Category Archive: Uncategorized
Our new Mexico vacuum impregnation plant is featured on the cover of the Fundidores April addition.
If you have not read the recent Fundidores from Metal Spain, then click here to download your free copy. FYI, the magazine is both in Spanish and English. The Englsih version begins on page 28.
Our Mexico service center opened towards the beginning of this year and is located in Santa Catarina, part of the Monterrey Metropolitan Area in the state of Nuevo Leon.
This new facility comprises 10,000 square feet and houses the HVLV, GW’s groundbreaking impregnation system that uses a patented single piece flow Dry Vacuum and Positive Pressure (DVP) process. Click here to learn more about our Mexico location.
For more information about Godfrey & Wing, please contact us by email or call +1.330.562.1440.
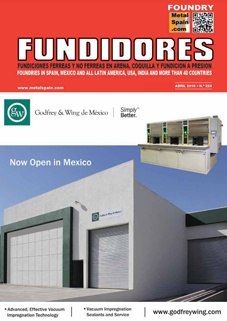
As we begin a New Year, we want to share our top 3 most read blog posts of 2014. If you missed any of these articles, be sure to check them out. They include helpful information about continuous flow vacuum impregnation, the quality of an impregnation process and sealants.
(more…)
As we approach a shutdown used by many manufacturers to service plant equipment, it is important to ensure that impregnation systems and sealants be included in the shutdown maintenance program.
(more…)
The Continuous Flow Impregnation (CFi) System is a lean, front loading vacuum impregnation system that uses a robot for part handling and transfers between modules. This impregnation system has a cycle times of less than 95 seconds. Individual part handling leads to many process improvements, such as shorter cycle times, better rinse results without risk of contamination, damage or discoloration. Furthermore, each part passes through an identical process, and process parameters can be directly associated with a particular part (tracking).
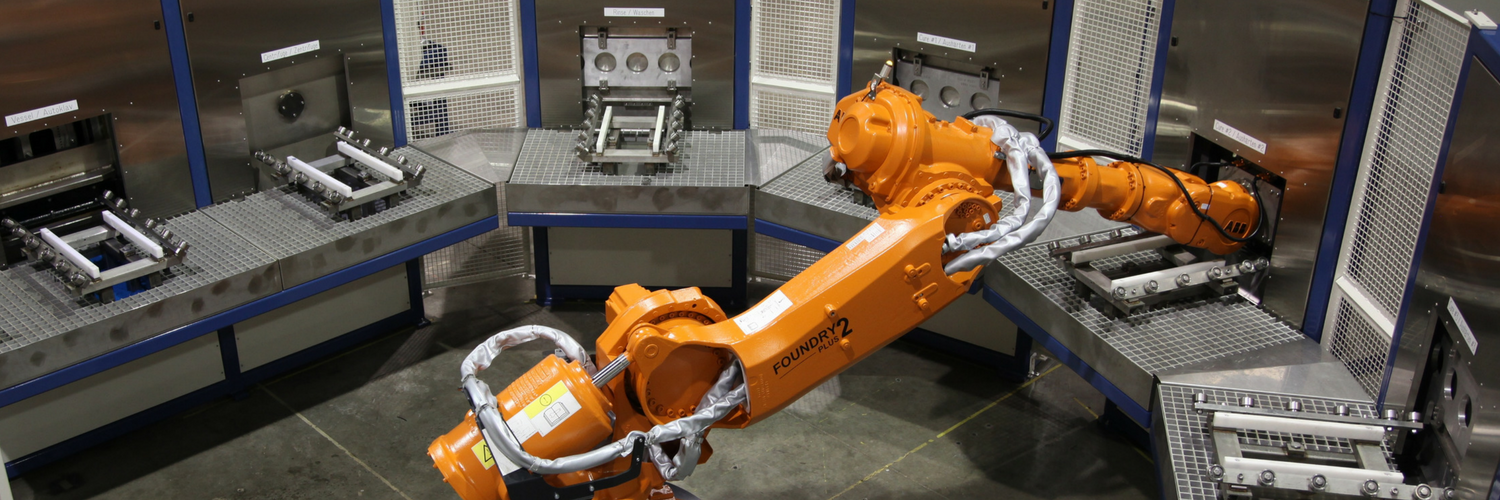
Continuous flow is the most recent technology in vacuum impregnation. Continuous flow vacuum impregnation systems are cellular or lean in design, focused on conserving valuable resources including labor, power and floor space while being more ergonomic than batch systems. The individual modules are loaded from the front, eliminating the need for overhead hoists and cranes. These systems impregnate smaller size batches or single components per impregnation cycle. This allows for reduction of individual module cycle times as well as increased mechanical manipulation assisting in the accomplishment of the four basic tasks of the impregnation process.
Modular Manufacturing
In general, lean, front loading continuous flow vacuum impregnation equipment uses smaller modules with little or no supporting infrastructure. Front loading systems can occupy as little as 86 ft2 of floor space and utilize conventional basket dimensions (e.g.: 600 x 450 x 350 mm), which can be adapted to meet specific part dimensions, if required.
Advantages of continuous flow vacuum impregnation systems:
- Smaller, self-contained modules requiring less floor space and infrastructure
- Increased throughput through faster cycle times with lower end points in vacuum and positive pressure
- Smaller payload or single part handling with improved mechanical manipulation of parts promoting enhanced sealant recovery and washing
- More repeatable processing reducing the need for inspection
- Lower in-process sealant requirements resulting in better control of raw materials
Disadvantages of continuous flow vacuum impregnation systems:
- Inability to process larger, heavier parts in excess of 60 Kg
- May require custom fixtures or tooling to secure parts during processing
Production Repeatability and Integration
The CFi technology is fully self-contained for quality with the robot and PLC working together to ensure that parts do not leave the cell if they have not met all of the pre-determined process parameters. Likewise, the use of robotics shortens cycle times, improving overall TAKT time and production volumes. At the same time robotic handling provides for repeatable processing while controlling handling damage.
The Continuous Flow Vacuum Impregnation technology offers manufacturers and OEMs the opportunity to completely integrate the impregnation process into their overall production line eliminating labor, reducing WIP and controlling costs. Existing cells deliver over 240,000 cycles per year operating 24/7. They are ideally suited for larger powertrain installations where uniformity and repeatability are essential to part quality and delivery is paramount. Higher volumes, expansion or ramping production can be met by integrating duplicate cells. The Continuous Flow Vacuum Impregnation technology enables continuous production through lean manufacturing.
Top Loading vs. Front Loading vs. Continuous Flow Vacuum Impregnation Systems
System | Workload Size | Process | Cycle Time | Use | Labor | Floor Space Requirement |
Top loading batch system | 24-96 inches in diameter; working depths of 12-120 inches | DVP, DV or W | 20-40 minutes | Jobbing and processing hundreds of unique parts, large and small | High | 1.000 to 10.000 square feet, including storage and support equipment |
Front loading system | Rectangular tote size of 300 mm x 400 mm x 800 mm | DVP or DV | 240-540 seconds | Specialized, similar parts, large and small | Low | Low |
Continuous flow system | Rectangular tote size of 300 mm x 400 mm x 800 mm or direct part handling | DVP or DV | 90 seconds | Specialized, similar parts, large and small | Low to None | Low - less than 600 square feet |
MIL-I-17563C is the Military Specification for cast or powder metal components. This specification is approved for use by all Departments and Agencies of the Department of Defense and “covers the requirements for impregnants suitable for use in sealing the voids found in cast or powder metal components which cause leaking of contained fluids.”
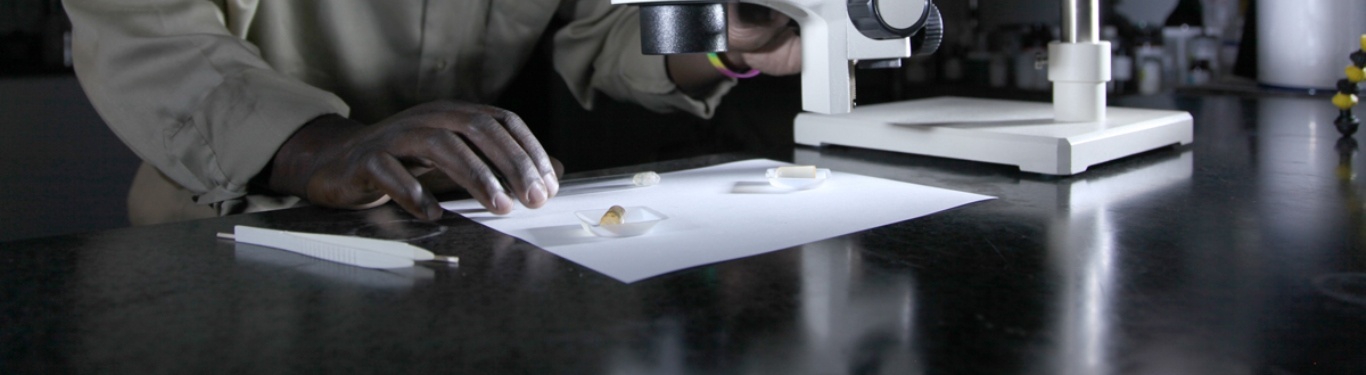
To answer the question above, it’s important to first understand the 3 classifications within MIL-I-17563C.
Class 1 – Suitable for service temperatures up to 300°F (149°C)
Class 1a – Suitable for use on mortar shell castings up to 300°F (149°C)
Class 2 – Suitable for service temperatures up to 500°F (260°C)
Class 3 – Suitable for use where air pollution requirements apply and compatible with acrylic-nitrocellulose lacquer paint system up to 300°F (149°C)
In general, all organic based vacuum impregnation sealants are qualified to Class 1 and 3. Class 2 was designed specifically for sodium silicate which is in very limited use today, and Class 1a qualifies the sealant to be compatible with TNT (Trinitrotoluene) and Composition B explosives.
To qualify for MIL-I-17563C, the sealant is subjected to various tests including pot and storage life stability. Once activated, the sealant must be stable at 75 +/- 5°F (24 +/- 2.8°C) for one month for thermal cure and 45 +/- 5°F (8 +/- 2.8°C) for anaerobic while under aeration. Un-activated or un-catalyzed material in an unopened container must meet the manufacturer’s original specification at the end of one year from date of manufacture. All Godfrey & Wing sealants are approved for two (2) years.
The sealant reactivity to various metals including aluminum, copper, iron, magnesium and zinc is also tested. Samples must not exhibit any obvious surface defect such as holes, pits and fissures. Samples with copper shall not show a greenish coloration after exposure for 24 hours.
Godfrey & Wing currently has five sealants approved on QPL-17563 and are listed below:
95-1000 – Thermal curing
95-1000A – Thermal curing
95-1000AA – Thermal curing
95-1000AC – Anaerobic
95-1000ACP – Anaerobic
Conditioning testing under various test media, time and temperature are shown in Table 1.
TABLE 1 – Conditioning Tests
Impregnation Class | Material | Media Specifications | Time | Temperature |
1 and 3 | Carbon Removal | P-C-111 | 30 minutes | 73.4 +/- 3.6 °F (23 +/- 2 °C) |
| 18% Sulfuric Acid | O-S-809 | 2 hours | 73.4 +/- 3.6 °F (23 +/- 2 °C) |
| Turbine Fuel | MIL-T-5624 | 48 hours | 73.4 +/- 3.6 °F (23 +/- 2 °C) |
| Fuel | ASTM D-910 | 48 hours | 73.4 +/- 3.6 °F (23 +/- 2 °C) |
| Diester Grease | MIL-G-23827 | 48 hours | 73.4 +/- 3.6 °F (23 +/- 2 °C) |
| Stoddard Solvent | P-D-680 | 48 hours | 73.4 +/- 3.6 °F (23 +/- 2 °C) |
| Ethyl Alcohol | MIL-E-463 | 48 hours | 73.4 +/- 3.6 °F (23 +/- 2 °C) |
| Hydrocarbon Fluid | TT-S-735 | 14 days | 73.4 +/- 3.6 °F (23 +/- 2 °C) |
| Water | N/A | 14 days | 212 °F (100 °C) |
| Oil | MIL-H-17672 | 14 days | 210 +/- 5 °F (99 +/- 2.8 °C) |
| Hydraulic Fluid | MIL-F-17111 | 14 days | 210 +/- 5 °F (99 +/- 2.8 °C) |
| Lubricating Oil | MIL-L-7808 | 48 hours | 255 +/- 5 °F (121 +/- 2.8 °C) |
| Ethylene Glycol | MIL-E-9500 | 14 days | 300 +/- 5 °F (149 +/- 2.8 °C) |
| Ethylene Glycol | MIL-E-9500 | 14 days | 397 +/- 5 °F (197 +/- 2.8 °C) |
| Thermal Resistance | N/A | 14 days | 300 +/- 5 °F (149 +/- 2.8 °C) |
As we begin a New Year, we want to share our top 5 blog posts of 2013. If you missed any of these articles, be sure to check them out. They include helpful information about vacuum impregnation economics, processes and sealant.
How Much Does it Cost to Impregnate a Part?
Or in other words, how much sealant will a part consume? Parts consume sealant in two ways as part of the normal vacuum impregnation cycle.
Types of Vacuum Impregnation Processes
There are a variety of factors that can help you determine which type of vacuum impregnation system will best meet your needs, including processes, systems and sealants.
What Vacuum Impregnation Is Not
When thinking about vacuum impregnation it’s important to remember a few things that the process does not do.
Vacuum Impregnation Economics
If the impregnation process is not efficient and fails to seal the casting it will become scrap, and the number and value of these failures will determine the economic viability of the process.
What Is the Sealant Consumption with Godfrey & Wing Sealants?
Some manufacturers state that sealant consumption is 10 grams per impregnated kilogram. Other manufacturers state 5 grams and some even say less than 2 grams. All of these numbers may be correct.
For more articles about vacuum impregnation, visit the Godfrey & Wing blog.
We often write about the different types of vacuum impregnation systems that are commonly used and how each may be best suited for use when processing a particular type of part. Once you have determined the type of system that is required, you then need to select the appropriate sealant for the system and application.
(more…)
Is it more cost-effective to repair your existing vacuum impregnation equipment or to purchase a new system? There are many factors to consider when making this decision.
(more…)
I often meet with potential customers who are hesitant to implement a vacuum impregnation process for a variety of reasons. In this article, I will discuss the most common reasons as well as provide some explanation as to why and how a vacuum impregnation program can benefit your business.
(more…)
One of the most common questions in vacuum impregnation is how much does it cost to impregnate a part, or in other words, how much sealant will a part consume? Parts consume sealant in two ways as part of the normal vacuum impregnation cycle.
The first way that parts consume sealant is that sealant actually penetrates and gets trapped inside the part where the sealant then solidifies and seals the part. The second way sealant is consumed in the vacuum impregnation process is the design waste. This is the excess sealant on the outside of the part that ultimately gets washed off and discarded. If you know the amount of sealant that gets trapped (picked up) inside the part during the impregnation cycle, then you can do a rough estimate of the overall cost simply by multiplying the “pick up” amount by 4.
This calculation not only takes into consideration the sealant cost but also compensates for compressed air, electricity, water, labor, and design waste associated with the overall vacuum impregnation process. It does not, however, include any factor for profit, depreciation, freight, general or administrative expenses, selling costs, or any other non-impregnation process costs.
With that in mind, we can provide some basic information to help you establish sealant pick up rates for both powder metal (PM) parts and traditional aluminum-based parts. This information is based on historical data and is only meant to provide a ballpark understanding of typical sealant consumption. Given that every part is unique and different your application may or may not adhere to these guidelines. As for PM parts with a typical density of 6.8, you can assume an average pick up rate of 1 gram of sealant for every 40 grams of compacted metal. So, if a compacted part weighs 160 grams it will usually pick up about 4 grams of sealant.
For aluminum, let’s assume a density of 2.8 grams/milliliter. If you know the weight of the aluminum part in grams you can simply divide that by the density to get the volume of the part in milliliters. By dividing that by 1,000 you can convert the volume to liters. Once you have the volume you can simply multiply that result by a factor of 8 to get the estimated sealant pick up. For example, if a part made from aluminum weighs 1,500 grams, divide that by 2.8 to get 535mL. Divide 535 by 1,000 to convert to liters which will yield .535. Multiplying the .535 by 8 will provide an estimated sealant pick up of 4.3 grams. This information can then be used to help establish your annual sealant volume or daily sealant consumption.
Page 9 of 11« First«...7891011»