Category Archive: Uncategorized
Like most manufacturing processes, porosity is inherent to powder metallurgy. Porosity is only considered a defect if it is interconnected and creates a leak path can affect the part’s structural integrity and performance. This blog discusses the four main reasons why vacuum impregnation is used to seal powder metallurgy leak paths.
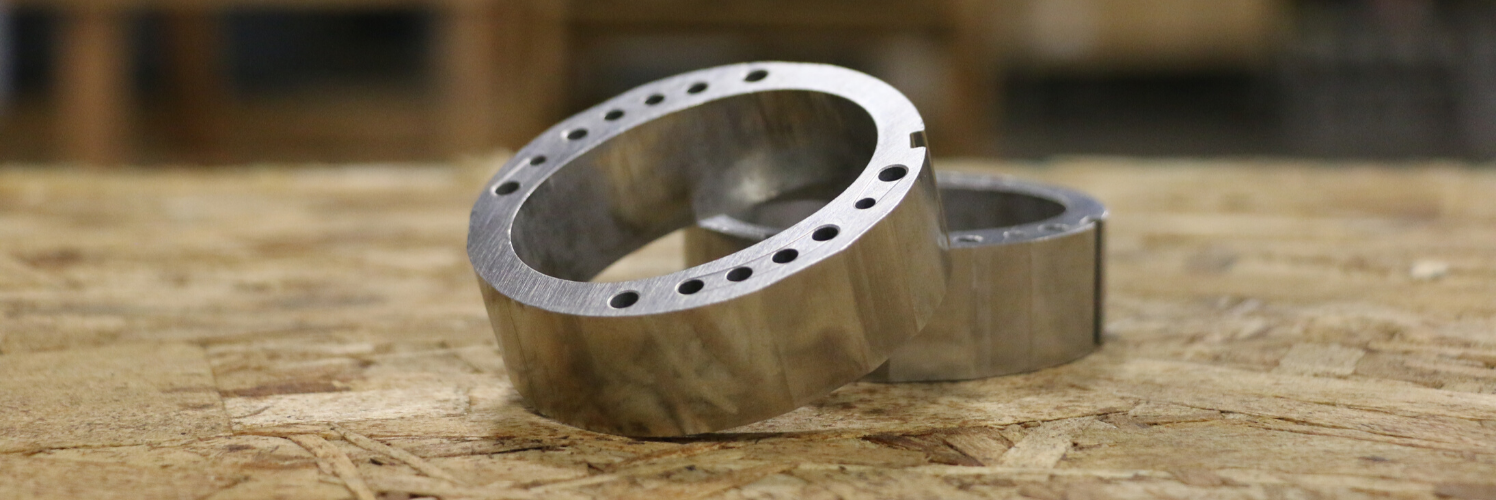
Preventing Fluids or Gases from Leaking Under Pressure
If the leak paths are not sealed, then fluids or gases may leak from the part. Vacuum impregnation prevents fluids or gases from leaking by sealing the porosity and leak paths. The process does this without changing the powder metal component’s dimensional or functional characteristics
Reduce Corrosion
Plating operations submerge the parts in acid solutions. The residual acid can seep into the porosity, which causes corrosion. Sealing the components before plating eliminates the risk of internal corrosion.
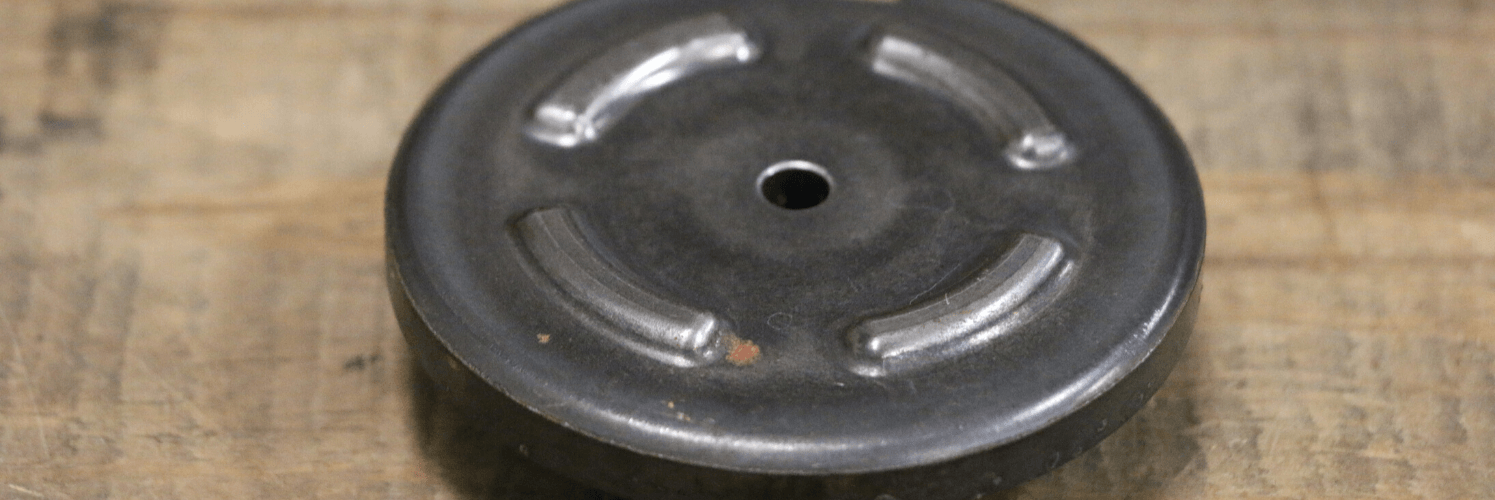
Improve Machinability
Secondary machine operations, such as drilling, tapping, or cutting, are impaired as the voids between the particles cause tool chatter, reducing tool life and finish quality. Vacuum impregnation stabilizes and supports the individual powdered metal granules during machining. This improves machinability by making it more efficient, eliminating tool chatter, and improving the machined finish.
Enhance Surface Finishing
Powder metal porosity absorbs oils, fluids, deburring fluids, pre-plating cleaners, and acids. If not sealed, fluids may bleed out and negatively affect the finish. Sealing the porosity before secondary finishes will eliminate any failure mode that could develop from bleed out of pretreatments.
Conclusion
Vacuum impregnation adds value to powdered metal components. The process eliminates failure modes caused by porosity, produces pressure tight parts, improves machinability, and meets surface finish/appearance requirements.
An effective production flow involves work stations and equipment to be arranged in a sequence that supports a smooth flow of parts and materials with minimal delays. Implementing an efficient production flow leads to increased production and flexibility, as well as a reduction in capital requirements.
Anoplate, an industry leader in surface engineering, faced a production flow dilemma. The company offers vacuum impregnation services to seal leak paths and eliminate failure modes that could develop from outgassing, chemical compatibility, or bleed out of pretreatments in porous materials. Anoplate processes high value, complex die castings for some of the largest and most respected aerospace, defense, information technology, and recreation companies in the world. The castings often have thin walls with small blind taps.
The Challenge
Anoplate’s operations span across two buildings. Its headquarters comprises of its offices and vacuum impregnation operation. The second building, located across the street, houses its vapor degreasing and plating operations. Anoplate uses in-house batch impregnation systems to process the die castings. The batch system aggregates various parts and processes them in large batches. Before impregnation, parts are processed through vapor degreasing.
Despite being well versed in vacuum impregnation, the company could not efficiently process complex castings due to three limitations of their batch systems.
- Contamination-Extra steps were needed to get clean, sealed parts. Cured sealant and oil remained in through and blind tape holes, requiring the operator to hand wash machine and tap holes after the process. Also, many parts required double impregnation.
- Sealant usage-The system processing baskets were the cause of high sealant “drag out”. This drag out led to high sealant use and increased material costs.
- Ineffective production flow– The process routing (degrease, impregnate, plate, and finish) had parts traveling between facilities multiple times, constantly placed in and out of transport dunnage. The amount of handling increased the risk of damage, reduced the control of inventory, and increased the cost of processing.
The SolutionThe company laid out its vision, and Godfrey & Wing responded with the lean, front-loading HVLV vacuum impregnation system, customized to address the company’s challenges.
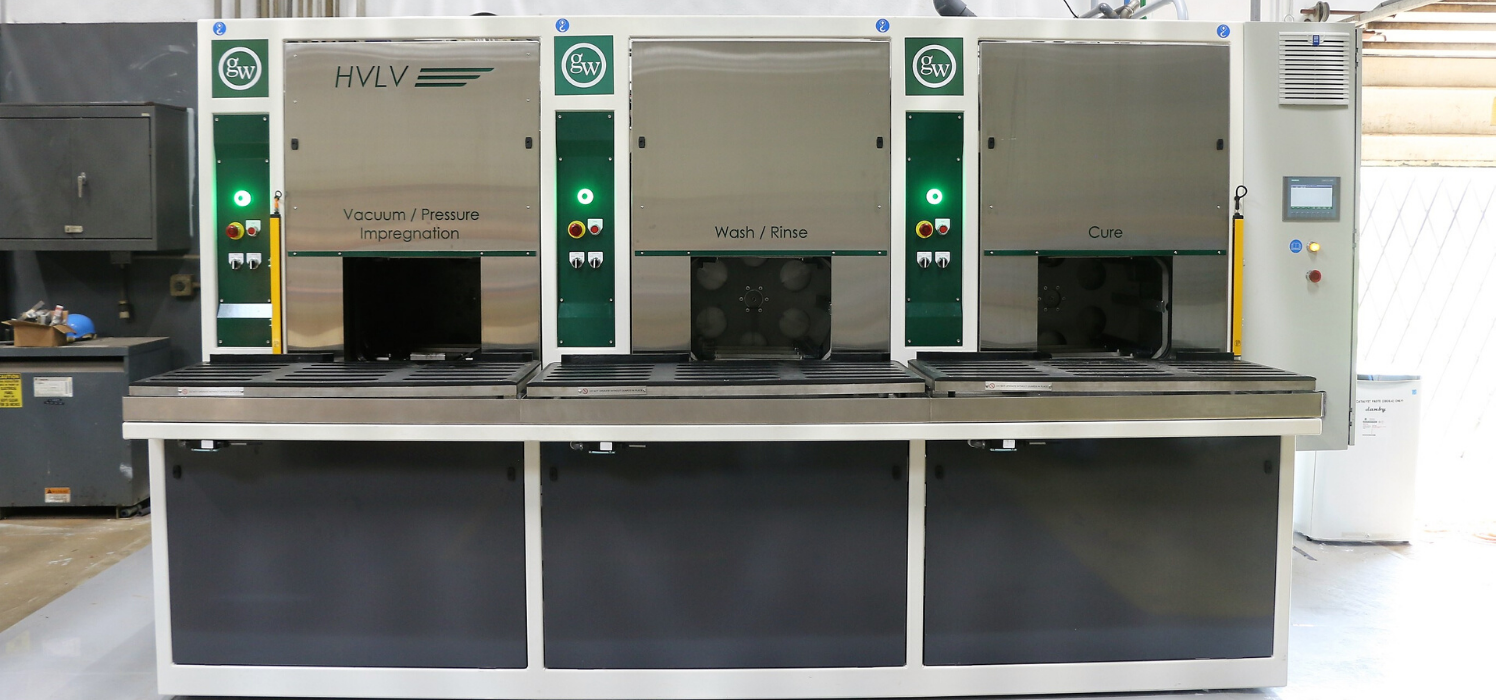
To eliminate contamination, Godfrey & Wing designed custom fixtures to maximize the number of castings per cycle and protect critical machined features. The HVLV’s advanced wash cycle was programmed with an aggressive wash to flush sealant from blind holes and machine features.
After impregnation, the part is centrifuged to recover unused sealant. The sealant is returned to the sealant reservoir for use in subsequent cycles. The HVLV recovers unused sealant before the wash, which eliminates sealant drag out, and risk of contamination.
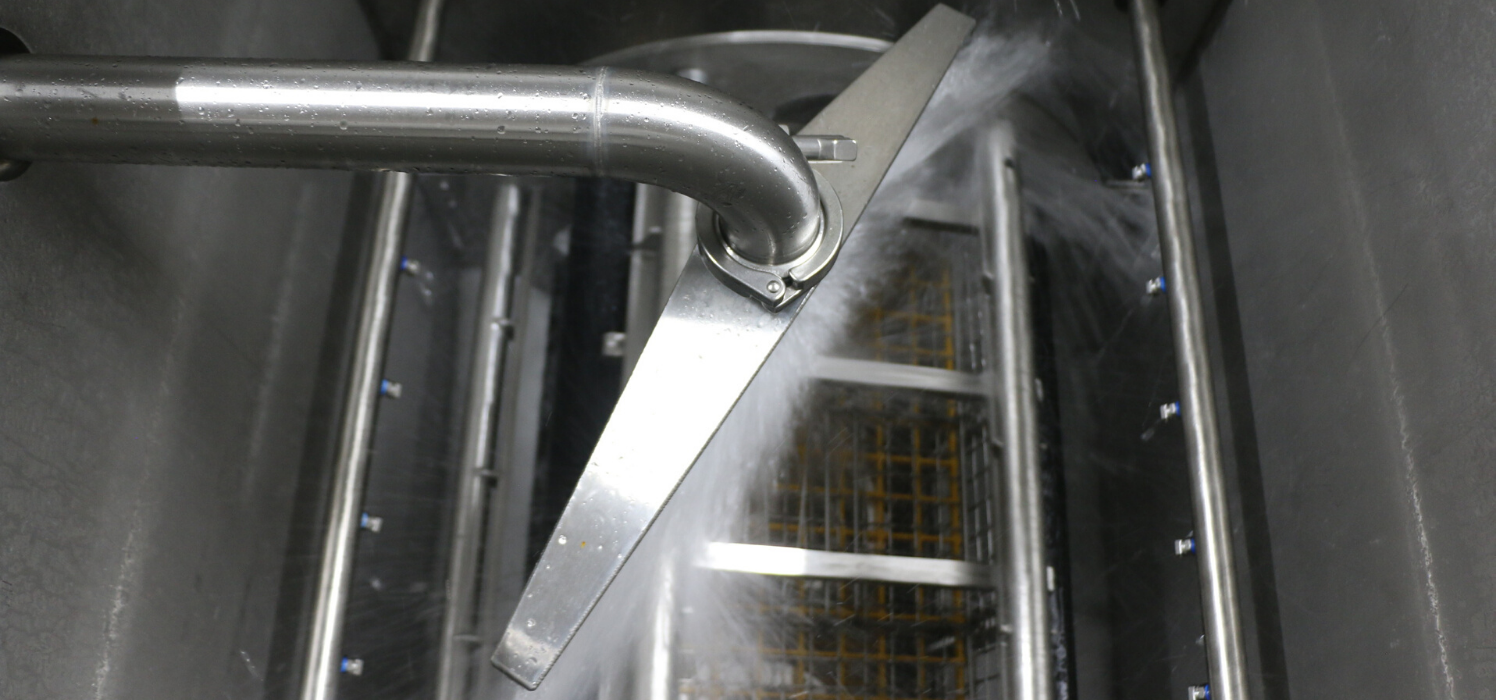
Recognizing the company’s desire to place the system in the same building as plating, Godfrey & Wing designed the HVLV to align with production. HVLV’s modular footprint requires 96 square feet without any floor changes. Godfrey & Wing also studied how the HVLV would integrate with Anoplate’s order of operations and concluded that with the HVLV, Anoplate’s vapor degreasing process could be eliminated.
While the system sounded perfect, Anoplate conducted rigorous sample testing before investing. Samples were processed at Godfrey & Wing’s headquarters on a machine identical to the HVLV proposed to Anoplate. The results demonstrated that the HVLV not only sealed the leak paths, but eliminated contamination, and reduced sealant usage. Also, the company was able to see firsthand how the modular footprint could easily fit into its existing production line. With these results, Anoplate purchased an HVLV.
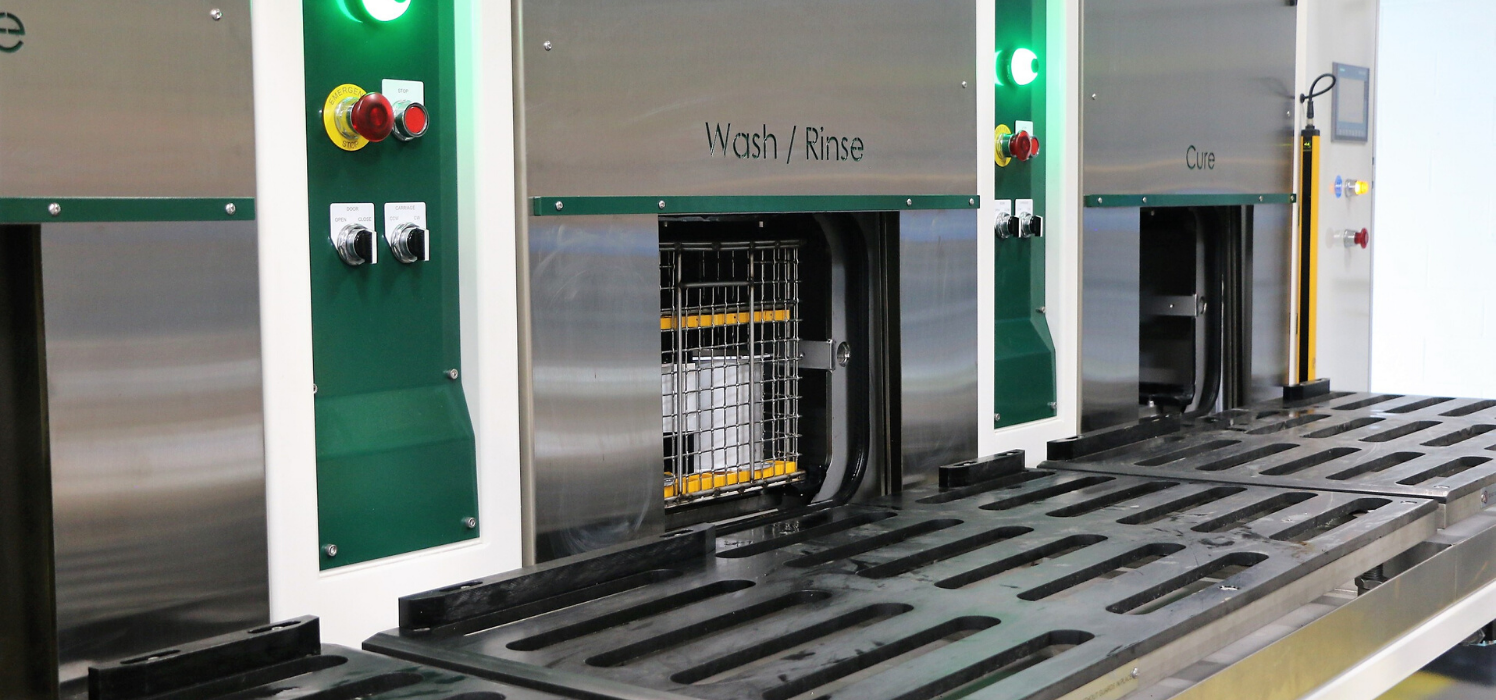
The Results
The HVLV was installed, operators and maintenance were trained, and the system was processing parts in under two weeks. Since then, the HVLV is addressing Anoplate’s challenges.
- Eliminate Contamination-The system’s custom fixtures and thorough wash processed all parts successfully and without any trace of residual sealant contamination.
- Minimize Sealant Usage-Sealant drag out has been greatly reduced, and sealant costs have gone down by 50%.
- Improve Production Flow-The HVLV operates alongside the plating operations. By delivering parts directly to the impregnation system, labor costs have been reduced by 50%, and production throughput has increased by 30%.
“Considering our challenges, the HVLV has been a very effective solution delivering unrivaled quality for our advanced manufacturing environment.” Said Jesse Campbell, Anoplate’s Vice President of Engineering, “This system has also changed our perception of vacuum impregnation equipment in that it is simple to use, and the look is sleek and modern.”
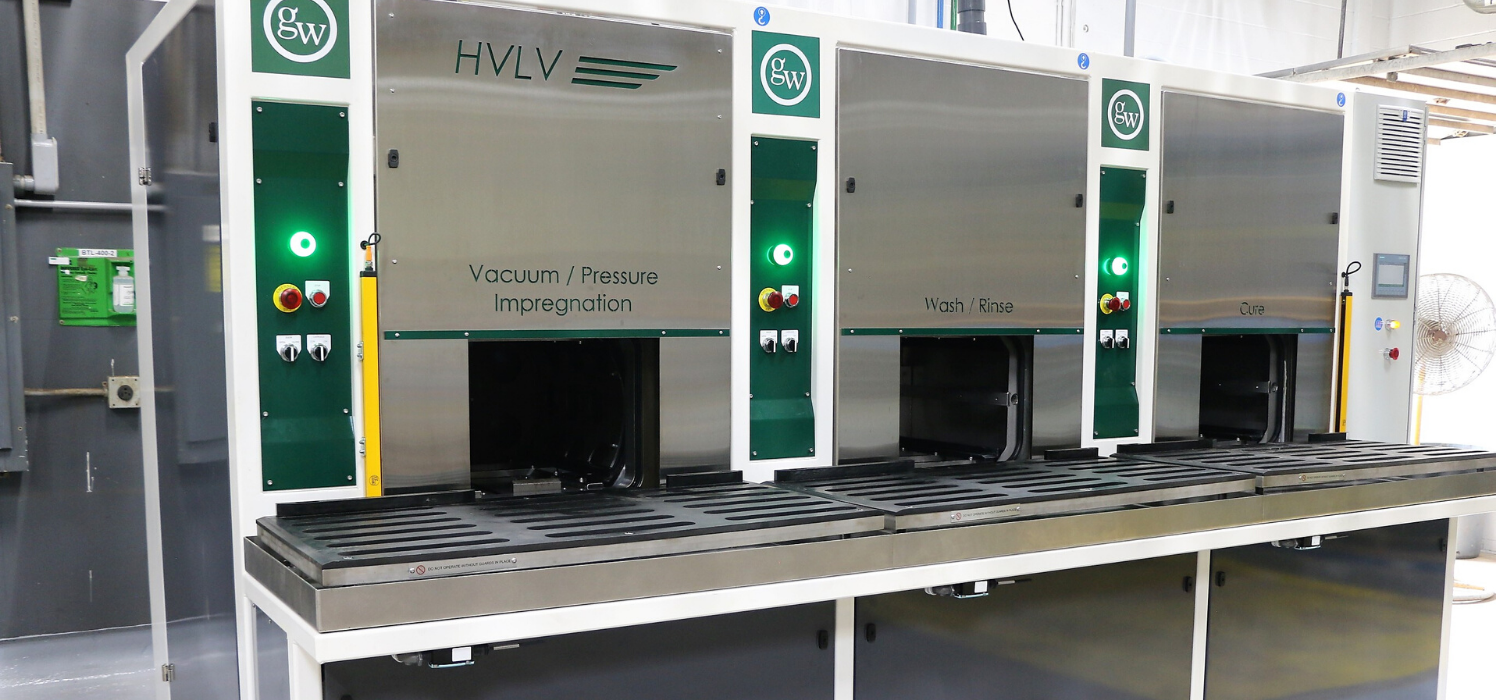
In SummaryThe HVLV has created a competitive advantage to Anoplate’s vacuum impregnation services. The system has transformed its impregnation business by reducing costs, increasing quality and improving efficiency.
Godfrey & Wing’s Continuous Flow Impregnation (CFi) system seals porosity in a short cycle time with minimal labor. In this video, John Halladay (aka Johnny Impreg) will show you some of his favorite features:
1. Compact design
2. Part traceability
3. Integrates with production
Video Transcript
Hello, everybody. Welcome to another edition of Casting Call with Johnny Impreg. I’m your host, Johnny Impreg, and again this month, we’re going to be unveiling a new piece of equipment. It seems like we just did it last month, but our equipment people have been really busy.
Favorite FeaturesThis is an automated system that’s going to go to an engine plant in Mexico, and it’s got a couple of unique features I’d like to share with you. Number one, it’s super compact, and it integrates directly in with the manufacturing facility. The blocks are fed in with an Automated Guided Vehicle (AGV). They go through the process completely automatically. They’re scanned for traceability, and they go through an outbound cooling tunnel, or they go back to, with the AGV, back to a leak test. So, super small, compact, totally integrated, complete traceability, the Godfrey & Wing CFi.
Let’s TalkHope you enjoyed this video. If you have any questions, please leave them in the comments below, and watch for another upcoming edition with some more machines that we’ll be unveiling. Thanks for your time, and as always, bye for now.
In the latest issue of Die Casting Engineer, NADCA President Stephen Udvardy reports on the overall North American die casting health. This piece discusses a variety of manufacturing topics ranging from political factors, macroeconomics, and surveying current business challenges.
Below are three takeaways in regards to the automotive industry.
Manufacturing Capacity Increase
The report states that overall, consumer sentiment is high (Figure 1). The high consumer sentiment has had a positive impact on U.S. manufacturing outlook. This has lead manufacturers to increase capacity. U.S. manufacturing capacity increased to 77.5% in the third quarter of 2019, a two-point increase from 2017 (Figure 1).
Figure 1: Consumer sentiment from 2009 through the third quarter of 2019.
Light Vehicle Sales
“The current forecast for light vehicle sales in 2019 is 16.9 million units (Figure 2). Stephen explained, ” 16.9 million units represent strong light vehicle sales, defying the predictions in 2017 that sales above or near 17.0 million could not be sustained.”
Figure 2: Monthly light vehicle sales from November 2018 to November 2019.
Electric Vehicle Sales
The report cites Statista that 1.2% of 2018 U.S. auto sales were of plug-in electric vehicles. Sales of plug-in electric cars are forecasted to grow to 7.6% of total U.S. auto sales by 2026.
In Conclusion
This report highlights a variety of economic and political barometers. Overall, the data indicates that the U.S. manufacturing outlook is healthy and encouraging.
In some die casting applications, components must also be pressure-tight to hold pressurized fluid or gases. Companies use the vacuum impregnation process to meet these requirements by sealing the internal leak paths without impacting any other features of the casting. A commonly asked question is in addition to leak paths, can vacuum impregnation seal die casting cracks? This video answers this question with easy to follow visuals.
Video Transcript
Hola, y buen dia todos. Welcome to another edition of “Casting Call with Johnny Impreg.” I’m your host Johnny Impreg and in this episode we’re gonna get into the question of “Can Vacuum Impregnation Seal Cracks?” I’d like to rephrase that a little bit and say “Should Vacuum Impregnation Be Used to Seal Cracks?” I’ll start out with the answer is, “No, you should never use vacuum impregnation to seal a crack.”
Let’s Get Into the Science
Now let’s get into the science a little bit, I’ll explain why I say that. Now, everybody’s familiar with porosity, and that’s kind of formed during the solidification process, is either shrink porosity or gas porosity. And when that forms, when the casting freezes, that’s static. It’s never going to move so that when we fill the casting porosity with sealant, that’s never going to open up again. That leak path is sealed and the sealant will survive as long as the casting. Now, if you take a look at a crack, on the other hand, a crack forms post-solidification, typically in the injection. Sometimes in handling after the casting is ejected. But, the crack is not static and can move.
Impregnating Cracks vs. Impregnating Porosity
And what will happen is sealant will actually seal it and it may pass leak tests. But then when you go to assemble it and torque it down for assembly, or worse yet, when it gets out in the field, the crack can propagate and open up again, and then that will open up the leak path. So it will fail later on.
And cracks can be a real problem with castings because it can be difficult to detect. You can actually have a crack that’s so slight it will pass leak test to be an impregnation candidate. You impregnate it and it will seal for a passing leak test, then it gets out in the field and it leaks. Oftentimes folks will jump to the conclusion that impregnation failed, but on further investigation you’ll find that there’s a crack. And some of the programs that we do, leak testing and vacuum impregnation, if it leaks in an area that we know is prone to cracking, the casting will get scrapped and not even impregnated.
So, I hope this information is helpful. If you have any questions, please look me up on LinkedIn or hit me up on WhatsApp and be happy to help out more. Take care and bye for now.
In some die casting applications, components must also be pressure-tight to hold pressurized fluid or gases. Companies use vacuum impregnation to meet these requirements by sealing the internal leak paths caused by interconnected porosity.
Misconceptions and lack of information about the vacuum impregnation process can hinder its implementation, which may increase unforeseen costs and negatively impact part quality. This piece demystifies vacuum impregnation by correcting three common myths.
Myth: Vacuum Impregnation is a CoatingFact: The process occurs subsurface, with no residual sealant remaining on the part’s surfaces, machine features, blind holes, and taps. Only the sealant drawn into the leak path by the force of the vacuum and pressure remains in the casting.
Myth: Vacuum Impregnation Causes Dimensional Changes to CastingsFact: Vacuum impregnation does not change the casting’s dimensions, thus allowing engineers the freedom to design and make parts to the net shapes. Since the vacuum impregnation process occurs subsurface, an engineer does not need to incorporate dimensional allowance.
Myth: Vacuum Impregnation is a Cork or PlugFact: Vacuum impregnation seals porosity deep within the leak path; it is not a cork or plug. In the case of visible or open porosity, low viscosity sealants will most likely be washed out of pits or holes. Thus, a casting with surface porosity or blemishes before the process will exhibit the same surface porosity and blemishes after the process. However, the leak path below the part’s surface is fully sealed.
In Summary A clear understanding of how vacuum impregnation works can help companies maximize their production results. As the preferred method to prevent fluids or gases from leaking under pressure, the vacuum impregnation process seals casting porosity that forms during manufacturing. When done properly, the casting will function so that fluids or gasses will flow only where needed while physical characteristics, simply stated, will not be different in any manner. Vacuum impregnation helps manufacturers decrease the rate of scrapped parts, increase productivity, and ultimately increase their profitability.
Productivity and quality are keys to the success of any continuous flow production philosophy. However, vacuum impregnation systems have remained antiquated, which causes production and quality issues in modern manufacturing environments. Hence their absence from most continuous flow production plans.Such is the case of a vertically integrated automotive OEM. This company had an outdated vacuum impregnation system that did not meet their continuous flow strategy. The division that operates the vacuum impregnation system pours the metal, machines, and assembles components to produce finished engines.
The Challenge
At the launch of a new engine block line, the company realized that its current vacuum impregnation system could not reliably process the new engine blocks. The OEM realized that the following challenges needed answered:
- Sealing Rate-The system was Dry Vacuum (DV) process only that resulted in below-average sealing rates.
- Floor space– The current automated system was enormous. It did not fit the desired floor space or integrate with production. As a result, the size was debilitating to their production flow.
- Maintenance– The system required continuous support. Maintenance areas were difficult to access. Spare parts were expensive and needed the company to keep a high inventory.
The Solution
The OEM’s leaders realized that the current vacuum impregnation system would need to be replaced with a modern impregnation system.
Based upon these roadblocks, Godfrey & Wing recommended its Continuous Flow Impregnation (CFi) system. The system would be customized to answer the customer’s challenges.
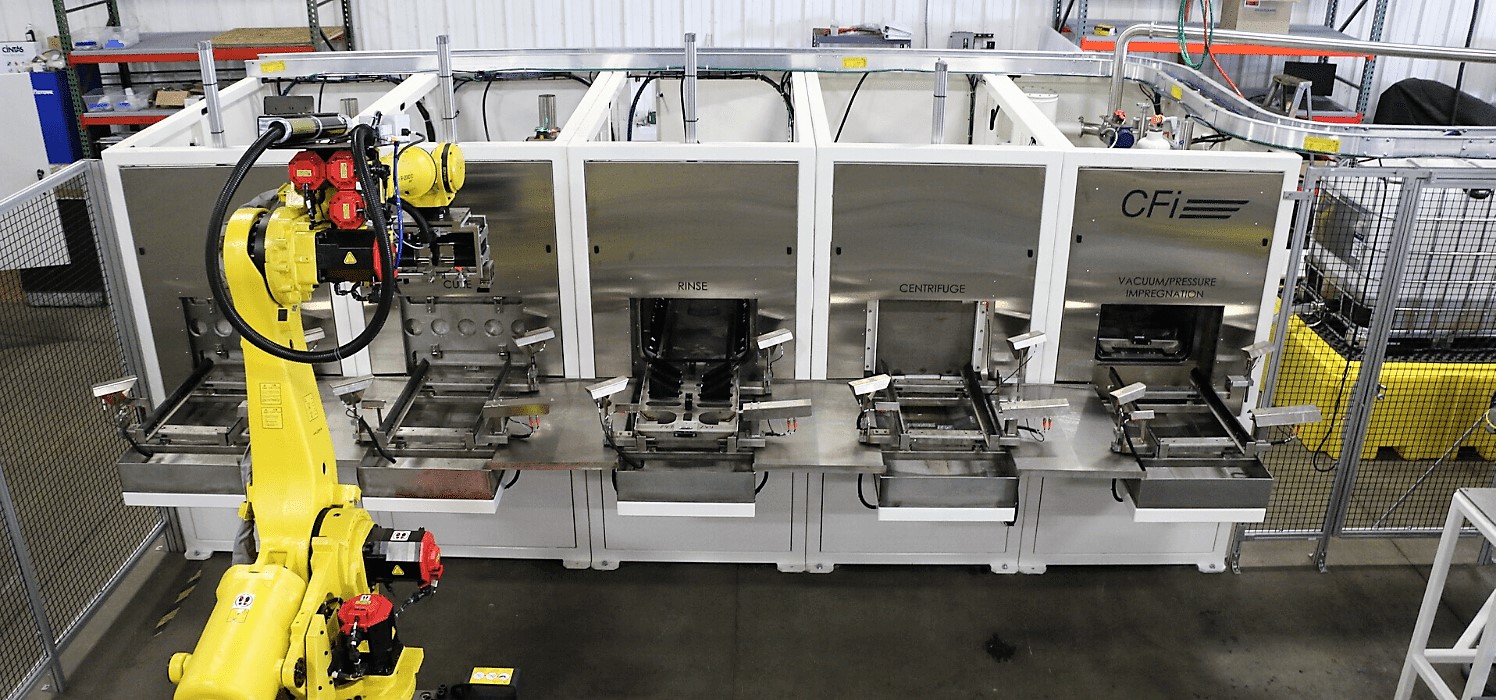
To improve the sealing rate, the CFi uses the patented Dry Vacuum and Pressure (DVP) process, which yields a higher seal rate than the DV process. The CFi with the DVP process incorporates a fast, deep vacuum to evacuate the air from the porosity. Then after moving sealant to the part, the system applies high pressure to allow the sealant to penetrate deep in the casting walls.
The OEM specified precisely where to place the system on the manufacturing floor. Knowing this, the Godfrey & Wing engineering team designed the layout to accommodate the floor space and production integration.
The system was designed with a 7-axis robot for parts handling, and conveyors integrated with machining and leak test operations. The robotic arm forms the interface between the impregnation system and the processing line while using the least amount of space. After impregnation, the castings are fed by the robot directly to leak testing via a cooling conveyor belt. The automation enables continuous production in a modular, compact space.
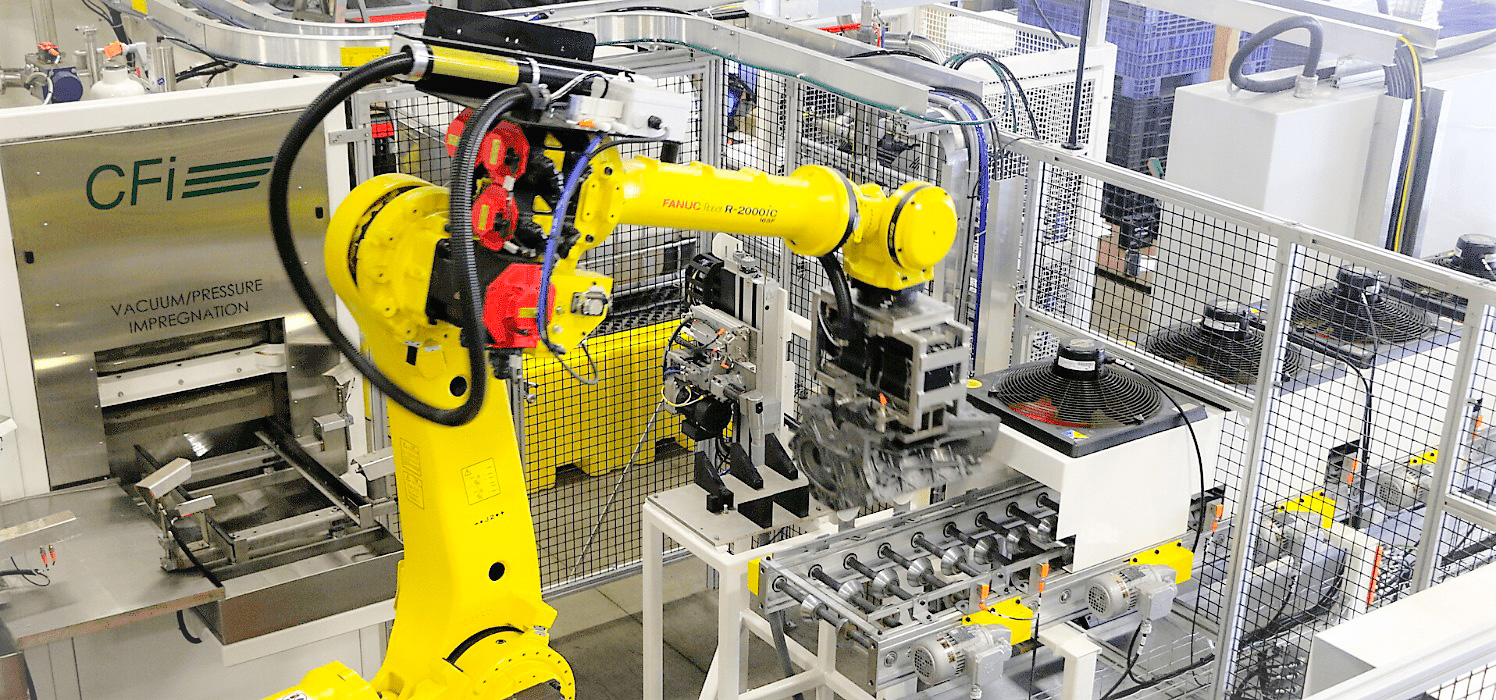
The internal components were positioned to enable ease of maintenance without interrupting production. The maintenance team is now able to service principal components through the rear panel doors, rather than accessing the system through the safety fence. Sanitary connectors are used that can be maintained by hand without the need for specialty tools. Each module has a line rate disconnect so that maintenance does not need to power down the entire system for service.
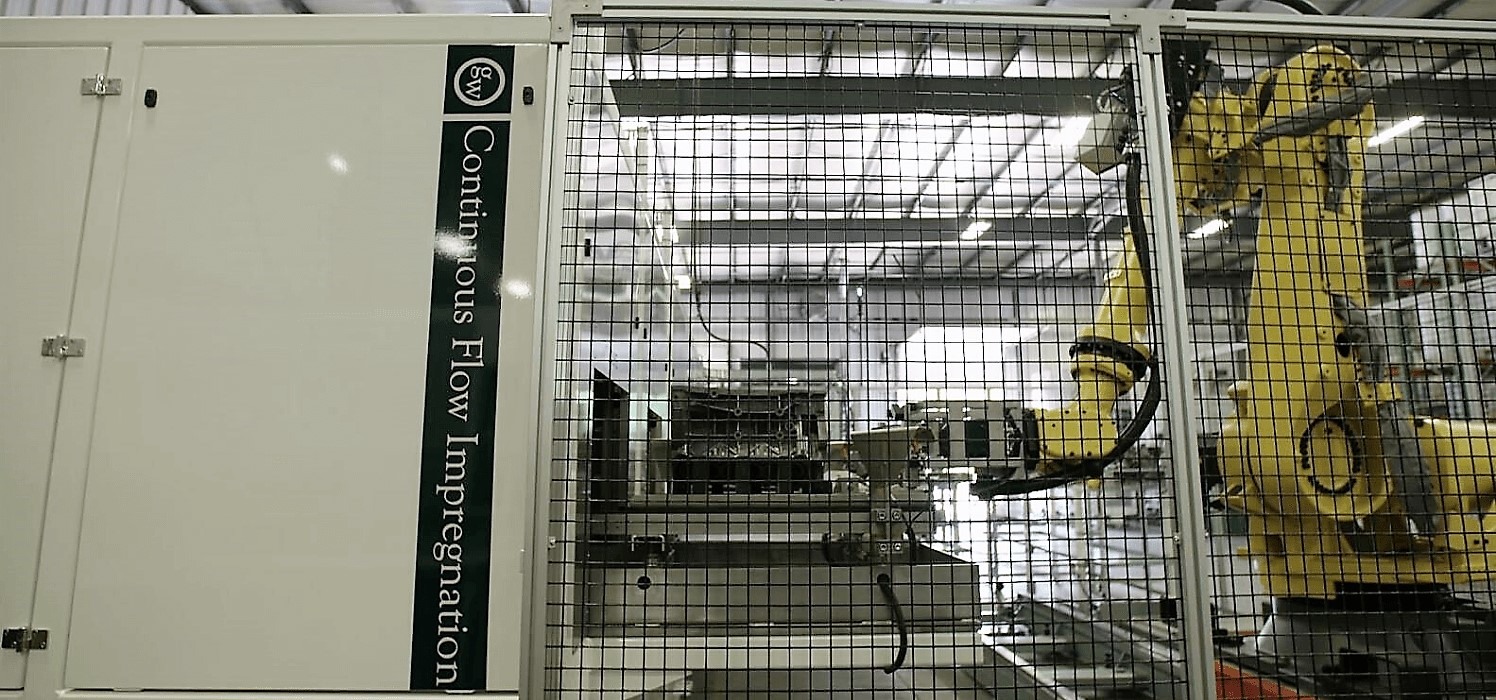
The Results
The CFi was installed, operators and maintenance were trained, and the system was running production in two months. Since then, the CFi is addressing all the company’s challenges.
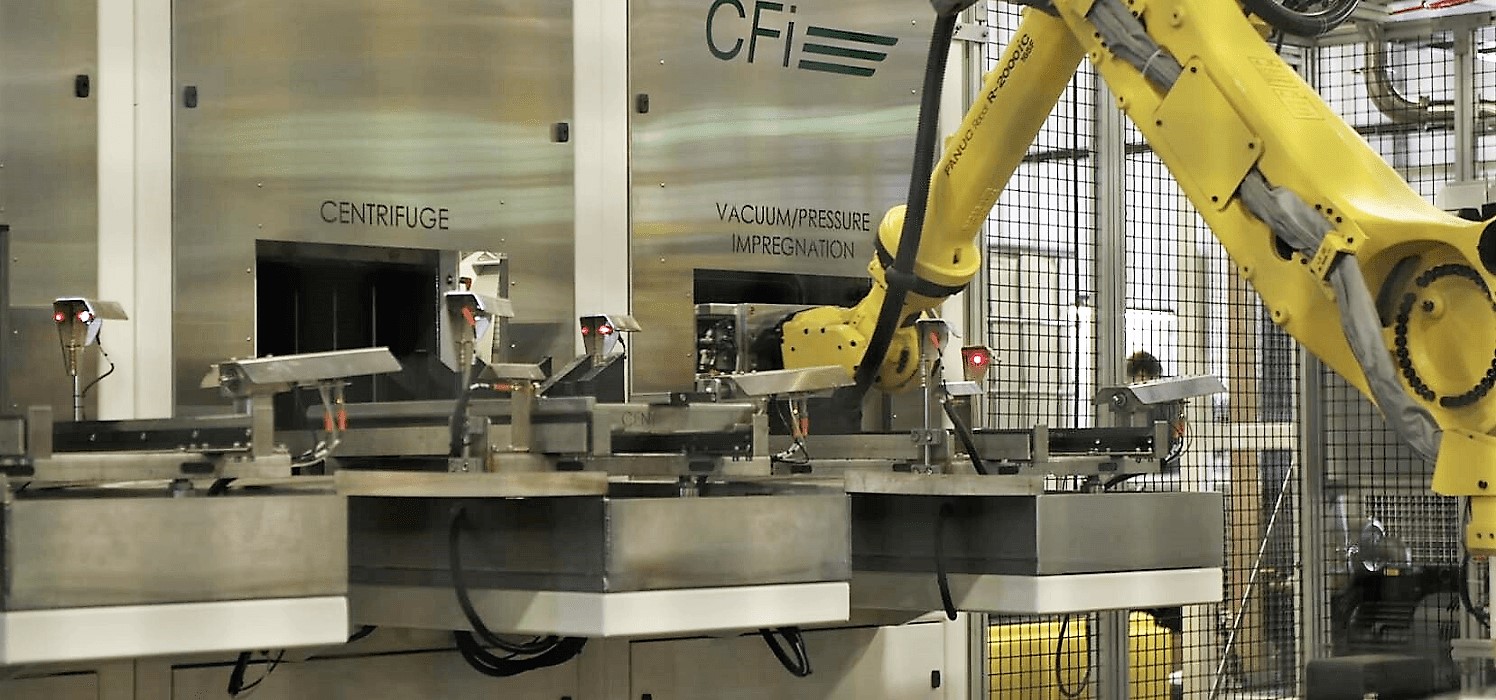
- Increased Sealing Rate– The CFi has increased recovery of the castings by 15%. Scrap from porosity has been virtually eradicated.
- Conserve Floor Space– The system layout cut required floor space by over 50%.
- Reduced Maintenance Cost– The purchase of the CFi has reduced maintenance costs by 65%.
In Summary
As OEMs search for ways to improve continuous flow manufacturing, it is necessary for a paradigm shift. This OEM found value in doing so by investing in a lean and modern vacuum impregnation system. The CFi plays an integral production role by increasing casting recovery while reducing maintenance
In some die casting applications, components must also be pressure-tight to hold pressurized fluid or gases. Companies use vacuum impregnation to meet these requirements by sealing the internal leak paths without impacting any other features of the casting. A commonly asked question is in addition to leak paths, can vacuum impregnation seal cracks?
(more…)
We look forward to seeing you while you visit Cleveland during NADCA’s Die Casting Congress & Tabletop. We’re home to a number of distinguished attractions and award-winning eateries. If you are looking for things to do in your free time during the show, below is a list of some of our favorites.
(more…)
As manufacturing equipment ages, the Overall Equipment Effectiveness (OEE) decreases. A company that fails to invest in equipment, will not be able to meet demand or produce a quality product, thus potentially losing its competitive edge. Companies who want to succeed in this landscape are identifying equipment investment opportunities to keep production moving and while producing a quality product.
(more…)
Page 4 of 11« First«...23456...10...»Last »