Vacuum impregnation seals the porosity in metal castings, thus making leaky castings pressure tight. But how exactly does it work? The following demonstrates the 4 steps to the vacuum impregnation process.
Step 1
The part is first placed into the impregnation chamber (also known as an autoclave, pressure vessel or vacuum vessel) and air is evacuated from the leak path by using a deep vacuum. The evacuated leak path is filled with sealant by covering the part with the sealant and applying pressure. More energy is required to penetrate the porosity with sealant than to evacuate the air.
Note – Porosity with no leak path to either surface will remain ‘enclosed’ as there is no way for the air or sealant to penetrate the material.
Step 2
In the recovery station (also known as drain station, centrifuge) excess sealant is recovered for reuse.
Step 3
In the wash/rinse station (also known as surge station, rolling rinse or pump over station) residual sealant is washed from the part’s internal passages, taps, pockets and features where sealant is undesirable.
Step 4
In the cure station (also known as standing, rolling cure or pump over station) the sealant, impregnated into the walls of the part, is polymerized in the leak path.
Final Part
As shown in purple, the porosity is fully sealed without changing dimensional or functional characteristics.
Conclusion
The intent of impregnation is to eliminate any leak paths so that fluids or gases do not migrate out of the part. To learn more about vacuum impregnation, download our eBook.
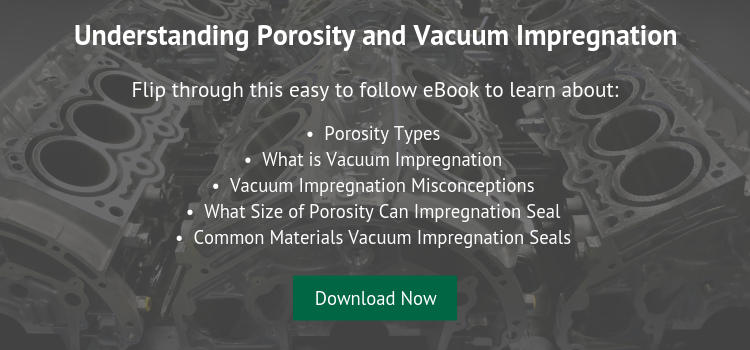