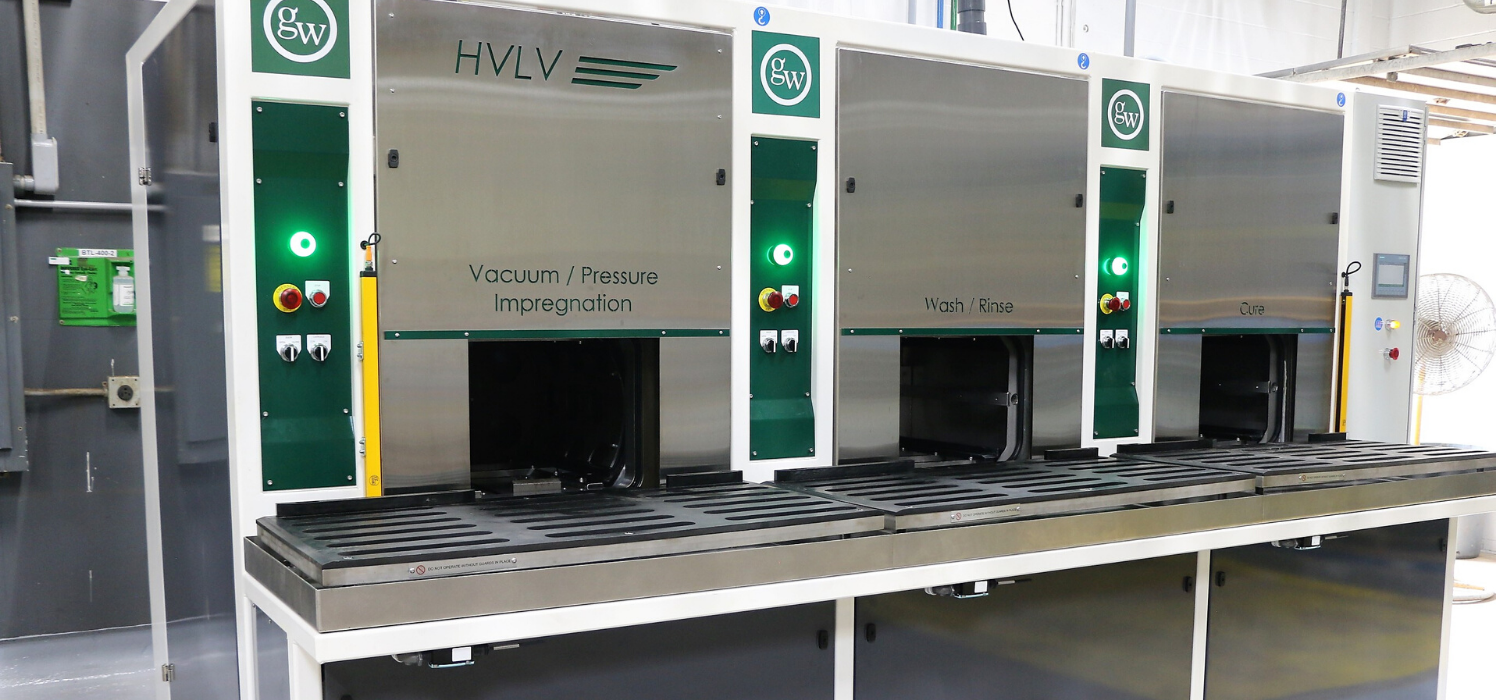
最後に
HVLVの導入によって、Anoplate社の真空含浸サービスの競争力は更に増したといっても過言ではありません。コスト削減、品質向上、効率化により、真空含浸ビジネスに変革をもたらしたのです。
ポロシティ(穴孔)は、鋳物中の隙間や孔と定義されます。しかしこの定義は、ポロシティ(穴孔)の根本的な原因については言及されておらず、その方向性も示されていません。鋳物のポロシティ(穴孔)は、金属が液体状の時に、ガスや凝固収縮が発生することで引き起こされます。 鋳物に耐圧性が必要な場合、ポロシティ(穴孔)によりガスや液体が部品から漏れる可能性があります。さらに、ポロシティ(穴孔)は鋳物の強度にも影響を及ぼします。ここでは、ガスによるポロシティ(穴孔)と引け巣の違い、およびポロシティ(穴孔)をシールするベスト・ソリューションについてご紹介します。
ガスによるポロシティ(穴孔)
概略
ガスによるポロシティ(穴孔)とは、液体状の金属内で、鋳型ガスや炉心ガスが滞留することによって発生するポロシティ(穴孔)です。鋳型キャビティには空気が存在しており、金属がキャビティに充填される際、空気が簡単に内包されてしまいます。キャビティに金属を充填する時に、この空気は高圧の小球体状にて飛散します。
形状
ガスによるポロシティ(穴孔)は、一般的に内面がスムーズな気泡のような形状です。常に浮遊しており、鋳物の上部周辺に見られます。
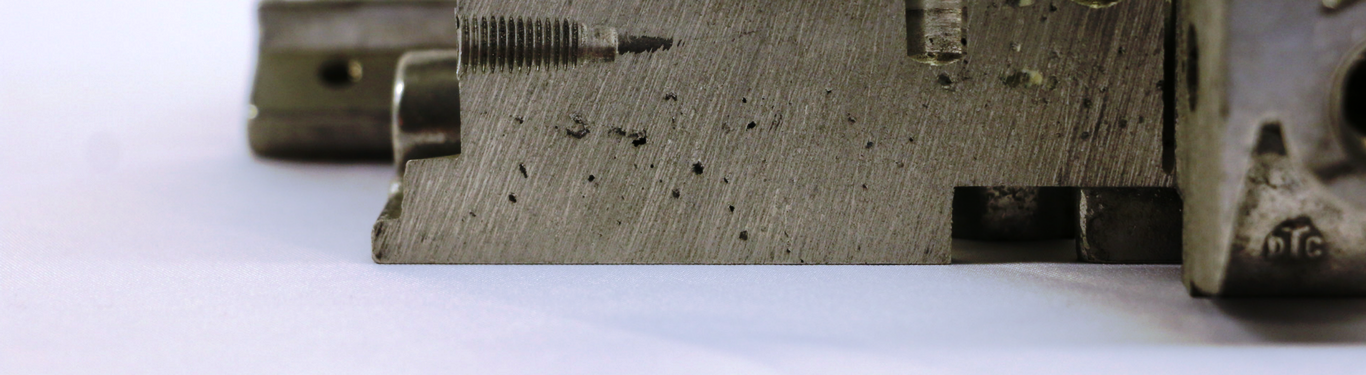
引け巣
概略
凝固時に、鋳物は鋳型内で収縮します。引け巣は、鋳物の一部が周囲よりも遅れて凝固し、その部分を完全に埋める十分な金属が流れ込まないために発生します。
形状
ギザギザ、または線状の形状をしています。一般的に、鋳物のコーピング部やドラッグ部、表面下に見られます。
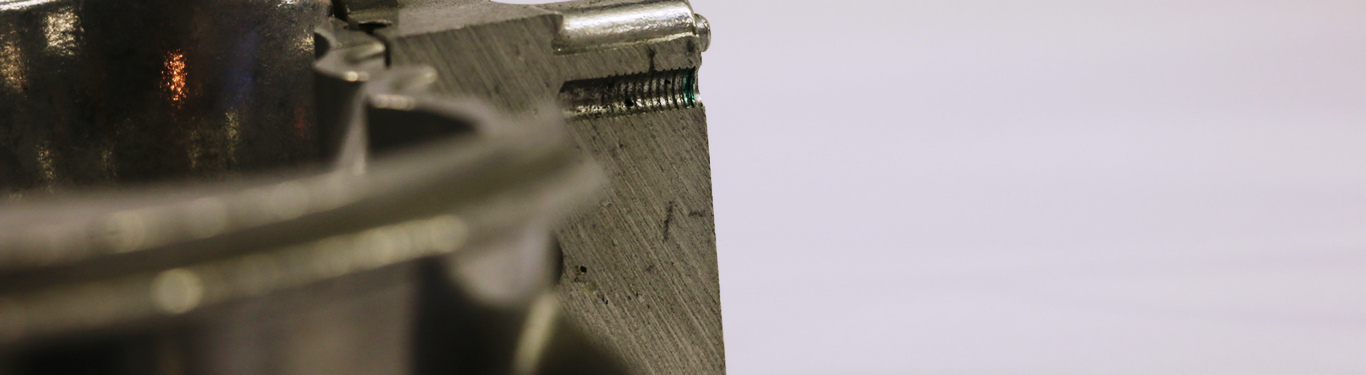
ポロシティ(穴孔)の問題
アルミニウムや鉄の鋳物の場合、ポロシティ(穴孔)の量が増加すると、相互に連結して漏れ経路を形成します。ポンプ、コンプレッサー、トランスミッション、配管設備などのアプリケーションにおいてポロシティ(穴孔)が存在すると、鋳物が圧力を持つため、鋳物を使用できなくなってしまいます。
鋳物のポロシティ(穴孔)の防止方法
最も経済的かつ成功する方法は、真空含浸法です。真空含浸法 は、ポロシティ(穴孔)が生じた鋳物にシールを行う方法です。真空および/または加圧方式で、鋳物の肉厚内にある隙間にシール剤を入れます。この方法は、コスト・パフォーマンスが高く、鋳物のポロシティ(穴孔)に対する恒久的なソリューションです。含浸を行う鋳物のサイズに制限はありません。含浸プロセスは部品内で行われるため、鋳物に歪み、変色などの影響は及ぼしません。
真空含浸法とは、何世紀にもわたって鋳造エンジニアたちが求めてきたソリューション「漏れがなく、耐圧性に優れた鋳物」です。すべてのアプリケーション要件に合致しており、さらに経済的でもあります。
金属製鋳物が最初に発見されて以来、安定した金属であるにも関わらず、スポンジのような内部構造を持つ鋳物のポロシティ(穴孔)は長年の課題でした。孔のある鋳物は、内部収縮、ガス・キャビテーション、酸化膜などの含有物/組み合わせによって、引き起こされてきました。あらゆる金属製鋳物や部品において見られる現象ですが、特にアルミニウム、亜鉛、青銅、鉄、マグネシウム、その他の合金から作られる鋳物で問題となることが多いのです。粉末金属または焼結金属製の部品には、その構造上、必ずポロシティ(穴孔)が存在します。
液体やガスを加圧式で充填する部品のポロシティ(穴孔)には、これまで数多くの方法で充填が試みられてきました。最初に含浸法として用いられた材質の一つは、「水ガラス」、つまりケイ酸ナトリウムでした。その後、ケイ酸ナトリウムの他にも、桐油、亜麻仁油、ピッチ・ガム など、他の材料が試されましたが、どれも上手くいきませんでした。第二次世界大戦直後、熱硬化性プラスチックの開発によって含浸法に使用されるようになり、特に真空加圧含浸法と併用することにより、金属製鋳物の肉厚内にあるポロシティ(穴孔)をシールする効率的かつ経済的な方法として注目されるようになりました。
真空含浸法の理解
金属製鋳物および粉末性金属製部品における真空含浸法は、ポロシティ(穴孔)を原因とする漏れ経路のシールのことを示します。含浸に使用されるシール剤は液状で、真空や圧力を使用して、肉厚内の隙間やポロシティ(穴孔)に注入されます。その後シール剤は硬化して、ポロシティ(穴孔)を埋めて部品の耐圧性を高めます。
粉末金属製部品に含浸法を施すことにより、加圧式アプリケーション用部品へのシールを行うことだけでなく、ポア(細孔)内のたまり部分メッキの巻き込みによる流出や斑点が削減されたことによって、メッキ加工や仕上げ加工の向上にもつながります。また、粉末冶金部品の加工では、ツールの寿命が延びるという利点もあります。
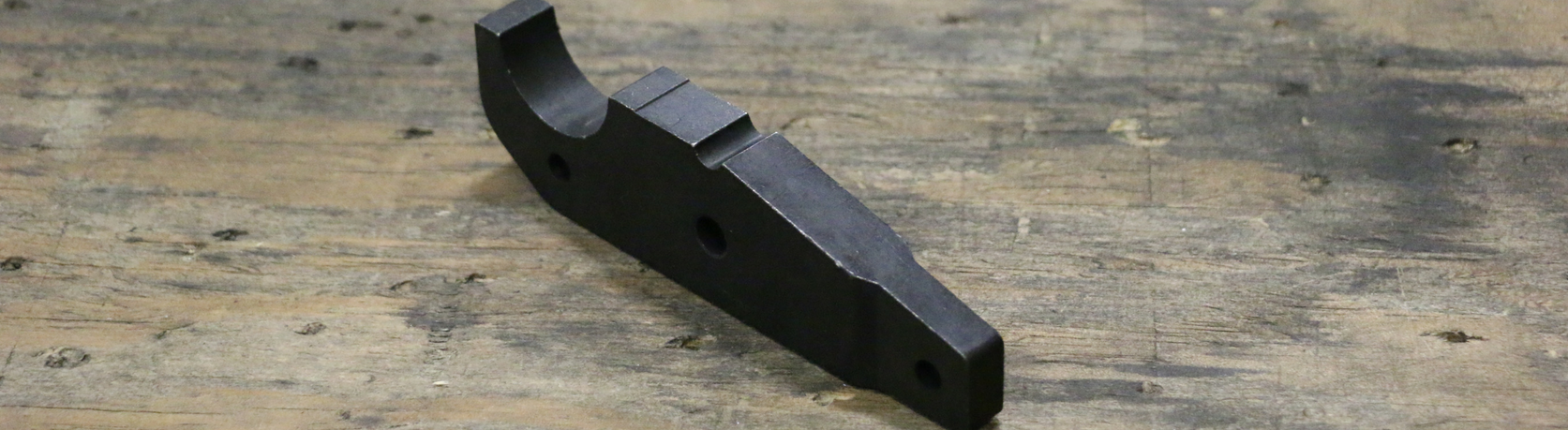
鋳物に盲孔性エリア、または連続的ポロシティ(穴孔)エリアがある場合、塗装やメッキ加工を行う前に含浸法を行うことで、最終表面仕上げの向上や、表面における流出や水ぶくれを防止することができるのです。
含浸テクノロジーは、ダイ・キャスト(圧力鋳造)、サンド・キャスティング、インベストメント(焼き流し)鋳造、圧力鋳造品、粉末金属製部品、鍛造製、溶接部などの、鉄および非鉄金属の漏れ経路をシールすることができる技術です。鉄、青銅、アルミニウム、亜鉛、マグネシウム、鋼、焼結金属などの金属に含浸処理を行うことができます。他の非金属製の物質(木、プラスティック、セラミック)も、含浸処理が可能です。
真空含浸法で、全体の部品品質が向上
鋳物のポロシティ(穴孔)によって漏れの問題が発生した場合、「不良品」はテストや検査によって識別されるのが一般的です。製造工程に送られる「良品」は、「不良品」と同様に多孔質であることが多いのですが、多孔質というのは分かりにくく、完全には相互接続していないことが特徴なのです。機械加工、機械的/熱的な衝撃、応力などによって、分かりにくい多孔質を連結させないように押しとどめていた薄い被膜が破壊され、「漏れの経路」となってしまうことがよくあるのです。含浸法では、孔を双方から充填するため、薄い皮膜が破れたとしても漏れを防止することができるのです。つまり、検査では漏れを選別するだけですが、含浸法は、品質の向上や改善も見込めるのです。
真空含浸法の経済性
機械加工、処理、アセンブリーなどの付加価値がある金属製部品は、その価値が100~1000米ドルに及ぶこともあります。しかし、ポロシティ(穴孔)や漏れによって金属製部品が廃棄された場合、この価値は消滅してしまうのです。含浸に必要な費用は、再溶解、再鋳造、再加工、部品の超過に関する費用に比べればほんの僅かなものです。含浸法によって、時間/費用/エネルギーが節減され、品質も保証され、また従来なら廃棄されていた部品も利用できるのです。廃棄量や再加工の削減により、継続的に生産性が向上するのです。また金属製部品に100%含浸法を行った結果、高額な漏れ検査を行う必要がなくなり、トランスミッション・ケース、エアコン、ポンプなどの金属製部品が現場で不合格となることが劇的に減少しました。
粉末金属製部品に含浸法を行うことで、ツールの寿命を最大100倍にも延ばすことができました。それはひとえにGW社のシール剤が潤滑剤の役目も果たし、かつそれぞれの粉末金属製部品のサポートも行ったからです。潤滑性があるということは、含浸法をまだ施していない粉末金属製部品の機械加工のプロセスにおいて、チャタリングの削減も出来るということです。
含浸法が効率的で経済的であると既に世間では証明されているため、圧力下で液体やガスを含んでいる全タイプの金属製部品を対象に、含浸法を適応するよう指定するケースが多くなってきました。現在、含浸プロセスは単なる回収作業ではなく、品質保証のために生産スケジュールに予め組み込まれるようになりました。
マクロ/マイクロ・ポロシティ(穴孔)
金属製部品内のポロシティ(穴孔)は、一般的に2つに分類されます。マクロ・ポロシティ(裸眼で目視可能な部品上にある大きなキズ)と、マイクロ・ポロシティ(肉眼では確認できないような微小の空洞)です。粉末金属製部品の場合、金属の構造上、低密度の鋳物ではマクロ・ポロシティ、高密度の鋳物ではマイクロ・ポロシティと分類されます。
ポロシティ(穴孔)には、「貫通型」「ブラインド型」「完全密閉型」があります。
貫通型ポロシティ(穴孔)(レッドで表示)は、金属製部品の肉厚を全に貫通しているので、漏れ経路となり得ます。
ブラインド型ポロシティ(穴孔)(ブルーで表示)は、部品の片壁のみに孔があります。
完全密閉型ポロシティ(穴孔)(グリーンで表示)は、部品の肉厚内で完全に分離された状態です。鋳物を機械加工すると、ブラインド型ポロシティ(穴孔)および完全密閉型ポロシティ(穴孔)も「貫通」してしまい、連結したポロシティ(穴孔)となって、漏れが発生してしまうのです。
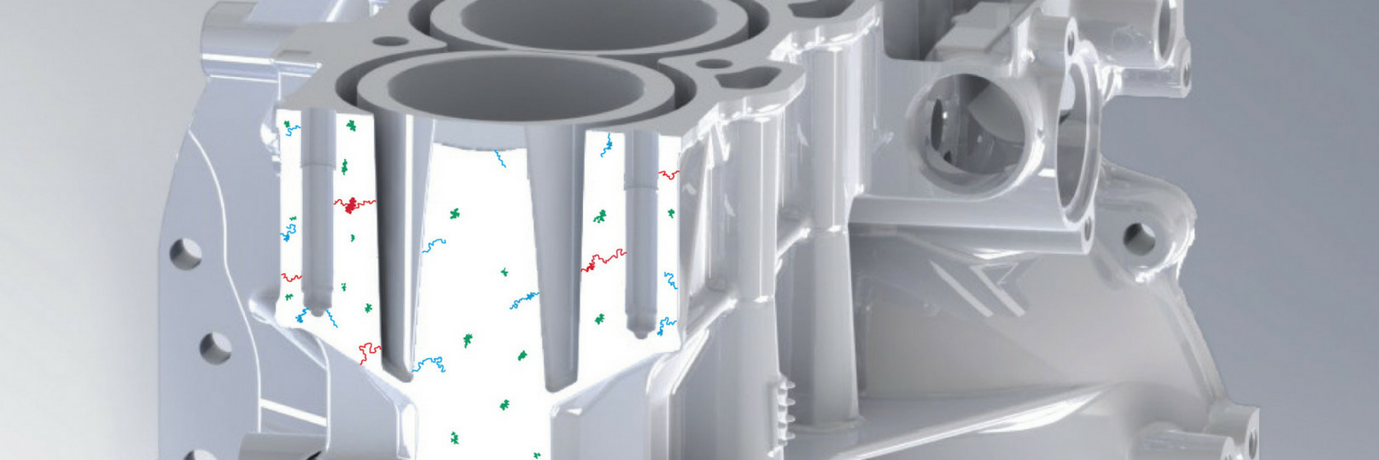
真空含浸プロセス
含浸法には一般的に3つの方法ードライ真空加圧法、ドライ真空法、ウェット真空法ーがあります。
最も一般的なプロセスは、ドライ真空加圧法です。ドライ真空加圧法の手順は以下のとおりです:
手順1:
ドライ含浸チャンバーに部品をセットして、設定値に到達するまで真空引きを行います。この真空度は、米軍の規定においては水銀29 インチ(23.4 Torrまたは31mbar)以上と定められています。容器内には、ポロシティ(穴孔)から空気を除去するのを妨げる液体は存在していません。すべの部品には一定の真空圧がかかります。これが「ドライ真空法」のプロセスです。
手順2:
真空の終点に到達すると、伝達用バルブが開状態になります。シール剤は脱気され、リザーバーから含浸容器に引き込まれます。その間、真空状態は維持されたままです。
手順3:
真空が解放されると、過圧をかけます(約70~90 PSI)。そしてシール剤がポロシティ(穴孔)を貫通するように圧力を保持します。伝達用バルブを再び開状態にし、シール剤を貯蔵槽に再び戻します。部品を取り除き、クリーニングおよび硬化を行います。
シール剤の要件
米国国防総省が制定した軍用規格MIL-276AおよびMIL-I-17563Cでは、含浸プロセスおよびシール剤に関する要件について記載されています。
MIL-276A は、ポロシティ(穴孔)がある金属製鋳物および粉末金属製部品に対する含浸法の軍用規格です。この規格では、アルミニウム、マグネシウム、銅、鉄(鋼以外)、亜鉛合金製の、構造的に健全な鋳物および粉末金属部品の含浸要件およびテストについて規定しています。
MIL-I-17563C は、鋳物および粉末金属部品の含浸プロセスに関する軍用規格です。この規格では、流体漏れの原因となる鋳造または粉末金属部品の隙間をシールするために行われる含浸法の要件について規定しています。
耐圧性に優れた鋳造品の製造に必要な基準に合致するための理想的なシール剤とは、ポロシティ(穴孔)を貫通して充填し、金属製部品のポロシティ(穴孔)内で完全に凝固できるものでなければなりません。シール剤の要件は、懸濁液内に不活性溶媒や濾過性固体物質を含まず、硬化時や不浸透性固体への変化時に気体や液体の副生成物を生じないイオン化された低粘度の液体であることです。この特性により、シール剤が毛細管現象によってごく微小な開口部や最も深い孔に浸透することができるのです。つまりこのシール剤は、水圧だけでは押し込むことのできない場所にまで毛細管現象を使って到達させることが出来るのです。また、安定性があり、寿命も長く、取り扱いや試験も容易で、作業環境における健康上/環境上の安全が確保できるようなシール剤でなければならないのです。