In an earlier blog article, we discussed the most common ways that sealant can get into vacuum pumps during the impregnation process.As a reminder, the list included:
- The transfer valve no longer functions as designed, typically caused by wear and tear over time. This leads to a leaking valve during the vacuum cycle and the possibility of the sealant being pulled into the vacuum pump.
- The upper level sensor in the vessel no longer functions as designed. The by-product is that the PLC never receives a signal to close the transfer valve when sealant reaches the upper level sensor. Therefore, sealant continues to transfer, possibly all the way into the vacuum pump.
- Excess sealant foam is generated. Mechanical failures can introduce excessive air into the process, causing the sealant to boil more than normal during the degassing phase of the vacuum process. Regardless of what caused the foam (failed sensors, failed valves, leaks in the system, cavitation from poorly adjusted process, etc.), the excess foam may not be seen by the upper level sensor and can find its way to the vacuum pump.
The next step is to discuss how to defend against the problem of sealant getting into vacuum pumps. Even if an impregnation system is properly set up and maintained, accidents can happen that can lead to this problem. The best defense is a trap that the sealant can be “caught” in prior to reaching the pump.
Depending on the level of protection desired, traps can be as simple as a loop in the vacuum hose/line or as sophisticated as a mechanical trap with sensors.These traps are located between the impregnation vessel and the vacuum pump.The purpose of a trap is to give the sealant an alternative place to go (get trapped) versus into the vacuum pump.
The simplest approach, which is effective when sealant rarely enters the vacuum pump, is to loop the vacuum hose/line in such a way that gravity alone stops sealant before the pump.In this case, the weight of the sealant cannot overcome gravity and therefore cannot reach the peak of the vacuum hose, thereby “trapping” it in the line, typically to drain back into the vessel.
The next level of technology is a mechanical trap that is either maintained manually or set up for semi-automation (Fig 2 below). With these types of traps, there is a level sensor that sends a signal to the PLC, indicating that it is full and needs to be drained. A manual drain at the bottom allows maintenance personnel to easily drain the system.
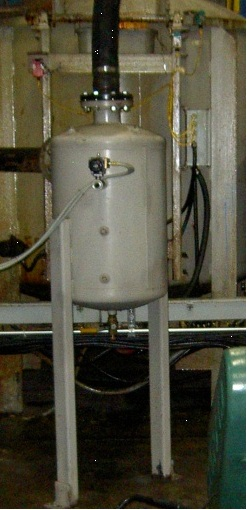
The highest level of technology is a fully automated trap that allows for continuous running of the impregnation system (Fig 3 below). These traps also have level sensors to indicate when they are full. In addition, the traps are connected to pneumatic valves that are programmed to open between cycles, draining any sealant in the trap back into the sealant reservoir.
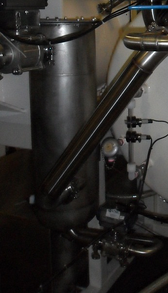
The interior of the mechanical traps can be of various design. Those requiring the least maintenance will have steel baffles that the air/sealant would have to navigate to get to the pump. Designed correctly, these are very effective and pulling any sealant out of the air flow.
Another option is to have filter elements (typically in the 5 micron range) that the air can pass through, yet the sealant will be trapped in.
Depending on the size and performance of the system, a cost-effective Vacuum Sealant Trap can be designed and installed. The additional protection for the vacuum pumps are worth the investment so as to reduce downtime and maintenance costs.
For more information on this topic, contact Godfrey & Wing.
In the vacuum impregnation industry one of the more frequent topics of discussion surrounds the difference between anaerobic and thermal curing impregnation sealants.
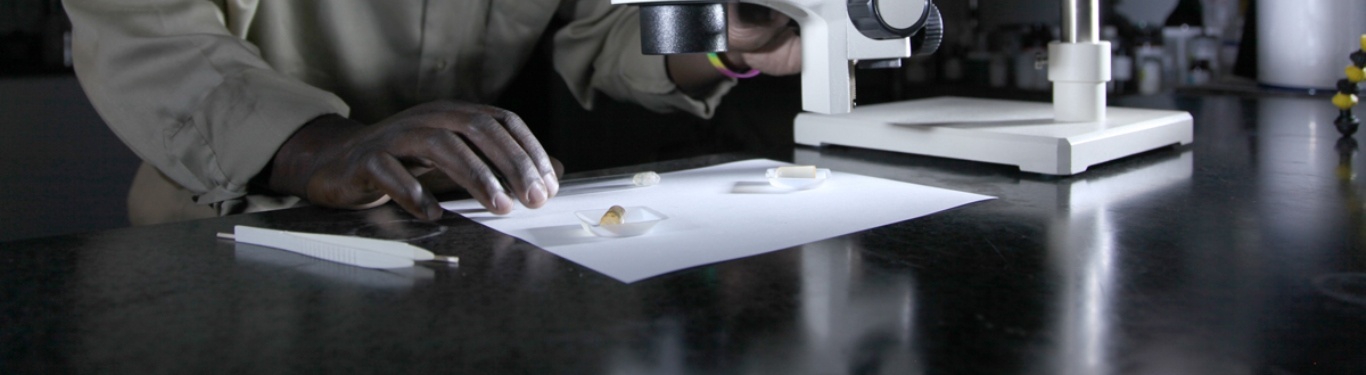
It is well known that thermal cure sealants, like Godfrey & Wing’s 95-1000A and 95-1000AA, are more widely used than anaerobic sealants (95-1000AC and ACP). Many will say the reasons for the increased use of thermal cure sealants are acquisition cost of the sealant or equipment. Others will cite ease of maintenance while still others will say it is due to the elimination of a host of failure modes.
In reality the decision for choosing a specific style of sealant lies with the part to be impregnated. Some parts are just more likely to be sealed in one versus the other. It has nothing to do with the quality of the sealant, but it has everything to do with the materials being impregnated and the size of the pore or leak path.
Compare Vacuum Impregnation Sealanats
| Thermal Cure | Anaerobic |
Curing | Polymerizes when heated to 195°F | Polymerizes in the absence of air over 24-48 hours |
Pressure Testing | Immediately after impregnation | Need to wait 24-48 hours after impregnation |
Maintenance | Continuous refrigeration | Continuous refrigeration and aeration |
Packaging | 5 gallon, 50 gallon, 250 gallon | 4-5 gallon carboy |
Applications | Castings, aluminum, iron, steel, zinc | Powdered metal, electrical applications, cables |
Powdered metal applications have large, through porosity and work best when using an anaerobic sealant. Why is this? First, once impregnated into the part, the sealant may be activated in a chemical bath to seal the pore at the surface, allowing the remaining sealant trapped in the porosity to cure over time. This reduces the chance of sealant migration from the pore which could be found when using a thermal curing sealant with large open porosity.
Likewise when sealing micro-porosity in a casting, a thermal cure sealant will perform better than an anaerobic as the process used to impregnate thermal cure sealants is more robust and thorough. Also since the sealant is forced to cure when it reaches the 195°F cure temperature, impregnated parts may be tested immediately after impregnation. Thermal cure sealants also will be less reactive and have a much longer pot life than anaerobic sealants.
The other morning I was walking the dog around 5:00 AM, and I noticed how exceptionally crisp and brilliant the stars were in the pre dawn sky, shining though the high pressure system overhead. While finishing the walk around the neighborhood, I thought about mankind’s worldview that the earth was flat as recent as 600 years ago and the reluctance of decision makers of that time, influenced by the rhetoric of naysayers, to accept anything other than the status quo.
(more…)