Category Archive: Sin categorizar
Conforme transcurre la vida útil de un equipo, el mantenimiento y la reparación (MRO) aumenta, mientras que la Eficiencia General del Equipo (OEE) disminuye. En este contexto, cuando las compañías estén trabajando en nuevos proyectos, deben de decidir entre una de las siguientes: “Utilizar el equipo viejo e invertir en MRO, aceptando un OEE más bajo” o “Invertir en un nuevo equipo utilizando la última tecnología, generando un OEE más alto.”
Si agregamos a los competidores la decisión se vuelve aún más confusa. En términos generales, la compañía que se niega a invertir en equipo, tecnología e infraestructura, puede perder su ventaja competitiva. Henry Ford lo dijo claramente cuando reflexionaba sobre la modernización de los equipos, con su famosa frase:
“Si necesitas una máquina nueva y no la compras, eventualmente te darás cuenta que pagaste por ella, pero sin tenerla.”
La realidad es que un negocio invierte dinero en los equipos, esperando adquirir una rentabilidad financiera. La inversión es necesaria para poder seguir compitiendo, y la compañía que no lo hace se verá superada por aquellas que sí lo hacen.
Rediseñando los Sistemas de Impregnación al Vacío
Los fabricantes que utilizan la impregnación al vacío se enfrentan constantemente con este dilema de invertir en equipos de impregnación al vacío. Al inicio de los años 2000, los sistemas de impregnación al vacío fueron modernizados para cumplir con las demandas de los nuevos entornos de fabricación. Los sistemas de lotes grandes, y de carga superior fueron reemplazados por los nuevos equipos que se diseñaron para carga frontal, procesando una sola pieza o una cantidad pequeña de piezas.
A medida que los estándares de manufactura cambian, el OEE de los equipos tradicionales de impregnación ha disminuido, y ya no es suficiente para alcanzar los estándares de producción y calidad del presente. Aquellos que integraron un equipo moderno de impregnación a su cadena de producción se mantienen competitivos con un OEE mas alto por las siguientes razones:
Costo
La impregnación dentro de la misma planta se puede hacer por tan solo una parte del precio si se compara con un servicio externo a la compañía. Los equipos modernos utilizan el mínimo de mano de obra, son pequeños y compactos, y son ahorradores de sellador y de otras utilidades.
Logística
Al operar un equipo de impregnación dentro de la misma planta, la compañía puede eliminar el trabajo en proceso (WIP, por sus siglas en inglés) y costos de transportación. Adicional a esto, la compañía tendrá mejor control de los lotes y rastreabilidad de las piezas. La rastreabilidad de los lotes es fundamental para producir piezas eficientemente. El tener control y rastreabilidad de los lotes significa ahorro de dinero a largo plazo, protegiendo a la compañía de llamados a revisión e inventario perdido, y ayudándole a cumplir con los estándares y regulaciones.

Integración
Tanto el tamaño como el diseño modular de los sistemas modernos de impregnación al vacío, permiten que los fabricantes puedan ubicar las unidades inmediatamente dentro del maquinado, pruebas de fugas o áreas de ensamble, ubicando la solución justo donde se necesite.
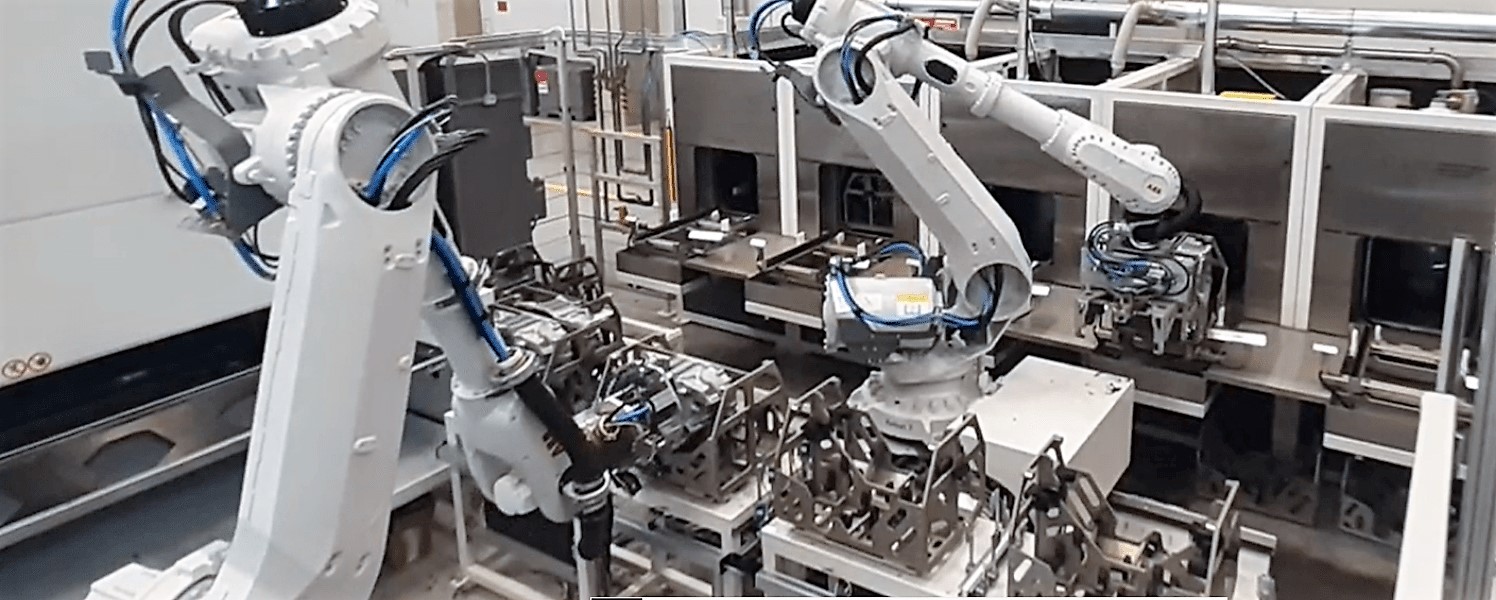
Control de Calidad
El equipo para impregnación dentro de planta utiliza un manejo robótico, y tiene ergonomía para que el operador pueda mover las piezas entre los módulos. Este proceso repetitivo aumenta la tasa de recuperación, y elimina el daño por manejo y la contaminación del proceso.
Adicional a esto, la mayoría de los sistemas tienen controles PLC. Esto significa que la adquisición de los datos, proceso esencial en el entorno de fabricación de hoy en día, pueden integrarse al proceso para fortalecer la calidad en el sistema de producción. Los datos individuales de los parámetros clave se pueden recolectar y almacenaren números de serie individuales. En caso de que surgieran dudas, el sistema de auditorías puede proporcionar datos importantes sobre cada pieza que se ha impregnado.
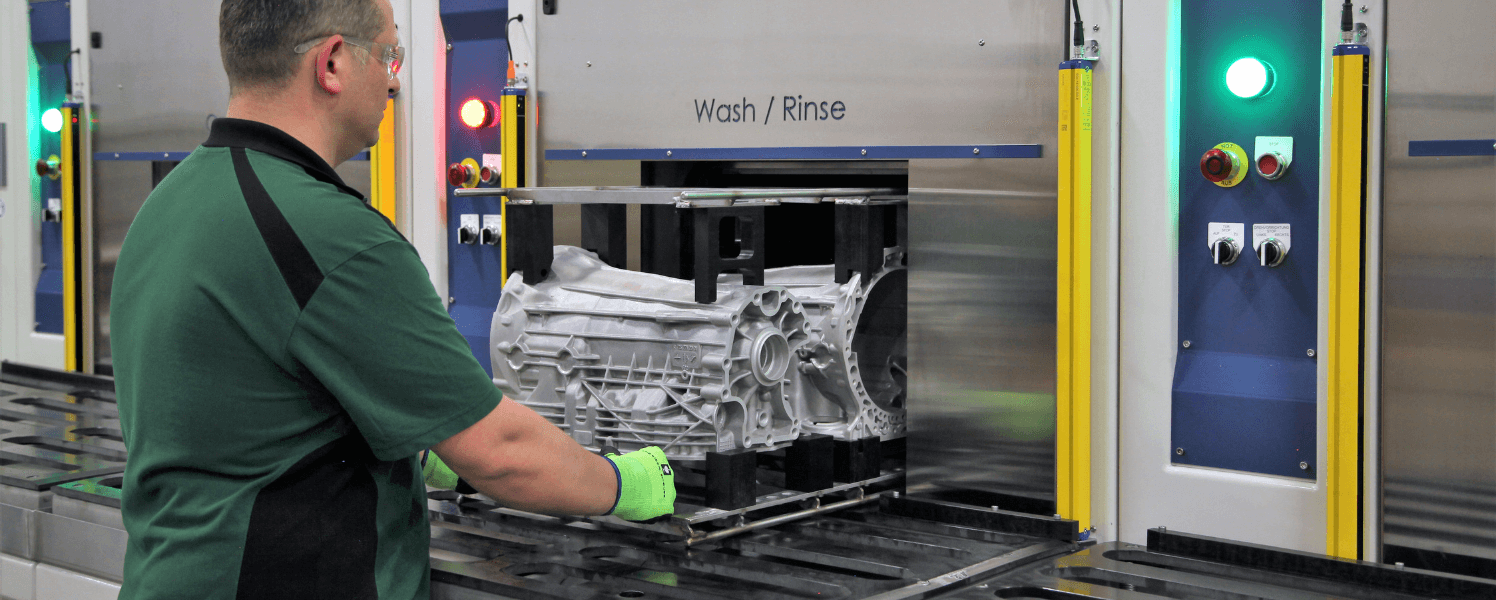
Conclusión
Conforme va avanzando la tecnología, la frase de Henry Ford sobre la inversión en los equipos se ha mantenido a través del tiempo. La inversión en equipos es necesario para que la compañía pueda cumplir con los requerimientos de rendimiento y demandas de calidad tan cambiantes. Al integrar sistemas modernos de impregnación al vacío dentro de su planta, las compañías permanecerán competitivas operando con el OEE más alto posible.
Los componentes electrónicos juegan un papel crucial en los vehículos electrícos (EVs). En el año 2000 los componentes electrónicos representaban 18% del costo total del automóvil eléctrico. Veinte años después, este porcentaje ha aumentado a un 40% del costo total. El uso de componentes electrónicos seguirá cumpliendo con los estándares de eficiencia de consumo de combustible, regulaciones de seguridad y de consumidor. Sin embargo, mientras que el uso de los componentes electrónicos siga creciendo, los fabricantes deben asegurar la calidad, seguridad e integridad de rentabilidad de sus piezas.
(más…)
Uno de los componentes que están diseñando los ingenieros para los vehículos eléctricos (EVs) es el motor eléctrico. Este componente es uno de los impulsores principales detrás de los EVs. Según datos de IDTEchEx, se van a adquirir más de 100 millones de motores eléctricos para el 2032. El mercado de EVs está evolucionando constantemente con requerimientos de nuevos diseños y de rendimientos más altos que cumplan con las demandas de los consumidores. Estos requerimientos ocasionan que aumente la cantidad de piezas que se rechazan y desechan, generando un aumento en los costos y atrasos en la producción.
En un motor eléctrico, el cableado de cobre aislado está enrollado en una base para crear o recibir energía electromagnética, transfiriendo esa energía hacia otra bobina por medio de inducción. Una vez que el motor eléctrico se enrolla, debe ser aislado con un barniz (Imagen 1). Este paso es crítico para asegurar la integridad de la pieza. La Impregnación al Vacío y Presión (VPI) y el Baño de Barniz son los dos métodos más comunes para aislar motores eléctricos.
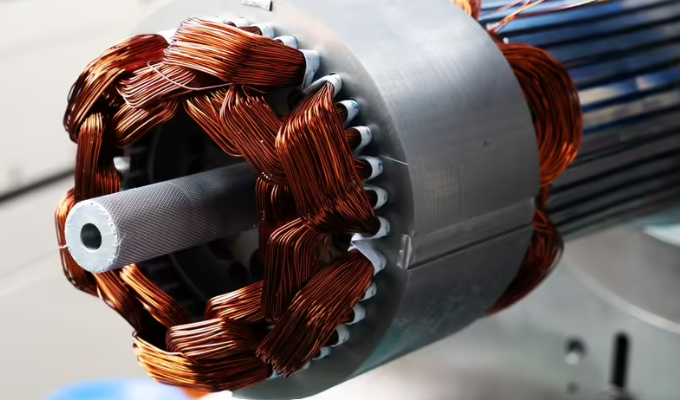
Imagen 1: El cableado de cobre debe ser aislado para asegurar el rendimiento del motor.
Proceso de Impregnación al Vacío y Presión
Durante el proceso de VPI, la pieza se sumerge dentro del tanque de presión y se aplica vacío. Mientras ocurre eso, se inyecta un barniz dentro de la cavidad hasta que la unidad está completamente sumergida (Imagen 2). Se aplica presión, y el interior y exterior de la pieza se impregna completamente con el barniz. Después, la pieza se extrae y es curada en un horno.
El aire es un elemento crítico que ocasionará problemas de calidad y de rendimiento. Por lo tanto, el proceso del vacío es crucial para eliminar el aire. Esto asegura la penetración efectiva del barniz.
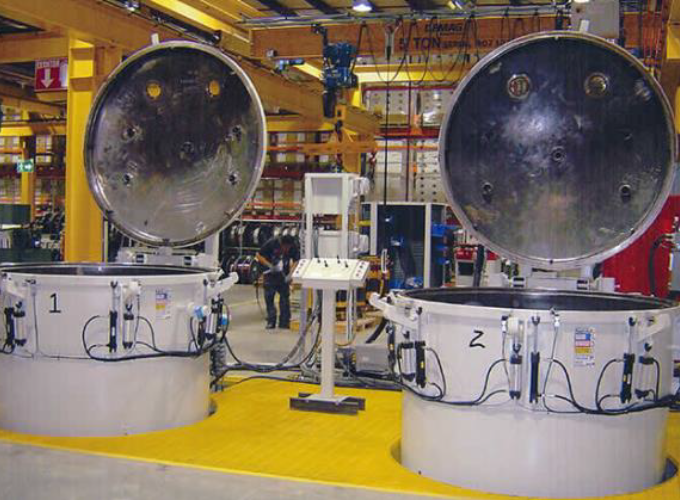
Imagen 2: La pieza se sumerge dentro del tanque de presión y después se aplica vacío.
La eliminación del aire es crítica para asegurar que el barniz penetre completamente.
El proceso de Baño de Barniz sumerge la pieza dentro del tanque de barniz. Después, la pieza se cura en un horno. El proceso de Baño de Barniz no cuenta con la aplicación de vacío. Esto significa que el aire no es completamente eliminado, y que la pieza no queda completamente impregnada por dentro y por fuera.
Beneficios de la Impregnación al Vacío y Presión
Si bien ambos procesos se han utilizado por más de 60 años, el proceso de VPI tiene tres ventajas significativas sobre el Baño de Barniz (Imagen 3).
Aumenta la entrega de potencia
Gracias a la aplicación de vacío, el barniz del proceso VPI tiene una penetración completa. Una pieza completamente aislada promueve una mejor transferencia de calor, manteniendo la electricidad dentro del cableado. Esto genera un mejor rendimiento en el motor.
Resistencia a la contaminación
La contaminación se penetra en los pequeños orificios del aislamiento no sellado y produce un patrón de conducción entre vueltas de cable o contra la tierra. Tal como se mencionó anteriormente, el proceso VPI aísla completamente la pieza gracias al proceso del vacío. Por lo tanto, el proceso VPI elimina cualquier riesgo de contaminación. El aire que no se elimina de la pieza crea orificios microscópicos que aumentan el riesgo de contaminarse.
Reduce vibración en la bobina
La falla más común en los motores es la abrasión. La vibración causa desgaste y fricción, haciendo que la pieza deje de soportar el voltaje. El tener una pieza completamente aislada por medio del proceso VPI, sirve como un adhesivo entre las hebras del motor mientras éste gira. Esto reduce el riesgo de vibración en las bobinas.
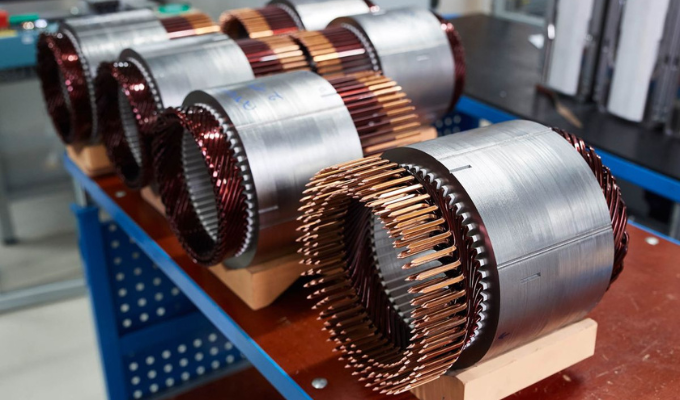
Imagen 3: El proceso VPI asegurará la salida de potencia de las piezas,
mejorará la resistencia a la contaminación y reducirá vibración en las bobinas.
Fuente de la imagen: Coche y conducir
En Resumen
Los motores eléctricos en EVs ofrecen tecnología y rendimiento de punta. Mientras los motores eléctricos continúen en auge, también la necesidad del proceso VPI. La Impregnación al Vacío y Presión es la manera más eficiente y efectiva de aislar motores. El proceso VPI asegura el rendimiento de las piezas y elimina modos de falla.
A medida que las demandas cambian, es imprescindible que las compañías se vuelvan respetuosas con el medio ambiente. Debido a esto, los fabricantes de equipos originales que utilizan castings de fundición de aluminio se han adaptado rápidamente, y las prácticas de fabricación sustentables se han vuelto cada vez más comunes.
La fabricación sustentable pretende minimizar los desperdicios de producción y el impacto ambiental. Esto se logra diseñando productos y adoptando procesos de manufactura que son más ambientalmente amigables. La fabricación sustentable se extiende desde el fabricante de equipos originales a través de proveedores tanto en procesos y materiales. Esto también incluye procesos como impregnación al vacío y materiales como selladores (Imagen 1).
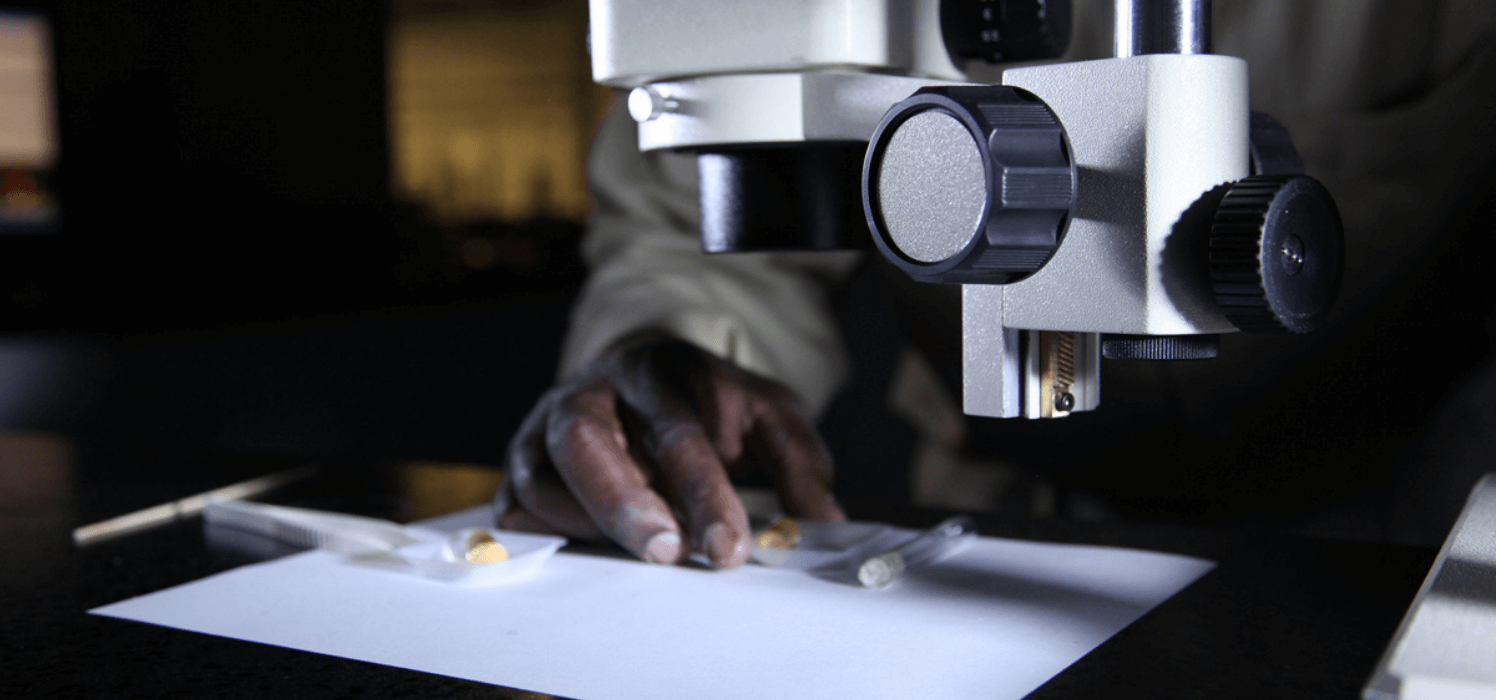
Imagen 1: La fabricación sustentable se logra diseñando productos y procesos que son respetuosos con el medio ambiente.
Qué es Impregnación al Vacío
Vacuum impregnation al vacío es un método de bajo impacto para sellar vías de fuga que se forman durante el proceso de fundición. Específicamente, la impregnación al vacío sella cualquier vía interna e interconectada de porosidad que penetró la pared del casting y puede resultar en la falla del producto. La técnica sella la porosidad con un sellador sin necesidad de cambiar las características dimensionales o funcionales del casting.
Al sellar la porosidad en castings, la impregnación al vacío permite que los fabricantes las piezas en lugar de desecharlas y enviarlas a scrap. Como resultado, el proceso permite que los fabricantes reduzcan radicalmente sus desperdicios y controlen sus recursos ya que se regresa casi el 100% de las piezas a la línea de producción.

Imagen 2: Al sellar la porosidad en castings de fundición de aluminio, la impregnación al vacío permite que los fabricantes utilicen las piezas que iban a desechar o enviar a scrap.
Beneficios de Selladores Recuperables
No solamente el proceso de impregnación al vacío contribuye a la sustentabilidad ambiental, también algunos materiales disponibles para usar en el proceso, por ejemplo, el sellador recuperable. A continuación, se nombran los beneficios principales de los selladores recuperables más comúnmente usados.
- Recupera– Los selladores recuperables son recuperados automáticamente antes de lavado y retornados al módulo de impregnación para reutilizar inmediatamente. El sellador recuperado ayuda a eliminar el riesgo de contaminación de sellador.
- Reutilizar– Los selladores recuperables permanecen en su estado original durante el proceso de impregnación. A diferencia de otros selladores, no tienen que pasar por un proceso costoso para ser reconstituidos. Por lo tanto, pueden ser utilizados múltiples veces sin tener que pasar por procesos adicionales para quitar agua de lavado y otros contaminantes.
- Reducir– El consumo de sellador se reduce a través del manejo de piezas eficiente y la pureza del sellador. Esto ayuda a asegurar que la pieza sea debidamente sellada sin quedar pegajosa o por contaminación de grumos, así sea el primer o el quincuagésimo ciclo. Debido a que el sellador recuperable es expulsado antes de la estación de lavado este no se emulsiona con el agua de lavado. Las piezas se limpian en agua limpia y no retienen sellador residual (Imagen 3).
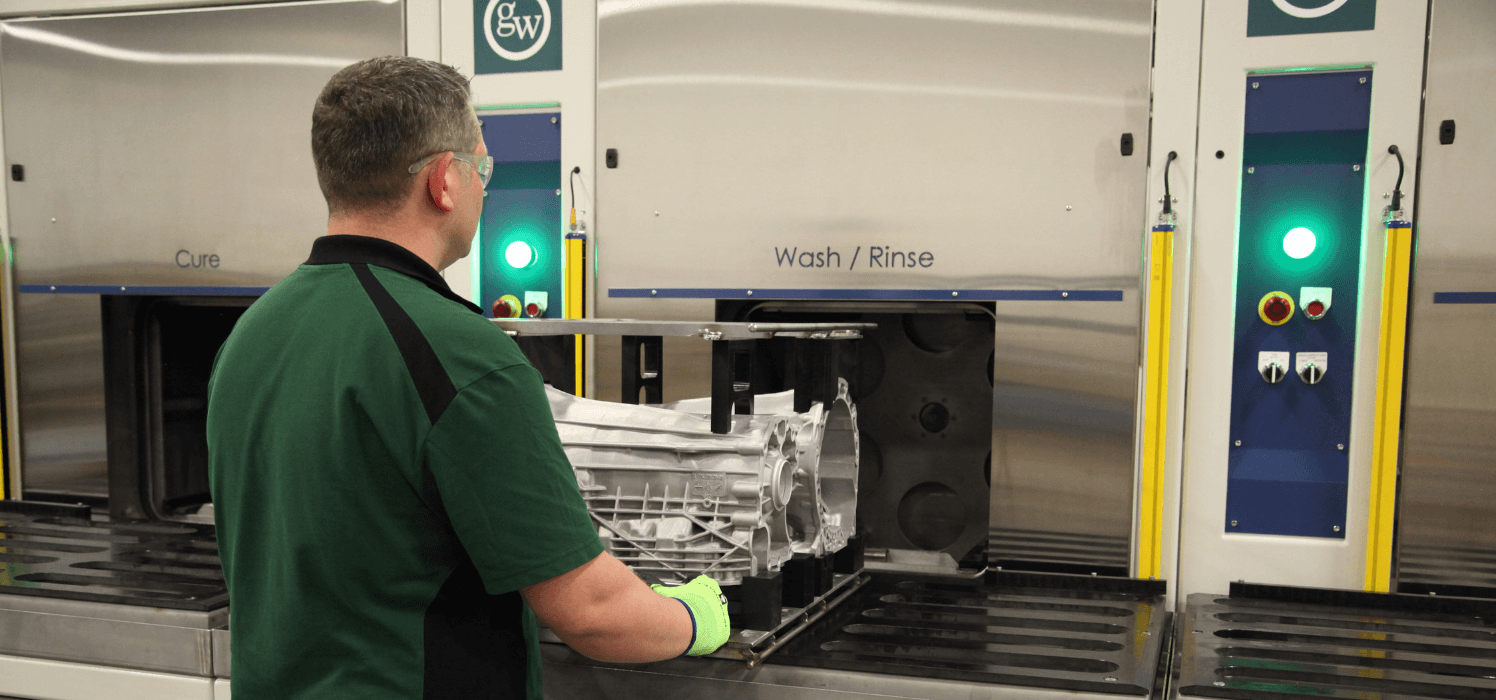
Imagen 3: El sellador recuperable no se emulsiona con el agua de lavado debido a que se expulsa desde antes de entrar a la estación de lavado.5\
Conclusión
Los selladores recuperables ofrecen una ventaja significativa a los fabricantes en el sellado de porosidad en castings de aluminio. Los selladores son realmente ecológicos y conservan el medio ambiente. Maximizan la recuperación de castings mientras aseguran la seguridad del operador y el medio ambiente.
Los fabricantes se encuentran constantemente en el dilema entre desechar un casting que fuga, o sellarlo por medio de impregnación al vacío. Algunos perciben la impregnación al vacío como un costo que no agrega valor y asumen que es menos costoso desechar los castings que fugan. En un ejemplo simple y real, estaremos revisando el costo de scrap de castings de fundición de aluminio contra la impregnación al vacío.
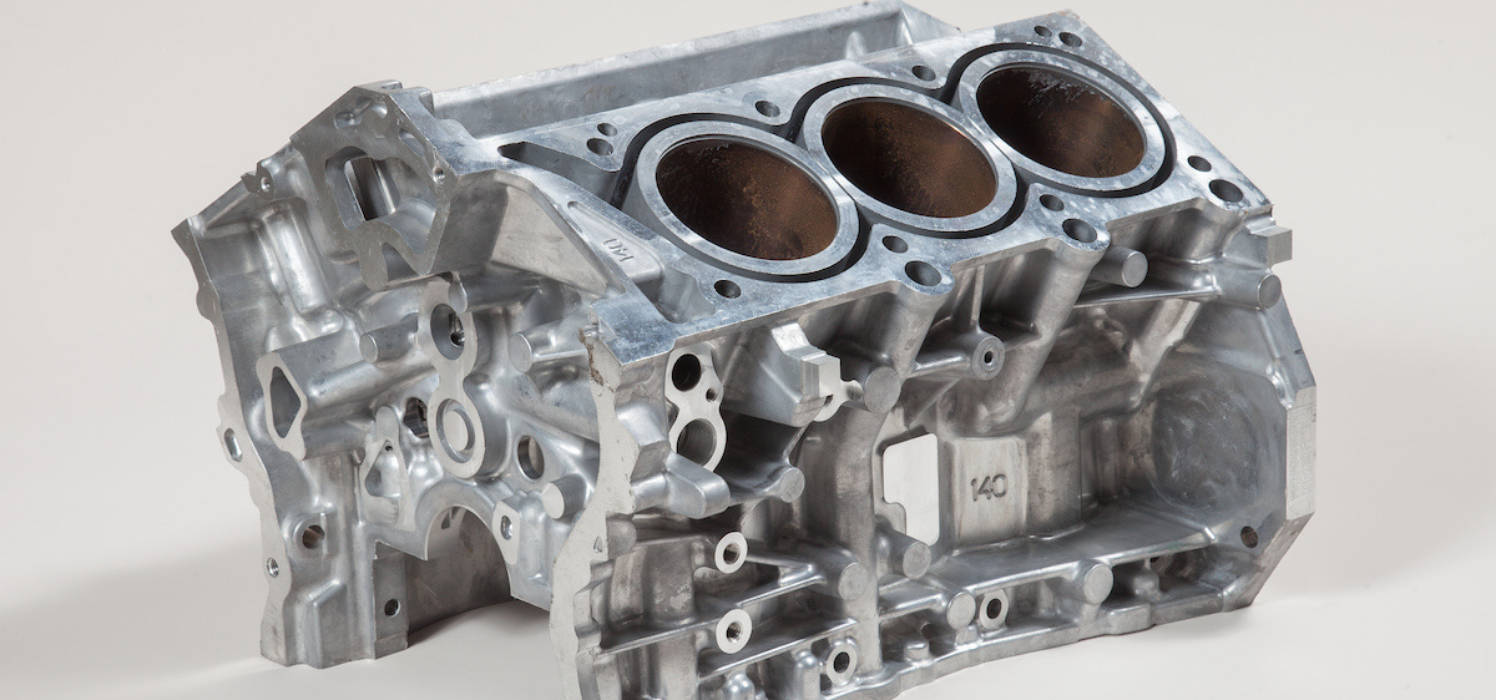
Imagen 1: Si este bloque de motor tiene fugas ocasionadas por porosidad, el fabricante tiene la opción de mandar la pieza a scrap, o sellarla con impregnación al vacío.
Supongamos que un fabricante automotriz requiere 1,000 bloques maquinados por día. La pieza se vende por $150. De esos 1,000, 3% no pasa la prueba de fugas y requiere impregnación. Suponiendo que las piezas se fabrican durante un turno de lunes a viernes, es igual a 240 días por año.
Costo de Scrap en Castings:
Si los 30 castings se mandaran a scrap, el costo sería el siguiente:
- 30 * $150 = $4,500 por día
- $4,500 por día * 240 días = $1,080,000 por año en scrap
Costo de Impregnación al Vacío:
Al utilizar un equipo moderno de impregnación al vacío, se logra una tasa de recuperación de más del 96%, lo cual significa que 29 de 30 piezas serán selladas. Históricamente, el costo promedio por embarcar e impregnar 30 piezas por día es el siguiente:
- $384 por día
- $384 * 240=$92,160 por año
Retorno de Inversión:
- Si se sellaran 29 de 30 piezas cada día, la compañía recuperará $4,350 por día (29 * $150)/
- Considerando un costo anual de $92,160 en impregnación al vacío, la compañía tendría un retorno de su inversión en 22 días ($4,350/$92,160)
- Para el final del año, la compañía habrá tenido un retorno del 1,172% ($92,160/$1,080,000).
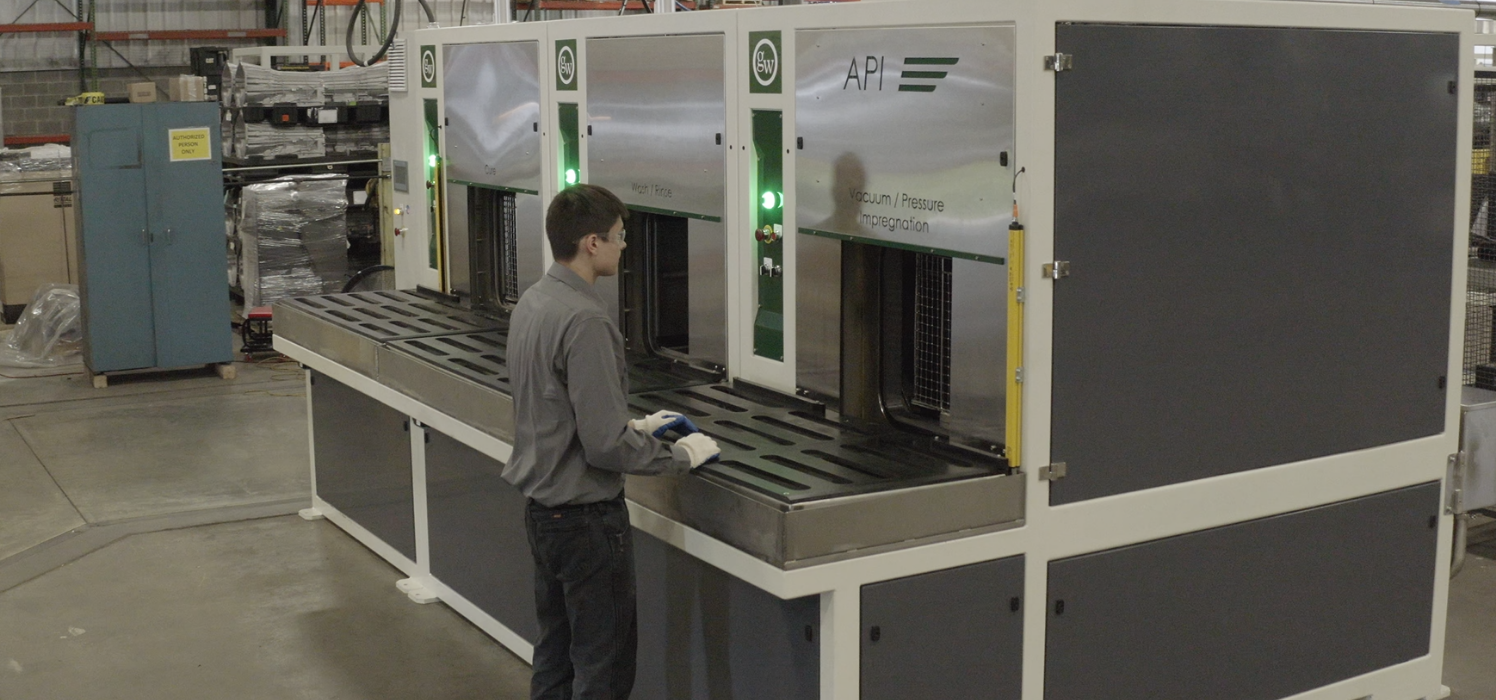
Imagen 2: La impregnación al vacío sella la porosidad en castings y permite que los fabricantes utilicen piezas que iban a desechar.Este es el proceso preferido y el método más fácil para sellar porosidad.
Conclusión:
Después de ver que el retorno de inversión es significativamente alto, es evidente por qué los clientes prefieren recuperar castings. El cliente gastará $92,160, para ahorrarse $1,080,000 al año. La impregnación al vacío es el método más rentable para sellar porosidad. Este ejemplo resalta cómo la impregnación al vacío es un costo que agrega valor y mejora la calidad del producto. La impregnación al vacío asegura la calidad del producto mientras mejora la rentabilidad.
El uso de electrónicos en los automóviles los ha hecho más rápidos, seguros y confiables. Los electrónicos se han vuelto tan comunes que son prácticamente un commodity lo mismo que el aluminio y el acero. Como esta tendencia va subiendo, los fabricantes necesitan soluciones enfocadas a las vías de fuga que se pueden generar naturalmente cuando estos componentes se fabrican.
Una vía de fuga es un hueco entre los materiales de un componente eléctrico. Estos huecos o vacíos pueden presentarse durante la fabricación, cuando se contraen los materiales a diferentes velocidades debido a sus propiedades físicas. Estos huecos podrían ser invisibles, pero desastrosos (Imagen 1). Se podrían filtrar agentes húmedos o corrosivos en la vía de fuga, ocasionando que la pieza sea ineficaz, resultado en una falla en campo.
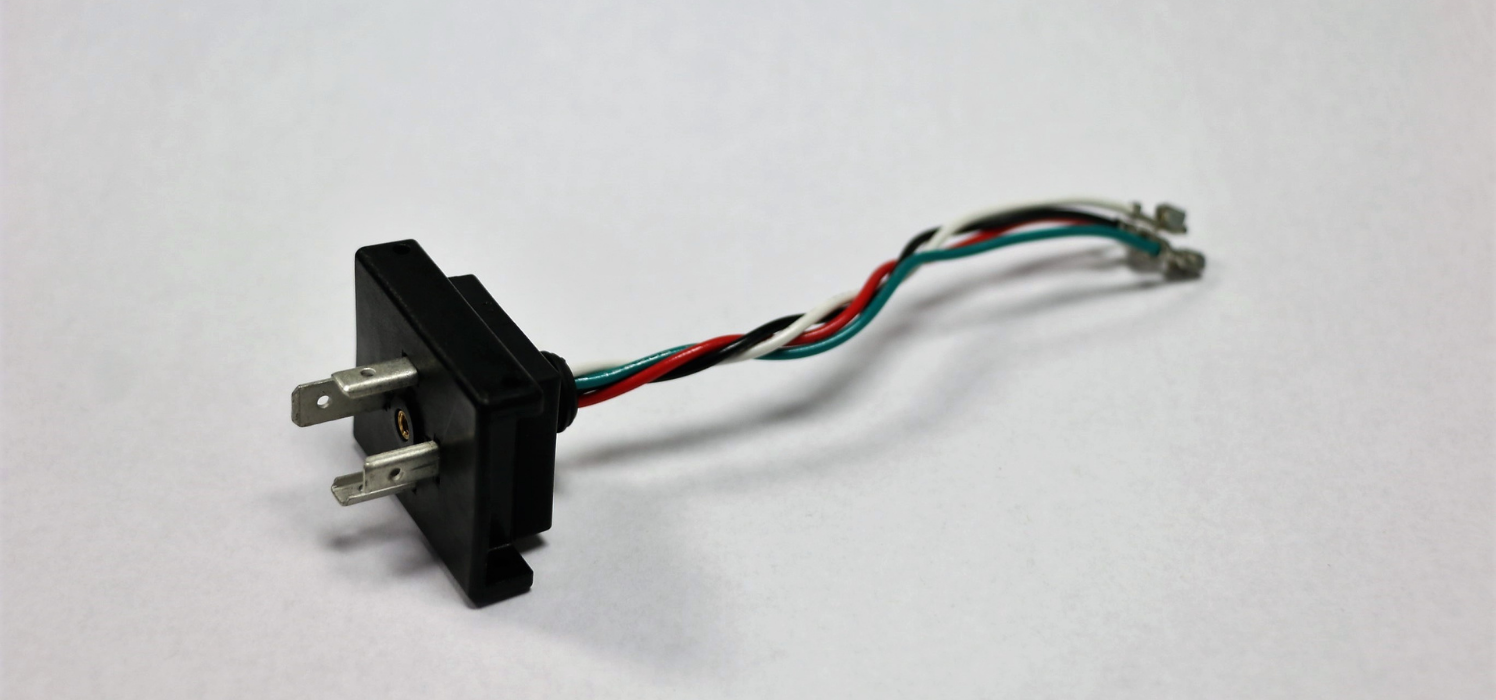
Imagen 1: Los materiales en los electrónicos se contraen a diferentes velocidades ocasionando porosidad.
Los agentes húmedos o corrosivos pueden penetrar la porosidad, ocasionando que la pieza sea ineficaz.
El empastado y la impregnación al vacío son los dos métodos más populares para solucionar vías de fuga en componentes electrónicos. En el empastado se llena una parte con plástico termoestable o caucho de silicona. El proceso de impregnación al vacío sella los huecos internos con un sellador. La impregnación al vacío se utilizó por primera vez hace 70 años para sellar porosidad en castings de fundición de aluminio. El proceso se sigue usando a la fecha para la porosidad en castings de fundición, pero en las últimas décadas tecnología de impregnación al vacío ha surgido también para el sellado de electrónicos.
Utilizar impregnación al vacío en lugar de empastado para sellar electrónicos tiene 4 principales beneficios:
1. La impregnación al vacío sella la vía de fuga—La impregnación al vacío sella la vía interna de fuga, mientras que el empastado solamente las rellena en la superficie de la interface. La impregnación al vacío habilita la presión y evita que los fluidos se filtren dentro de la pieza (Imagen 2).
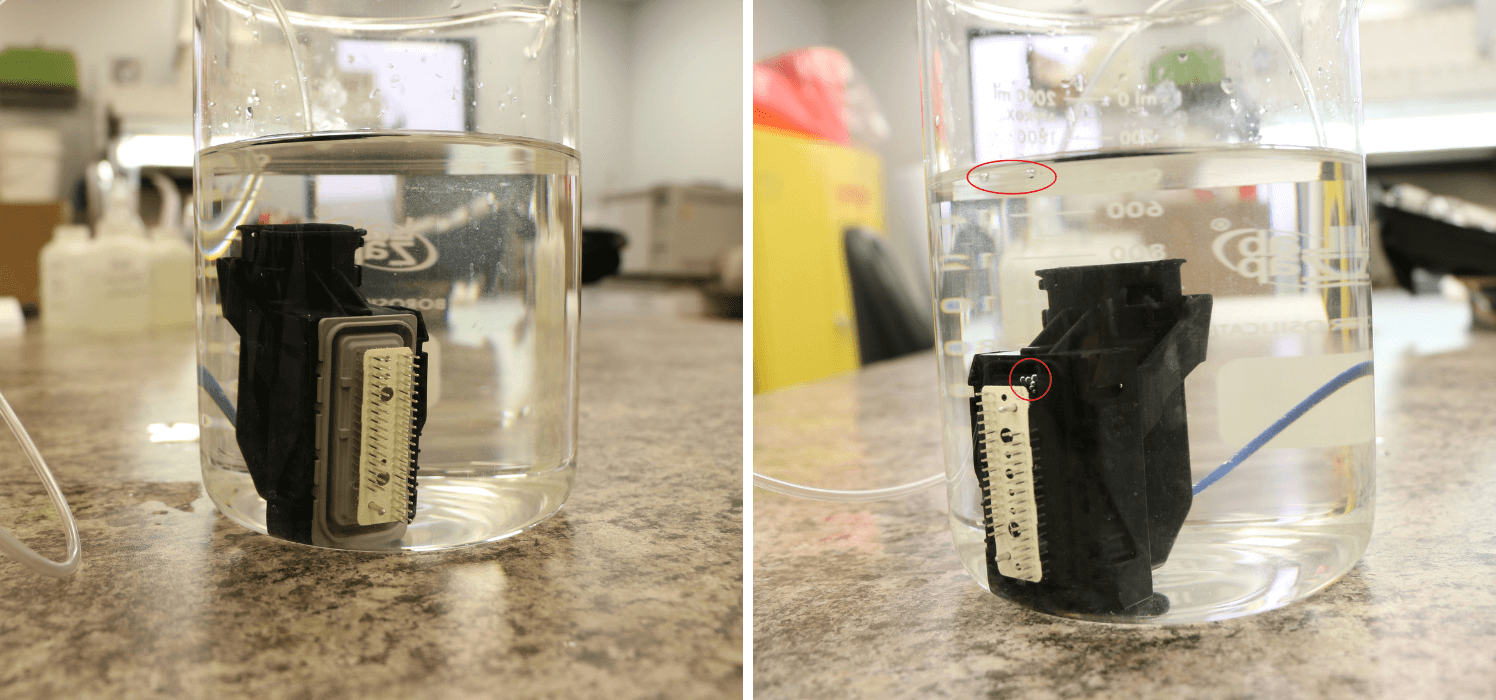
Imagen 2: La imagen en el lado izquierdo es un sellado a través de impregnación al vacío. En la pieza no aparecen burbujas al sumergirla al agua, lo que nos dice que quedó sellada. La pieza del lado derecho no queda sellada ya que sí aparecen burbujas (resaltadas en rojo).
2. La impregnación al vacío permite mayor libertad en el diseño—Las dimensiones de una pieza se mantienen en la impregnación al vacío, permitiendo que los ingenieros tengan la libertad de diseñar las piezas en sus tamaños netos. Además, desde que el proceso de impregnación al vacío se realiza en la bajo la superficie, un ingeniero no tiene necesidad de incorporar tolerancia dimensional.
3. La impregnación al vacío es menos costosa—El costo del equipo de impregnación al vacío es menor al del equipo del empastado, lo cual reduce el tiempo de recuperación de capital.
4. La impregnación al vacío brinda mayor rendimiento—La impregnación al vacío les da a las compañías el beneficio de las economías de escala. Las características y tiempos del proceso permiten que los electrónicos sean sellados efectivamente y económicamente (Imagen 3).
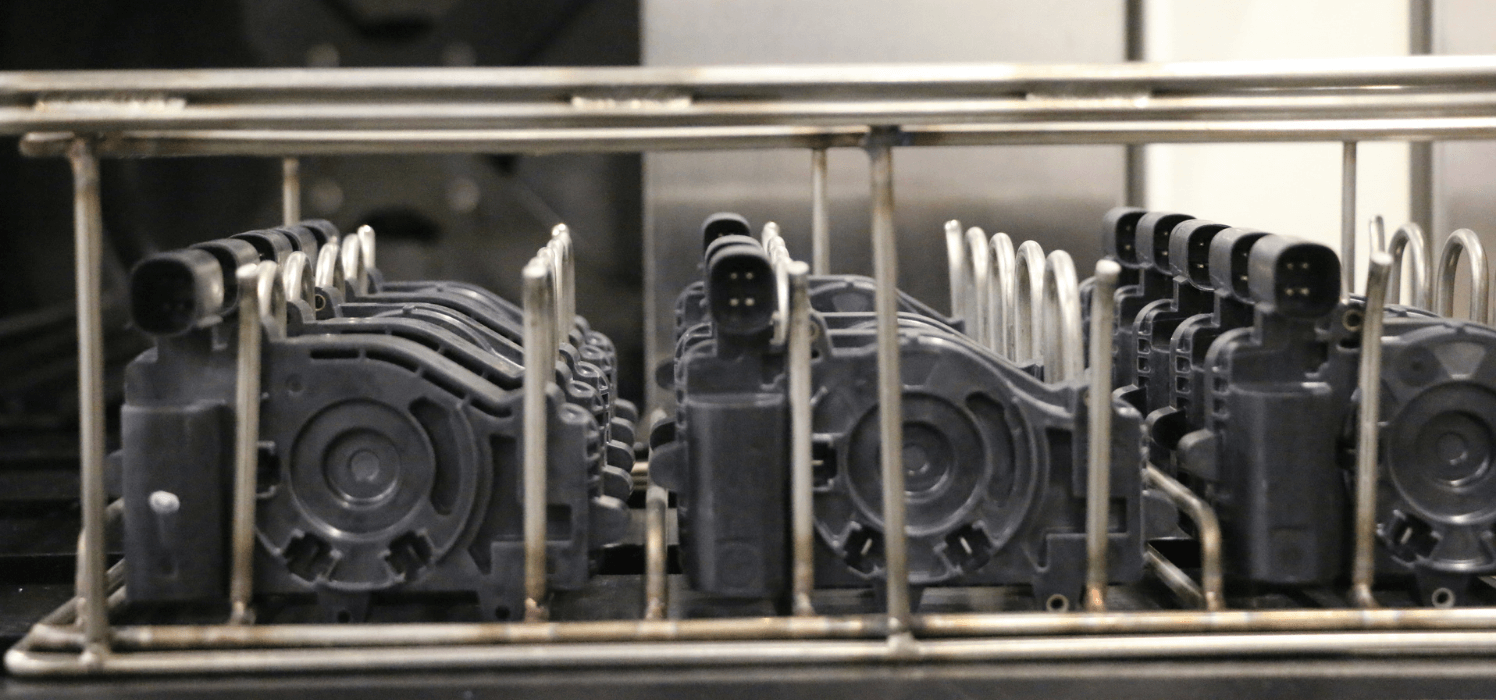
Imagen 3: Las características permiten que se pueda sellar una grande cantidad de piezas al mismo tiempo. Esto permite que las compañías tengan el beneficio de las economías de escala.
En Resumen
Conforme siga creciendo la demanda de los componentes electrónicos en los automóviles, también crecerán los requerimientos de rendimiento y de tasas de fuga de las piezas. La fiabilidad y repetitividad de la impregnación al vacío lo hacen la mejor solución para cumplir con estos requerimientos. Adicionalmente, la impregnación al vacío asegura la calidad de los componentes eléctricos, mientras también mejora la rentabilidad.