Fallstudie: Auswahl des richtigen Imprägnierprograms
Im Jahr 2008 beschloss ein nordamerikanischer Motorradhersteller, seinen Imprägnierbedarf im eigenen Hause zu decken, um die Herstellungskosten zu senken. Der OEM berücksichtigte mehrere Imprägniermittel- und Anlagentechnologien. Dem Unternehmen wurde eine Imprägnieranlage verkauft, mit der Behauptung den Abwasseranfall zu eliminieren, besser Abdichtraten zu erzielen und minimale Wartungs- und Reparaturkosten zu haben. Die ausgewählte Imprägnieranlage basierte auf einem Recycling-Imprägniermittel.
Die Herausforderung
Im Laufe der Zeit stellte der Hersteller fest, dass sich das, was verkauft wurde, von der Realität unterschied. Sie fanden heraus, dass sich die Chemie des recycelbaren Imprägniermittels im Laufe der Zeit verändert hat, ebenso wie die erzielten Abdichtraten. Während des Imprägnierprozesses wird das Imprägniermittel mit Wasser vermischt. Während das Imprägniermittel zunächst rein war, verlor es durch den Kontakt mit Wasser seine Eigenschaften und kehrte nie zu seiner ursprünglichen Formulierung zurück.
Außerdem war eine zusätzliche WaschWasserChemie erforderlich, um die Funktion des Imprägniermittels aufrechtzuerhalten. Diese zusätzliche Chemie musste jedoch täglich und in einem genauen Verhältnis zugesetzt werden.. Wenn das Verhältnis nicht korrekt war, wurde das Imprägniermittel instabil. Der Hersteller stellte fest, dass überschüssige Chemikalien, die in die Wasch- und Härtungsmodule verschleppt wurden, die Kontamination der Teile erhöhten und das Anlagensystem beschädigten (Bild 1).
Bild 1: überschüssiges Imprägniermittel, welches in die Wasch- und Aushärtestation gelangt, bedingt Bauteilkontamination
Das Imprägniersystem erwies sich als bemerkenswert teuer. Der Hersteller verbuchte Ausgaben in Höhe von über 1.000.000 USD aufgrund von Ausschuß, Reparaturen, Wartung, Arbeitsaufwand, Verbrauchsmaterialien für Imprägniermittel und weiterer benötigter Chemie. Die Kosten für die Verwaltung des Systems überstiegen die Kosten für die Auslagerung des Imprägnierungsprozesses.
Die Erkenntnis bestand darin, dass sich die Strategie der Vakuumimprägnierung ändern musste, und sie hatten die Gelegenheit, dies zu Beginn eines neuen Kurbelgehäuse-Programms zu tun. Das Unternehmen entwarf ein neues, leichteres Kurbelgehäuse, bei dem 100% der Teile abgedichtet werden mussten. Basierend auf früheren Erfahrungen und Daten stellte das Unternehmen fest, dass bei der Auswahl eines neuen Imprägniersystems drei Hauptherausforderungen zu bewältigen sind.
- Wartungskosten – Die alte Imprägnieranlage hatte einen hohen Bedarf an Ersatzteilen. Der Hersteller benötigte ein einfacher zu betreibendes System mit weniger Wartungs/Reparaturaufwand.
- Imprägniermittelmanagement – Das Recycligharz musste übermäßig getestet und gewartet werden. Der Hersteller benötigte ein Imprägniermittel, das seine ursprüngliche Formulierung beibehielt und keine tägliche Wartung durch mehrere Abteilungen erfordert.
- Schlechte Abdichtrate – Das alte Imprägniersystem produzierte einen Teileausschuß von ca. 14%. Alle nicht abgedichteten Werkstücke wurden verschrottet. Die Kosten für die verschrotteten Gussteile beliefen sich auf ungefähr 967.000 USD. Der OEM musste mehr Gussteile zurückgewinnen.
Die Lösung
Godfrey & Wing empfahl sein CFi-System (Continuous Flow Impregnation) das DVP-Verfahren (Dry Vacuum & Pressure) und das rückgewinnbares Dichtmittel 95-1000AA.
Das CFi-System basiert auf dem DVP-Imprägnierungsverfahren (Dry Vacuum and Pressure), von Godfrey & Wing, welches ein schnelles, tiefes Vakuum nutzt, um die Luft aus der Porosität zu entfernen. Nach dem Einbringen des Imprägniermittels in die Kammer wird das Imprägniermittel mittels aktiven Überdrucks tief in das Gussgefüge eingebracht (Bild 2).
Bild 2: Godfrey & Wing empfahl eine CFI-Imprägnieranlage (Continuous Flow Impregnation) um die Herausforderungen zu lösen.
Das rückgewinnbare Imprägniermittel 95-1000AA bleibt während des gesamten Prozesses rein. Das Imprägniermodul der CFI dient zur Rückgewinnung des Imprägniermittels in seiner ursprünglichen Formulierung. Sobald das Bauteil imprägniert ist, bewegt es sich zu einer Zentrifuge, um nicht verwendetes Imprägniermittel zurückzugewinnen. Das so zurückgewonnene Imprägniermittel wird für zukünftige Zyklen in den Imprägniermittelvorrat zurückgeführt. Durch die Beibehaltung des reinen Imprägniermittels kann der Kunde die Bauteil-Rückgewinnung ohne zusätzliche Chemie oder übermäßige Wartung maximieren.
Nach der Imprägnierung bewegt sich das Bauteil zu den Wasch- und Härtungsstationen der CFi. Da kein überschüssiges Imprägniermittel mehr vorhanden ist, bleibt das Waschwasser sauber. Dadurch kann das Teil ordnungsgemäß gewaschen und die Bauteilsauberkeit erhöht werden (Bild 3).
Bild 3: Das saubere Waschwasser ermöglicht eine perfekte Bauteilsauberkeit.
Hauptaugenmerk bei der Entwicklung der CFi lag auf einfacher Wartung und schnellem Service. Die internen Komponenten sind so positioniert, dass eine einfache Wartung möglich ist, ohne die Produktion zu unterbrechen. Das Wartungsteam kann die Hauptkomponenten über die hinteren Zugangsklappen warten. Schnellkupplungen werden verwendet, damit sie ohne Spezialwerkzeug von Hand gewartet werden können (Bild 4). Jedes Modul verfügt über einen Netztrennschalter, sodass bei Wartungsarbeiten nicht das gesamte System für Wartungsarbeiten heruntergefahren werden muss.
Bild 4: Das Wartungsteam kann die Anlage ohne Spezialwerkzeug schnell und einfach warten.
Während die Anlagentechnologie und das Imprägniermittel nach der perfekten Lösung klangen, wollte der Kunde mehr aus erster Hand über die Technologie und das Imprägnierharz erfahren. Godfrey & Wing brachte den Hersteller in Kontakt mit einem Lohndienstleister, welcher eine CFi mit einem rückgewinnbaren Imprägniermittel betreibt.
Der Hersteller konnte das Lohnimprägniercenter besichtigen, um mehr über die Technologie zu erfahren. Die Tour hat gezeigt, dass der Prozess und das rückgewinnbare Imprägniermittel rein bleiben und keine ständige Wartung oder Benutzereingriffe erfordern. Der Hersteller war vom Durchsatz, der Effizienz und der Einfachheit der CFi beeindruckt. Basierend auf dieser Erfahrung und den vorgelegten Daten kaufte der Hersteller eine CFi-Anlage.
Das Ergebnis
Das CFi-System wurde installiert, Bediener und Wartung geschult und das System imprägnierte umgehend Teile. Seitdem erfüllt das CFI-System die Herausforderungen des Herstellers.
- Reduzierte Wartungskosten – Der Betreiber wird vorraussichtlich ca. 35.000 USD pro Jahr an Wartungs- und Ersatzteilkosten einsparen.
- Effizientes und einfaches Imprägniermittel – Der Betreiber muss keine WaschWasserChemie mehr kaufen, und die Wartung und Überwachung des Imprägniermittel wird erheblich reduziert. Der Hersteller spart jährlich ca. 20.000 USD an Imprägniermittelkosten.
- Verbesserung der Abdichtrate – Die First Time Through (FTT) -Rate des CFi-Systems beträgt 99%. Durch diese Erhöhung um 14 Punkte gegenüber der vorherigen Abdichtrate werden jährlich ca. 630.000 USD an wiedergewonnenen Gussteilen eingespart.
Insgesamt wird erwartet, dass die Kosteneinsparungen und die verbesserte Rückgewinnung dem Hersteller etwa 685.000 USD pro Jahr einsparen, sodass die Rückerstattung der Kapitalkosten weniger als 24 Monate betragen wird. Die Produktivität und Wartungsfreundlichkeit des CFi-Systems hat den Eindruck des Herstellers zur Vakuumimprägnierung verändert.
Zusammenfassung
Die Wahl des richtigen Imprägnierprozesses und des richtigen Imprägniermittels ist entscheidend für den Kauf von Vakuumimprägnieranlagen. Sobald die Entscheidung getroffen wurde, kann sie nicht mehr rückgängig gemacht werden. Durch die sorgfältige Analyse seiner Daten wählte dieser Hersteller die richtige Ausrüstung und Imprägniermittel für seine Anforderungen aus. Die CFi im Zusammenspiel mit rückgewinnbarem Imprägniermittel veränderte den Imprägnierungsprozess des Herstellers, indem er die Kosten senkte, die Qualität erhöhte und die Effizienz verbesserte.
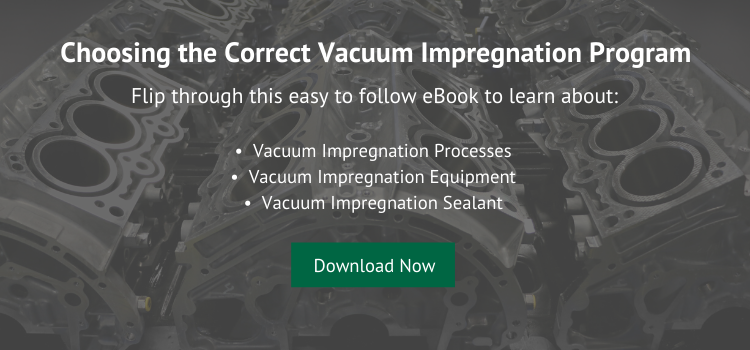